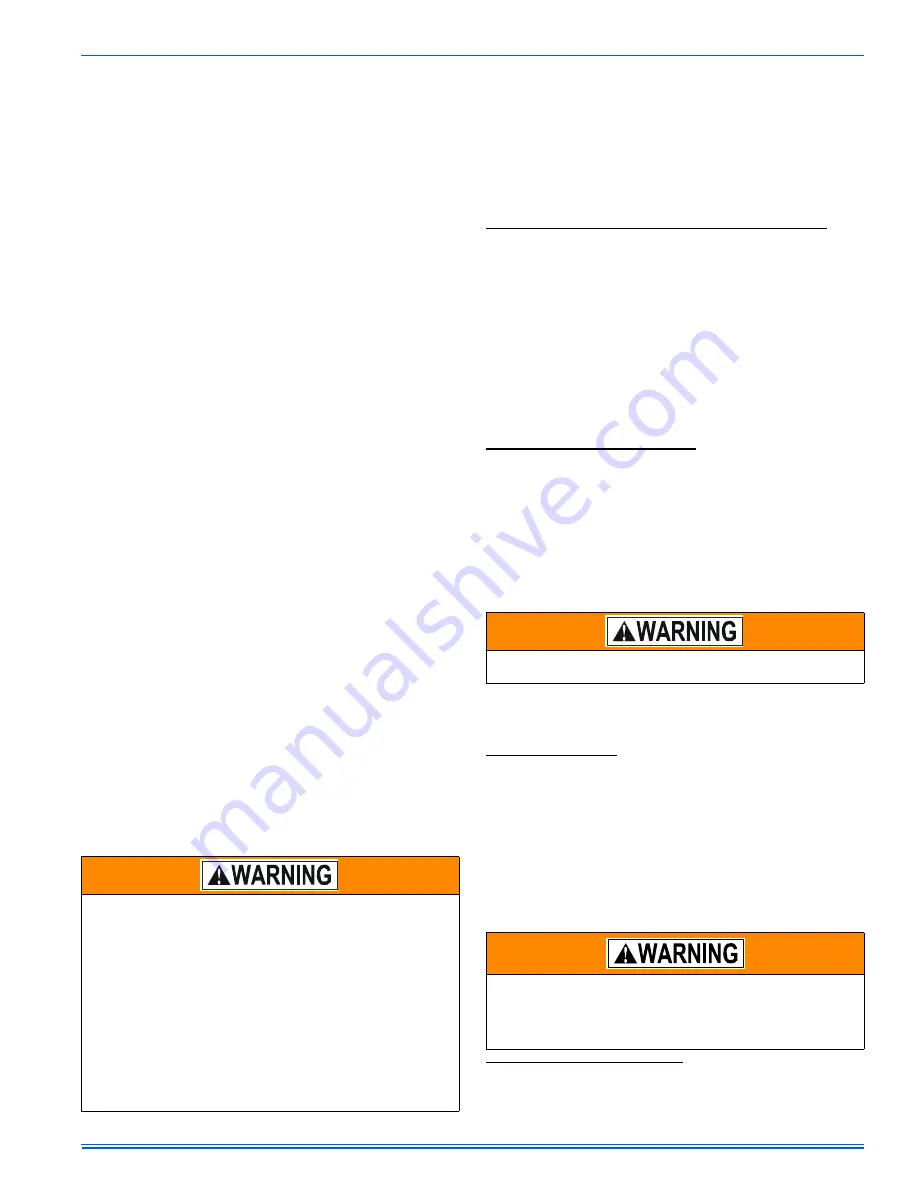
129098-UIM-G-0411
Johnson Controls Unitary Products
3
Manufactured homes in the U.S.A.:
•
Federal Manufactured Home Construction & Safety Standard
(H.U.D. Title 24, Part 3280).
•
National Fuel Gas Code (ANSI-Z223.1, NFPA-54).
•
National Electrical Code (NFPA 70).
Manufactured homes in Canada:
•
Natural Gas and Propane Installation Code (CAN/CSA B149.1).
•
Canadian Electrical Code, Part 1 (CSA C22.1)
Recreational Vehicles in U.S.A.:
•
Standard on Recreational Vehicles (NFPA 1192, formerly NFPA
501C).
•
National Electrical Code (NFPA 70).
Recreational Vehicles in Canada:
•
Unit installation shall comply with current CSA standard CAN/
CGA-Z240.4.2 - Installation Requirements for Propane Appli-
ances and Equipment in Recreational Vehicles.
•
Unit electrical wiring and grounding shall comply with current
CSA standard C22.2 No.148/CAN/CSA-Z240.6.2 - Electrical
Requirements for recreational vehicles.
