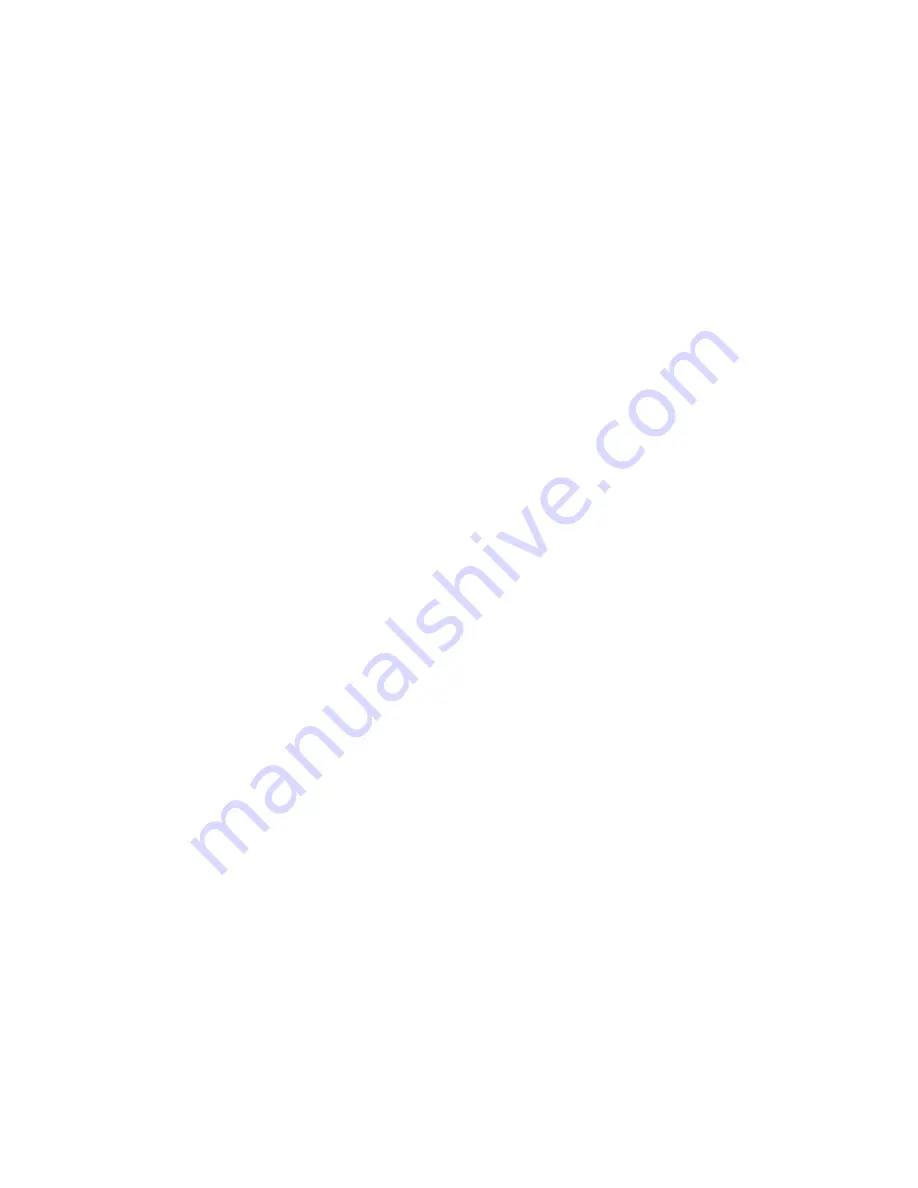
3901726
JobSmart 4 Gallon Air Compressor Assembly & Operating Instructions
10
MAINTENANCE
Daily (or before each use)
1. Check oil level
2. Drain condensation from the air tank.
3. Check for any unusual noise or vibration.
4. Be sure all nuts and bolts are tight.
Weekly
1. Clean breather hole on Oil Breather Cap.
Monthly
1. Inspect air system for leaks by applying soapy water to all joints. Tighten these joints if leaks are discovered.
6 Months (or after 250 hours of operation - whichever comes first)
1. Change Air Compressor Oil. Note: Change oil more often if Air Compressor is used near paint spraying
operations or in dusty environments.
Checking the Air Compressor Oil
1. Place Air Compressor on level surface. The oil level should be at the red dot on the Oil Sight Glass.
2. If oil level is low, remove Oil Breather Cap and add enough oil to bring the oil level to the red
dot on the Oil Sight Glass.
3. Replace Oil Breather Cap before starting compressor.
Changing the Air Compressor Oil
Note: This compressor uses only SAE 5W-30 motor oil.
1. Remove the Drain Plug under the Oil Sight Glass by turning the nut counterclockwise with wrench.
Note: Oil will begin to drain as Drain Plug is loosened. Place a funnel and oil pan in place BEFORE loosening
Drain Plug.
2. Once Drain Plug is removed, tilt Air Compressor backwards to allow all of the oil to drain out of
the crankcase.
3. Once oil is drained, replace Drain Plug and securely tighten in place with a wrench. Be careful not to
overtighten the Drain Plug, as this could damage the rubber seal.
4. Place Air Compressor on level surface.
5. Remove the Oil Breather Cap.
6. Slowly pour the oil into the oil fill hole, until the oil level rises to the center of the red dot on the Oil Sight Glass.
7. Install the Oil Breather Cap into the oil fill hole.
8. Firmly hand tighten the Oil Breather Cap by turning clockwise.
Always inspect the tool before use, and make sure it is in good working condition. Make sure all air
vents are clear, (use compressed air to clean the machine where possible). Check the power cable to
make sure it is intact and free from cracks, bare wires etc. Avoid using solvents when cleaning plastic parts.
Most plastics are susceptible to damage from the various types of commercial solvents.