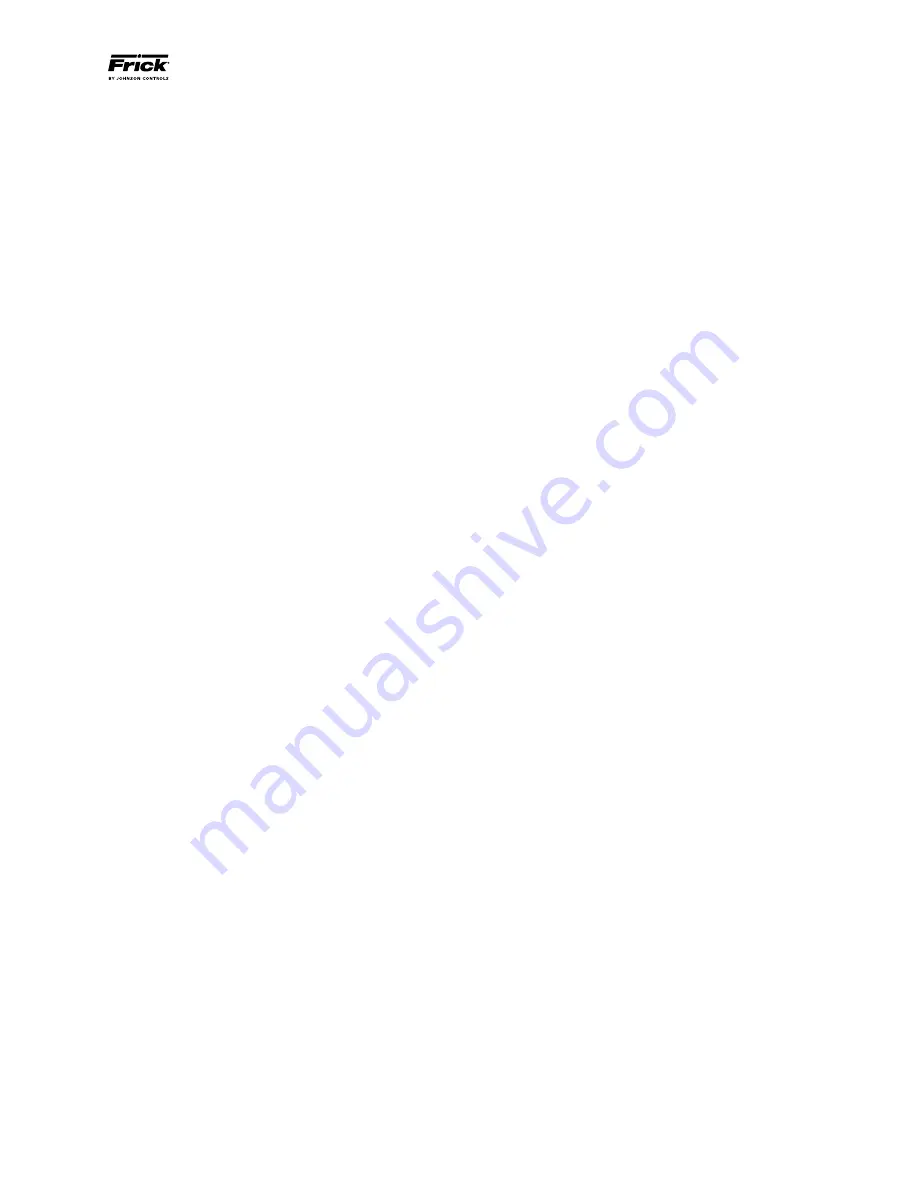
RWF ROTARY SCREW COMPRESSOR UNITS
MAINTENANCE
S70-600 IOM (OCT04)
Page 27
Pressure Gauge - Discharge Port
1.
High reading would indicate:
a. High viscosity and small and/or long discharge line.
b. Gate valve partially closed.
c. Filter plugged.
d. Vertical head did not consider a high specific gravity
liquid.
e. Line partially plugged from buildup on inside of pipe.
f. Liquid in pipe not up to temperature.
g. Liquid in pipe has undergone a chemical reaction and
has solidified.
h. Relief valve set too high.
