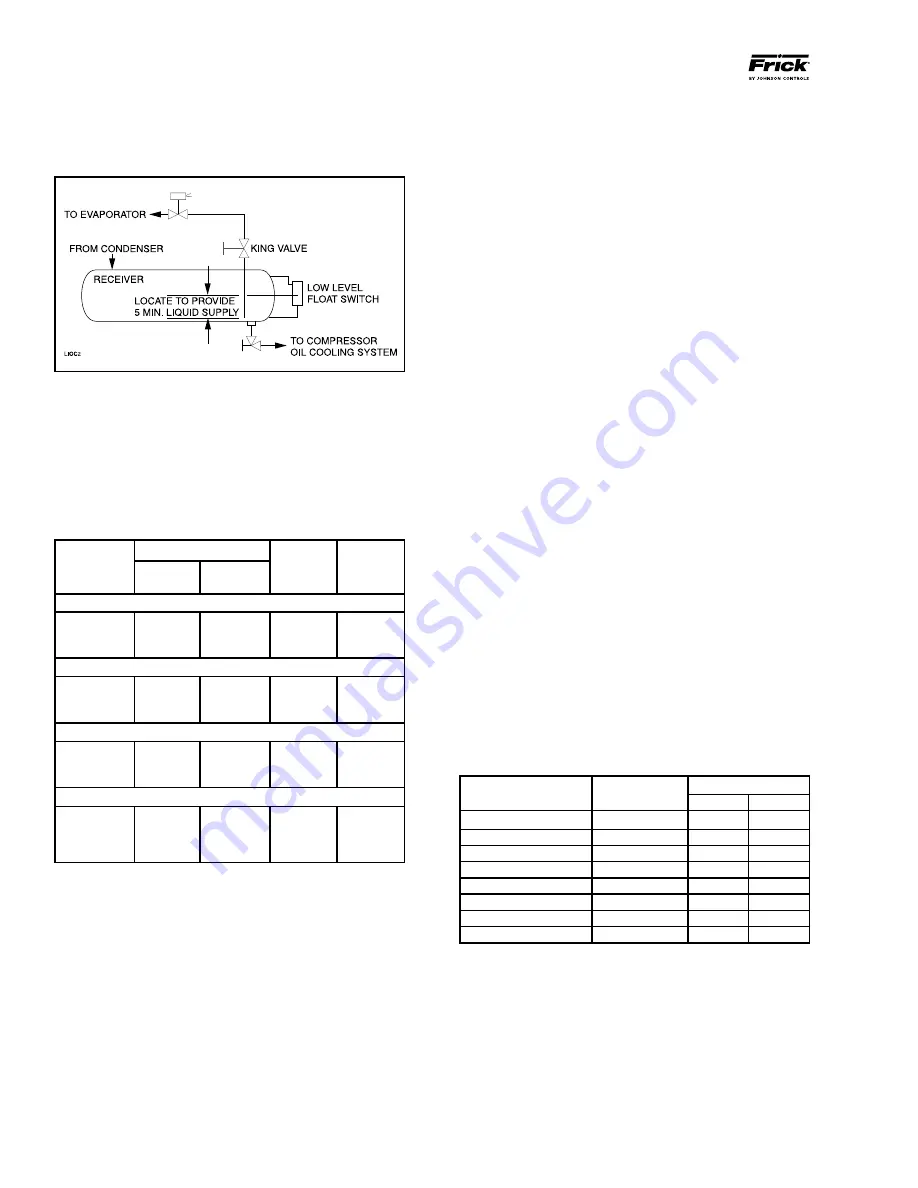
RWF ROTARY SCREW COMPRESSOR UNITS
INSTALLATION
S70-600 IOM (OCT04)
Page 8
WATER-COOLED OIL COOLING (OPTION AL)
The plate and shell type water-cooled oil cooler is mounted
on the unit complete with all oil piping. The customer must
supply adequate water connections and install the two-way
water regulating valve if ordered in lieu of a three-way oil
temperature valve. It is recom mended (local codes permitting)
that the water regula tor be installed on the water outlet con-
nection. Insert the water regulator valve bulb and well in the
chamber provided on the oil outlet connection. Determine
the size of the water-cooled oil cooler supplied with the unit,
then refer to table for the water connec tion size.
The water
supply must be sufficient to meet the required flow.
Frick recommends a closed-loop system for the waterside
of the oil cooler. Careful attention to water treatment is es-
sential to ensure adequate life of the cooler if cooling tower
water is used.
It is imperative that the condition of cool-
ing water and closed-loop fluids be analyzed regularly
and as necessary and maintained at a pH of 7.4, but not
less than 6.0 for proper heat exchanger life.
After initial
start-up of the compressor package, the strainer at the inlet
of the oil cooler should be cleaned several times in the first
24 hours of operation.
In some applications, the plate and shell oil cooler may be
subjected to severe water conditions, including high tem-
perature and/or hard water conditions. This causes accel-
erated scaling rates which will penalize the performance of
the heat exchanger. A chemical cleaning process will extend
the life of the Plate and Shell heat exchanger. It is important
to establish regular cleaning schedules.
Cleaning:
A 3% solution of Phosphoric or Oxalic Acid is
recommended. Other cleaning solutions can be obtained from
your local distributor, but they must be suitable for stainless
steel. The oil cooler may be cleaned in place by back flushing
with recommended solution for approximately 30 minutes.
After back flushing, rinse the heat exchanger with fresh water
to remove any remaining cleaning solution.
NOTE: The water-regulating valve shipped with the unit
will be sized to the specific flow for the unit.
OIL COOLER DATA TABLE
RWF
TYPICAL
CONNECTION
MODEL
COOLER
INLET OUTLET
100/134 High Stage
116 Plates
3"
3"
100 - 270 Booster
66 Plates
2"
2"
177/222 High Stage
190 Plates
3"
3"
270 High Stage
288 Plates
3"
4"
316/399 Booster
56 Plates
3"
3"
316/399 High Stage
136 Plates
4"
5"
480 Booster
72 Plates
3"
3"
480 High Stage
188 Plates
4"
5"
* Based on 100 foot liquid line. For longer runs, increase line
size accordingly.
LIQUID LINE SIZES/RECEIVER VOLUME
Liquid line sizes and the additional receiver volume (quanti-
ty of refrigerant required for 5 minutes of liquid injection oil
cooling) are given in the following table:
LIQUID LINE SIZE and RECEIVER VOLUME
LINE SIZE*
POUND
LIQUID
RWF
SCH 80
OD
PER
VOLUME
MODEL
PIPE
TUBING
5 MIN.
CU FT
R-717
HIGH STAGE*
100-134
3/4
–
80
2.0
177-270
1
–
140
4.0
316-480
1-1/4
–
250
7.0
R-717
BOOSTER*
100-134
1/2
–
20
0.5
177-270
3/4
–
30
1.0
316-480
1
–
40
1.5
R-22
HIGH STAGE*
100-134
1-1/4
1-1/8
290
4.0
177-270
1-1/2
1-3/8
570
8.0
316-480
2
2-1/2
1,050
14.0
R-22
BOOSTER*
100-134
3/4
7/8
44
0.6
177-270
3/4
7/8
59
0.8
316-480
3/4
7/8
92
1.2
The level-control method (Figure 5) utilizes a float level
control on the receiver to close a solenoid valve feeding the
evaporator when the liquid falls below that amount necessary
for 5 minutes of liquid injection oil cooling.
Figure 5