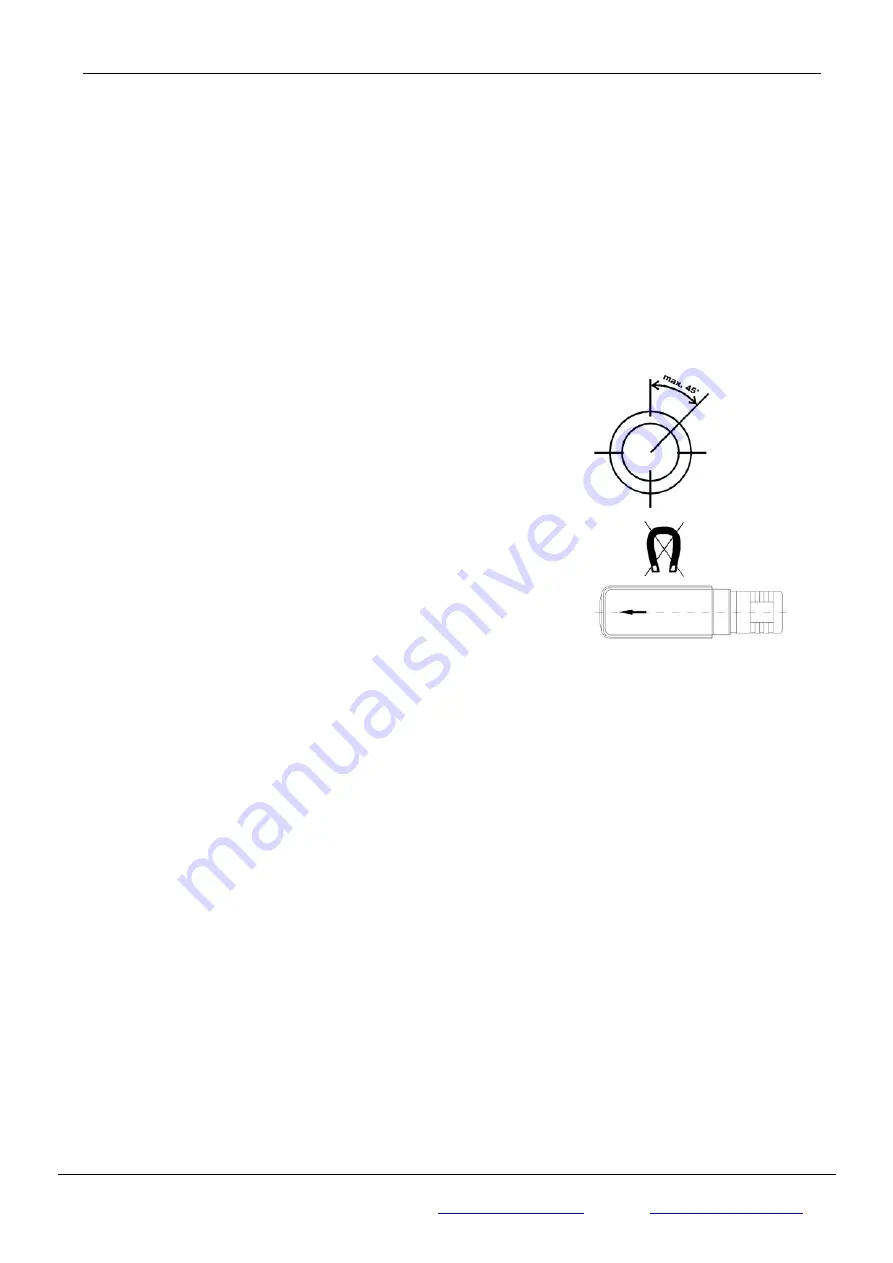
4 Flow Switch Installation
Flow switch
4 Flow Switch Installation
4.1 Mechanical installation
4.1.1 General installation instructions
⇒
When choosing the installation site, ensure that the specified limit values (see “Technical data”) are not
exceeded.
⇒
Select suitable measures to prevent the medium from freezing.
If the flow switch is to be used in ambient temperatures of <4°C, do not carry out any operation
beforehand with pure water, e.g. a test run. Residual water in the flow switch can result in frost damage.
⇒
Firstly, clean the pipe system in which the flow switch is to be installed and remove any magnetic
particles, e.g. welding residue.
⇒
The straight in- and outlet pipe (in front of and behind the flow switch) has to be at least
5 x DN.
⇒
The nominal installation position of the flow switch is an “upright
standing position” in horizontal pipework.
⇒
The switches should only be installed in a vertical position, deviation
max. 45° (Fig. 1).
⇒
Please contact the manufacturer if other installation positions are
desired.
⇒
Please make sure that there are no external magnetic fields in the
immediate vicinity of the flow switch, since these can impair device
functioning (Fig. 2).
⇒
There is an arrow on the flow switch. Ensure that this arrow is
parallel with the pipe shaft and is facing in the direction of flow
during installation (Fig. 2).
⇒
The brass and stainless steel union nuts ¾“BSP (version VH...)
have a tightening torque of 25...30 Nm.
⇒
The plastic union nuts (version VK...) have a tightening torque of 7...8 Nm.
Additional information for flow switch version VH...X
⇒
Please observe the specified limit values when choosing the installation site (see “Technical Data”).
⇒
When installing and before starting-up, it is to be guaranteed that the mechanical process connections are
technically tight.
⇒
Always consider the impermeability of the screwing elements for the zone allocation. Depending on the
operating conditions, it may be necessary to regularly check the impermeability of the screwing elements.
Fig. 1
Fig. 2
Page 6 of 15
Copyright © Jlso Tec Trade GmbH
JLSO Tec Trade GmbH
In den Birken 98
Fon:
+49 (0)
6369 230 9961
info@jlso-tec-trade.de
Fax:
+49 (0)
6369 230 9963
https://jlso-tec-trade.de
Daniel
H.
Meckel
D-66999
Hinterweidenthal