2.
Low reading would indicate:
a. Relief valve set too low
b. Relief valve poppet not seating properly.
c. Too much extra clearance.
d. Pump worn.
3.
Fluttering, jumping, or erratic reading:
a. Cavitation.
b. Liquid coming to pump in slugs.
c. Air leak in suction line.
d. Vibrating from misalignment or mechanical prob-
lems.
Some of the following may also help pinpoint the problem:
1.
Pump does not pump.
a. Lost its prime - air leak, low level in tank
.
b. Rotating in wrong direction.
c. Motor does not come up to speed.
d. Suction and discharge valves not open.
e. Strainer clogged.
f. Relief valve set too low, relief valve poppet stuck
open.
g. Pump worn out.
h. Any changes in the liquid system, or operation that
would help explain the trouble, e.g. new source of sup-
ply, added more lines, inexperienced operators, etc.
i. Tighten end clearance.
j. Head position incorrect.
2.
Pump starts, then loses its prime.
a. Low level in tank.
b. Liquid vaporizing in the suction line.
c. Air leaks or air pockets in the suction line; leaking air
through packing or mechanical seal.
d. Worn out.
3.
Pump is noisy
a. Pump is being starved (heavy liquid cannot get to
pump fast enough). Increase suction pipe size or
reduce length.
b. Pump is cavitating (liquid vaporizing in the suction
line). Increase suction pipe size or reduce length; if
pump is above the liquid, raise the liquid level closer
to the pump; if the liquid is above the pump, increase
the head of liquid.
c. Check alignment.
d. May have a bent shaft or rotor tooth. Straighten or
replace.
e. May be a foreign object trying to get into the pump
through the suction port.
4.
Pump not up to capacity
a. Starving or cavitating - increase suction pipe size or
reduce length.
b. Strainer partially clogged - clean.
c. Air leak in suction piping or along pump shaft.
d. Running too slowly - is motor the correct speed and
is it wired up correctly
e. Relief valve set too low or stuck open.
f. Pump worn out.
g. Tighten end clearance.
h. Head position incorrect.
5.
Pump takes too much power.
a. Running too fast - is correct motor speed, reducer
ratio, sheave size, etc. being used.
b. Liquid more viscous than unit sized to handle - heat
the liquid, increase the pipe size, slow the pump down,
or get a bigger motor.
c. Discharge pressure higher than calculated - check
with pressure gauge. Increase size or reduce length of
pipe, reduce speed (capacity), or get bigger motor.
d. Pump misaligned.
e. Extra clearance on pumping elements may not be
suffi cient for operating conditions. Check parts for
evidence of drag or contact in pump and increase
clearance where necessary
6.
Rapid Wear.
Examination of a pump that has gradually lost its ability
to deliver capacity or pressure would show a smooth
wear pattern on all parts. Rapid wear shows up as heavy
grooving, galling, twisting, breaking, or similar severe
signs of trouble.
PREVENTATIVE MAINTENANCE
Performing a few preventative maintenance procedures will
extend the life of your pump and reduce the cost per gallon
pumped.
1. Lubrication
- Grease all zerks after every 500 hours of
operation or after 60 days, whichever occurs first. If service
is severe, grease more often. Do it gently with a hand gun.
Use #2 ball bearing grease for normal applications. For hot
or cold applications, use appropriate grease.
2. Packing Adjustment
- Occasional packing adjustment
may be required to keep leakage to a slight weep; if im-
possible to reduce leakage by gentle tightening, replace
packing or use different type. See Technical Service Manual
on particular model series for details on repacking.
3. End Clearance Adjustment
- After long service the run-
ning clearance between the end of the rotor teeth and the
head may have increased through wear to the point where
the pump is losing capacity or pressure. Resetting end clear-
ance will normally improve pump performance. See Technical
Service Manual on particular model series for procedure on
adjusting end clear ance for the pump involved.