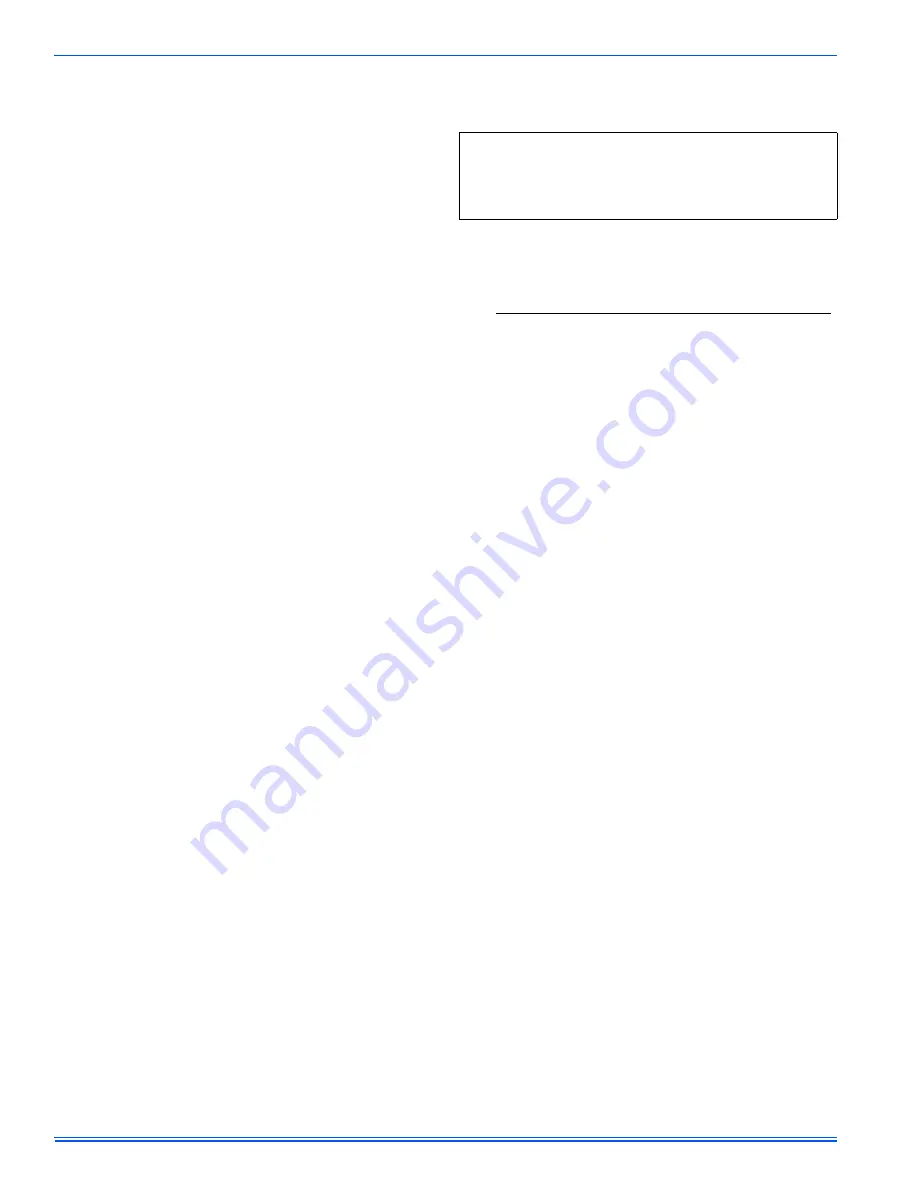
368261-UIM-B-1008
28
Johnson Controls Unitary Products
Four Red Flashes -
High limit switch open or defective temperature
sensor or 24 volt fuse is open. This may be caused by a dirty air filter,
improperly sized duct system, faulty blower motor, restricted circulating
airflow an open fuse on the control board.
Five Red Flashes -
Rollout switch or condensate pressure switch
open. Check the rollout switch(es) on the burner assembly. It is a man-
ual reset switch. To reset, push the small button in the center of the
switch. If it cannot be reset or if the switch trips again, contact a quali-
fied serviceman.
Six Red Flashes -
Current failure on modulating gas valve.
Seven Red Flashes -
Lockout due to no ignition. The control will try
three times for ignition. If flame cannot be established in three tries, the
control will lockout for one hour and then will try again to light. Check
gas supply, ignitor, gas valve, flame sensor.
Eight Red Flashes -
Lockout due to too many flame recycles. This
flash code occurs if flame is lost five times during a single heating cycle.
This could be caused by a faulty gas valve, low gas pressure, or dirty
flame sensor. The control will lock out for one hour and then will try
again.
Nine Red Flashes -
Reversed line polarity or improper grounding.
Check polarity of the incoming power to the furnace. Check the ground-
ing of the furnace, including the transformer ground and the L1 and
neutral connections.
Ten Red Flashes -
Gas valve circuit shorted. Check gas valve wiring. If
correct, replace gas valve.
Eleven Red Flashes -
Main blower failure - This flash code occurs
when the main limit opens and fails to reclose within five minutes, indi-
cating that the blower motor or blower wheel has failed.
Twelve Red Flashes -
ID plug is not present or not connected properly,
check for loose plug or loose wires in plug.
Steady On Red -
Control fault has been detected or there is 24 volts
present without 115 volts. Check that there is 24 volts and 115 volts
being supplied to the board. If so, then the board should be replaced.
DIAGNOSTIC FAULT CODE STORAGE AND
RETRIEVAL
The control in this furnace is equipped with memory that will store up to
five error codes to allow a service technician to diagnose problems
more easily. This memory will be retained even if power to the furnace
is lost.
Only a qualified service technician should use this feature.
The control stores up to five separate error codes. If more than five
error codes have occurred since the last reset, only the five most recent
will be retained. The furnace control board has a button, labeled
"LAST
ERROR"
that is used to retrieve error codes. This function will only
work if there are no active thermostat signals. So any call for heating,
cooling or continuous fan must be terminated before attempting to
retrieve error codes.
To retrieve the error codes, push the
LAST ERROR
button. The
LED
on
the control will then flash the error codes that are in memory, starting
with the most recent. There will be a two-second pause between each
flash code. After the error codes have all been displayed, the
LED
will
resume the normal slow green flash after a five second pause. To
repeat the series of error codes, push the button again.
If there are no error codes in memory, the
LED
will flash two green
flashes. To clear the memory, push the
LAST ERROR
button and hold it
for more than five seconds. The
LED
will flash three green flashes
when the memory has been cleared, then will resume the normal slow
green flash after a five-second pause.
IGNITION CONTROL FLAME SENSE LEVELS
Normal flame sense current is approximately
3.7 microamps DC (µa)
Low flame signal warning starts at 1.5 microamps.
Low flame signal control lockout point is
0.1 microamps DC (µa)