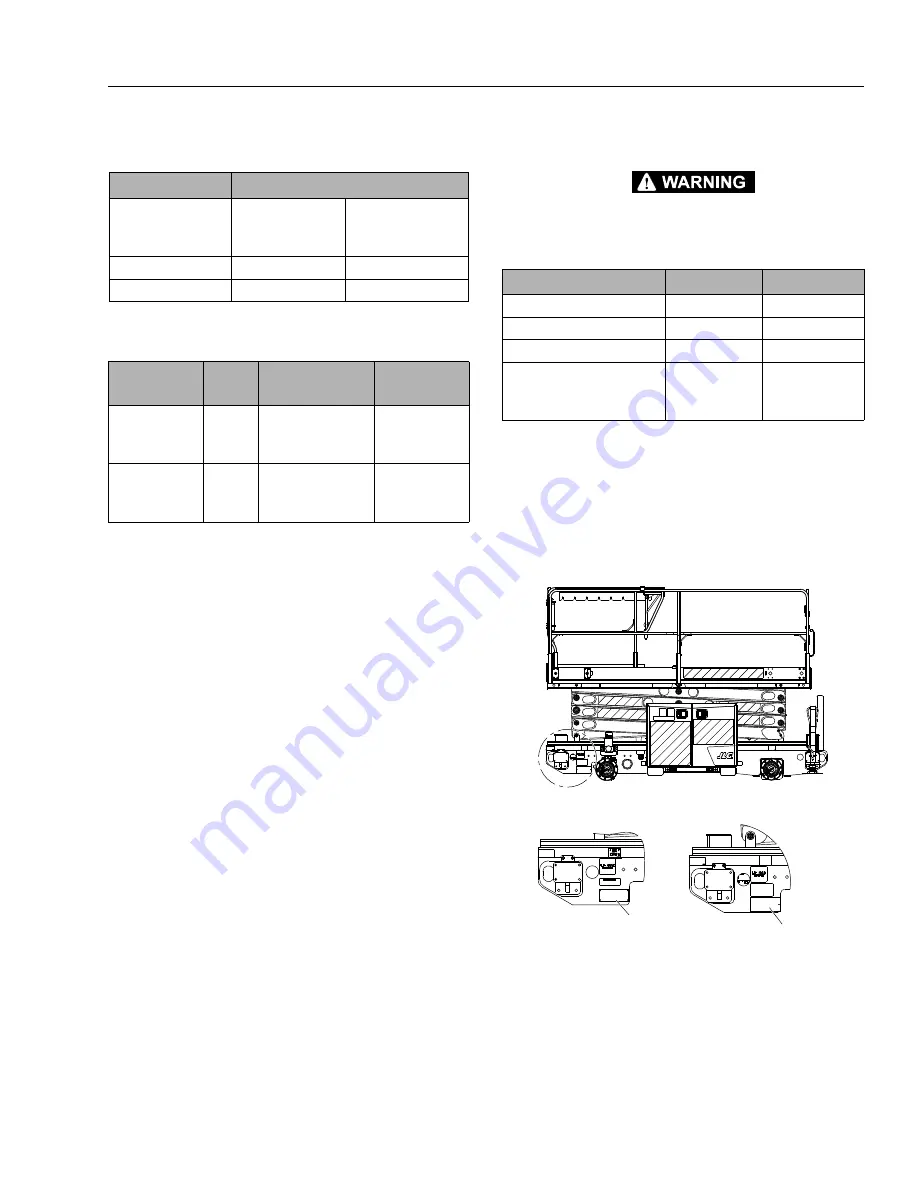
SECTION 1 - SPECIFICATIONS
31215923
1-3
Batteries (For ERT)
Tires
Critical Stability Weights
DO NOT REPLACE ITEMS CRITICAL TO STABILITY WITH ITEMS OF DIF-
FERENT WEIGHT OR SPECIFICATION (FOR EXAMPLE: FILLED TIRES,
ENGINE). DO NOT MODIFY UNIT IN ANY WAY TO AFFECT STABILITY.
1.2
SERIAL NUMBER LOCATION
For machine identification, the serial number will be
stamped in the frame on the front right of the machine.
In addition, should the serial number plate be damaged
or missing, the machine serial number tag is on the
front.
Specification
Lead Acid
Voltage
Total
Per Battery
48 V
6 V
48 V
6 V
Amp Hour Rating
310 Amp @20 hr
225 Amp @20 hr
Reserve Capacity
675 minutes
447 minutes
Size
Ply
Rating
Foam Fill Tire
Assembly Rating
Wheel Nut
Torque
26 X 12 Foam Filled
10
70 PSI @ 8400 lb
(3810 kg) - Static load
170 ft. lb s.-
Dry
(230.5 Nm)
26 X 12 Foam Filled
(Non-Marking)
10
70 PSI @ 8400 lb
(3810 kg) - Static load
170 ft. lbs. -
Dry
(230.5 Nm)
Component
RT
ERT
Wheel and Tire (each), Foam Filled
188 lb (85.3 kg)
188 lb (85.3 kg)
Engine Only (Kubota - Diesel)
227.3 lb (103.2 kg)
236 lb (107 kg)
Engine Only (Kubota - Gas/LP)
162 lbs (73.6 kg)
-
Battery
GC-110-WNL
For 6V-305-S
-
63 lb (28.6 Kg)
87 lb (39.5 Kg)
Figure 1-1. Serial Number Location
1. Serial Number Plate
MAF41950
1
1
SEE DETAIL A
DETAIL A
FOR CE/AUS MARKET
DETAIL A
Summary of Contents for ERT2669
Page 2: ......
Page 4: ...INTRODUCTION A 2 31215923 REVISON LOG Original Issue A January 08 2021...
Page 12: ...viii 31215923 TABLE OF CONTENTS...
Page 40: ...SECTION 1 SPECIFICATIONS 1 22 31215923...
Page 58: ...SECTION 2 GENERAL 2 18 31215923...
Page 187: ...SECTION 4 BASIC HYDRAULIC INFORMATION SCHEMATICS 31215923 4 11...
Page 206: ...SECTION 4 BASIC HYDRAULIC INFORMATION SCHEMATICS 4 30 31215923...
Page 225: ...SECTION 4 BASIC HYDRAULIC INFORMATION SCHEMATICS 31215923 4 49...
Page 242: ...SECTION 4 BASIC HYDRAULIC INFORMATION SCHEMATICS 4 66 31215923...
Page 307: ...SECTION 5 JLG CONTROL SYSTEM 31215923 5 65...
Page 334: ...SECTION 6 LSS SETUP CALIBRATION SERVICE 6 12 31215923...
Page 362: ...SECTION 7 GENERAL ELECTRICAL INFORMATION SCHEMATICS 7 28 31215923...
Page 374: ...SECTION 7 GENERAL ELECTRICAL INFORMATION SCHEMATICS 7 40 31215923...
Page 375: ......