COMBUSTION AIR QUALITY
(LIST OF CONTAMINANTS)
The furnace will require
OUTDOOR AIR
for combustion AT ALL TIMES,
INCLUDING any of the following environments.
•
Restricted Environments
•
Commercial buildings
•
Buildings with indoor pools
•
Laundry rooms
•
Hobby or craft rooms
•
Near chemical storage areas
•
Chemical exposure
This furnace requires
OUTDOOR AIR
for combustion AT ALL TIMES,
AS WELL AS where the furnace is being exposed to the following sub-
stances and / or chemicals.
•
Permanent wave solutions
•
Chlorinated waxes and cleaners
•
Chlorine based swimming pool chemicals
•
Water softening chemicals
•
De-icing salts or chemicals
•
Carbon tetrachloride
•
Halogen type refrigerants
•
Cleaning solvents (such as perchloroethylene)
•
Printing inks, paint removers, varnishes, etc.
•
Hydrochloric acid
•
Cements and glues
•
Antistatic fabric softeners for clothes dryers
•
Masonry acid washing materials
When outdoor air is used for combustion, the combustion air intake duct
system termination must be located external to the building and in an
area where there will be no exposure to the substances listed above.
INSPECTION
As soon as the furnace and/or accessories are received, it should be
inspected for damage during transit. If damage is evident, the extent of
the damage should be noted on the carrier’s freight bill. A separate
request for inspection by the carrier’s agent should be made in writing.
Also, before installation the furnace and/or accessories should be
checked for screws or bolts which have loosened in transit or shipping
and spacer brackets the need to be removed.
FURNACE LOCATION AND CLEARANCES
The furnace shall be located using the following guidelines:
1.
The furnace should be located where the roof jack can be installed
with out major modifications to the roof of the structure.
2.
As centralized with the air distribution as possible.
3.
Where there is access to fresh air particularly when the blend air
accessory will be installed.
4.
Where it will not interfere with proper air circulation in the confined
space.
5.
Where the outdoor roof jack terminal will not be blocked or
restricted. Refer to “VENT CLEARANCES” located in SECTION
VII of these instructions. These minimum clearances must be
maintained through out the installation.
6.
Where the unit will be installed in a level position with no more
than 1/4” (0.64 cm) slope side-to-side and front-to-back to provide
a proper roof jack connection and seal.
Installation in freezing temperatures:
1.
Furnace shall be installed in an area where ventilation facilities
provide for safe limits of ambient temperature under normal oper-
ating conditions. Ambient temperatures may fall below 32° F (0° C)
providing the flue temperature does not fall below 260° F (127° C)
at any point in the flue pipe. If the flue temperature falls below 260°
F (127° C) the flue products will condense in the vent pipe causing
the vent pipe to deteriorate rapidly.
2.
Do not allow return air temperature to be below 55º F (13° C) for
extended periods. To do so may cause condensation to occur in
the main heat exchanger, leading to premature heat exchanger
failure.
3.
If this furnace is installed in an unconditioned space and an
extended power failure occurs, there will be potential damage to
the internal components. Following a power failure situation, do
not operate the unit until inspection and repairs are performed.
Clearances for access:
Ample clearances should be provided to permit easy access to the unit.
The following minimum clearances are recommended:
1.
Twenty-four 24 inches (61 cm) between the front of the furnace
and an adjacent wall or another appliance, when access is
required for servicing and cleaning.
2.
Eighteen 18 inches (46 cm) at the side where access is required
for passage to the front when servicing or for inspection or
replacement of flue/vent connections.
In all cases, accessibility clearances shall take precedence over clear-
ances for combustible materials where accessibility clearances are
greater. See Table 1.
Installation in a residential garage:
A gas-fired furnace for installation in a residential garage must be
installed so the burner(s) and the ignition source are located not less
than 18 inches (46 cm) above the floor, and the furnace must be located
or protected to avoid physical damage by vehicles.
The furnace area must not be used as a broom closet or for any
other storage purposes, as a fire hazard may be created. Never
store items such as the following on, near or in contact with the fur-
nace.
1. Spray or aerosol cans, rags, brooms, dust mops, vacuum
cleaners or other cleaning tools.
2. Soap powders, bleaches, waxes or other cleaning com-
pounds; plastic items or
3. Containers; gasoline, kerosene, cigarette lighter fluid, dry
cleaning fluids or other volatile fluid.
4. Paint thinners and other painting compounds.
5. Paper bags, boxes or other paper products
Never operate the furnace with the blower door removed. To
do so could result in serious personal injury and/or equipment
damage.
Installation in an ambient below 32ºF (0.0° C) could create a haz-
ard, resulting in damage, injury or death.
Check the rating plate and power supply to be sure that the electri-
cal characteristics match. All models use nominal 115 VAC, 1
Phase 60Hz power supply.
Furnace shall be installed so the electrical components are pro-
tected from water.