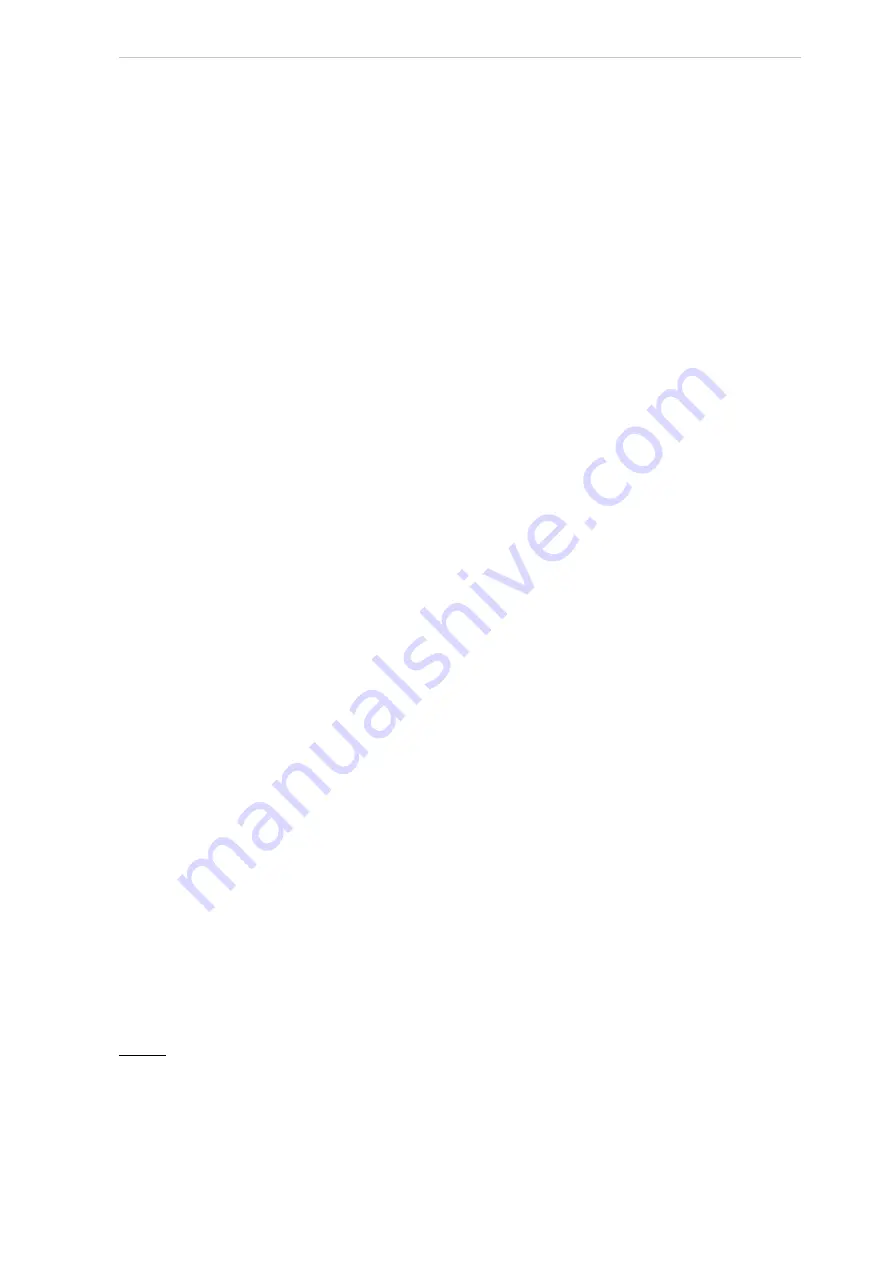
Operating manual- SAB 355 (including ATEX)
26/63
004059 en 2019.11
5. Installation
Installation in terms of mechanical work (refrigeration system and piping), electrical work and in-
stallation of safety equipment must be performed in accordance with local codes/rules and/or ac-
cording to EN 378-3 and EN 378-4 as a minimum requirement.
The pressure loss in the downstream line from the safety valve must meet the values stated in EN
13136 to which EN 378 is referring. The data necessary to dimension the line in accordance with
this standard is stated in the data sheet for your particular unit in the beginning of this manual.
Make sure that all necessary documents are available including declarations, certificates, identifi-
cation plates, manuals, machine card, log books etc. and/or other documentation required ac-
cording to local rules and/or EN 378.
The main issues/check points for installation of the compressor unit are as follows:
1.
Lifting the unit. Only use the lifting lugs marked with red.
Warning!
This screw compressor unit may be
top-heavy
. Use caution to prevent it from
turning over.
2.
Place the unit with sufficient free space for operation and maintenance.
3.
Place the unit on a foundation suitable for the actual load and vibrations with or without vi-
bration dampers according to the vibration design strategy.
4.
Welding on suction piping, discharge piping and other oil cooling system pipings. The pip-
ing design must include proper design considerations regarding function, vibrations, ther-
mal expansion and pre-stress after welding in order to avoid high load on the compressor
unit connections.
5.
Leak and pressure test according to the applied/local codes and rules. Isolate the com-
pressor unit from the test pressure or disconnect pressure transducers and safety valves.
Never exceed the test pressure of the unit stated on the unit name plate.
6.
Connect power supply wiring (compressor motor, oil pump motor (optional) and control
system) according to electrical diagrams.
7.
Make a final check of all relevant components, connections, electrical connections, safety
functions, meaning safety valve, safety high pressure cut-out (below compressor safety
overflow valve and not above 0.9 x max. allowable pressure) and the machine room
safety equipment.
8.
Evacuate the unit.
9.
Charge oil (type according to SABROE oil recommendation).
10. Charge refrigerant.
11. Connect power supply.
12. Set up the control system settings including calibration according to the control system
manual.
13. Check the direction of rotation of the compressor motor and oil pump (optional).
14. Mount the coupling.
ATEX:
On ATEX-executions, all electrical installations supplied with the compressor are in con-
formity with the ATEX directive. If the installations are expanded or additional equipment is
mounted, this must also be in conformity with the ATEX directive. For equipment not supplied by
Johnson Controls Denmark, it is the contractor who is responsible for ensuring that the equipment
is in conformity with the ATEX directive. Specifically, the contractor is responsible for equalising
potential differences on the compressor.