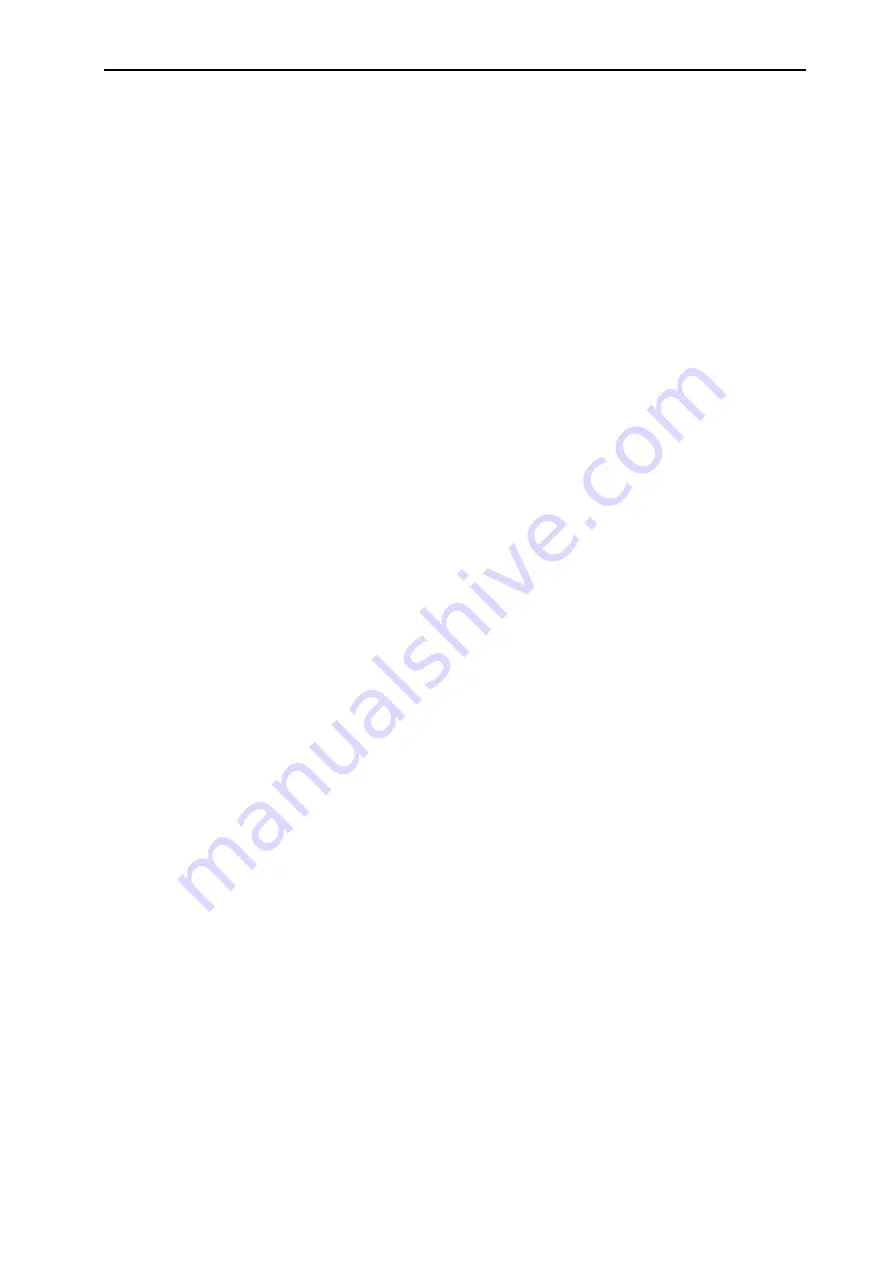
DINAMAP*
Compact
Vital Signs Monitor
21
Upon clearance of the overpressure condition the Main Board system processor can reset the
overpressure latch in GAL IC1 on the PSU Board, by asserting PNEU_RESET signal high, in order that
another determination can be carried out.
2.4.5 SpO
2
System (TS model only)
Blood oxygen saturation and pulse determinations can be made (DINAMAP*
Compact
TS only) using a
Nellcor Puritan Bennett
TM
finger sensor. This connects to the SpO
2
module fitted inside a shielded case
mounted in the monitor. This module is supplied as a complete replaceable part, no service being
possible.
The SpO
2
module communicates with the system processor via an isolated two wire serial interface.
Data signals from the system processor (SPO2_TX) are isolated by opto-coupler PC6. From here they
enter connector PL13 to the SpO
2
module. Likewise, data transmitted from the SpO
2
module are
isolated by opto-coupler PC5, from where it is routed to the system processor as signal SPO2_RXD.
The SpO
2
module (and the temperature determination circuit) is powered via an isolated power supply
module PM100. This is powered from the +12VV supply and generates the is5VI, +9VI and -
9VI supplies (+5VI, +15VI and -15VI supplies on revision 04 units and earlier). On revision 06 units the
isolated power supply module is switched on by the system processor SPO2_PSU_ON signal, turning
TR11 off and setting the control input to ML3 high. On revision 04 and earlier units the isolated power
supply module ML3 is turned on by grounding its -ve supply connection through FET TR12. In the event
of a FAILSAFE condition arising, the control signal of ML3 is set low by TR10 switching on (06 unit), or
by switching TR12 off (on revision 04 units and earlier).
2.4.6 Power Supply
The power supplies are generated and controlled on the power supply board 8620AB.
The power supply is designed to operate from both an external DC line source and from a 12 volt
rechargeable lead-acid battery. The supplied mains power converter provides 24 volt DC output.
When both supplies are present, the power supply will operate from the line supply if it is greater than
12 volts. If the line supply is greater than 16 volts the battery will be charged both when the monitor is
switched on and off. The power supply sequencing functions are controlled by the PIC IC5.
Incoming line power from the external power converter has any high voltage spikes snubbed by
transient suppresser D4 and over-voltage protection is provided by D6, R10 and CSR1. Should the line
input voltage rise above 34 volts, zener diode D6 conducts, turning on thyristor CSR1. This causes a
short circuit which blows the external DC line fuse. Reverse polarity protection for the power supply is
provided by blocking diodes D8 and D29. A sample of the line input voltage is taken by R3 and R6
(DC_INPUT), and routed to the external DC detection circuit IC16 and the PIC.
The switcher IC3, inductor L1 and diode D10 form a flyback converter with a nominal output of 15.1
volts and VRAW of 14.8 volts through the battery blocking diode D11. A sample of the smoothed
output is taken by R29 & R30 to provide a feedback voltage.
The PIC uses the DC_BATTERY, DC_INPUT and EXT_DC_ON signals to determine the available
power sources. If valid power supply conditions exist and a battery is detected, the PIC will turn on
TR7 which turns on p-channel FET TR6, allowing the +15VI line to charge the battery via D9, R17 and
FS1. When charging is taking place, a voltage will appear across R17, which will be proportional to the
charge current. This voltage is sampled by R14 & R15 to produce the BATTERY_C signal.
If there is no valid external DC line supply applied to the monitor, the monitor will default to use the
battery. DC from the rechargeable battery arrives on thermal fuse FS1, from where it is routed to the
source of TR2, a p-channel FET under the control of TR3. The battery supplies power to VRAW via
transistor TR2 and diode D28. When operating from a battery, VRAW will be in the range 10.4 - 13.5 V
depending on the battery charge. A sample of the battery’s terminal voltage is taken by R1 & R2 and
applied to the ADC input of the PIC (DC_BATTERY). From this, the PIC can determine the charge
state of the battery.