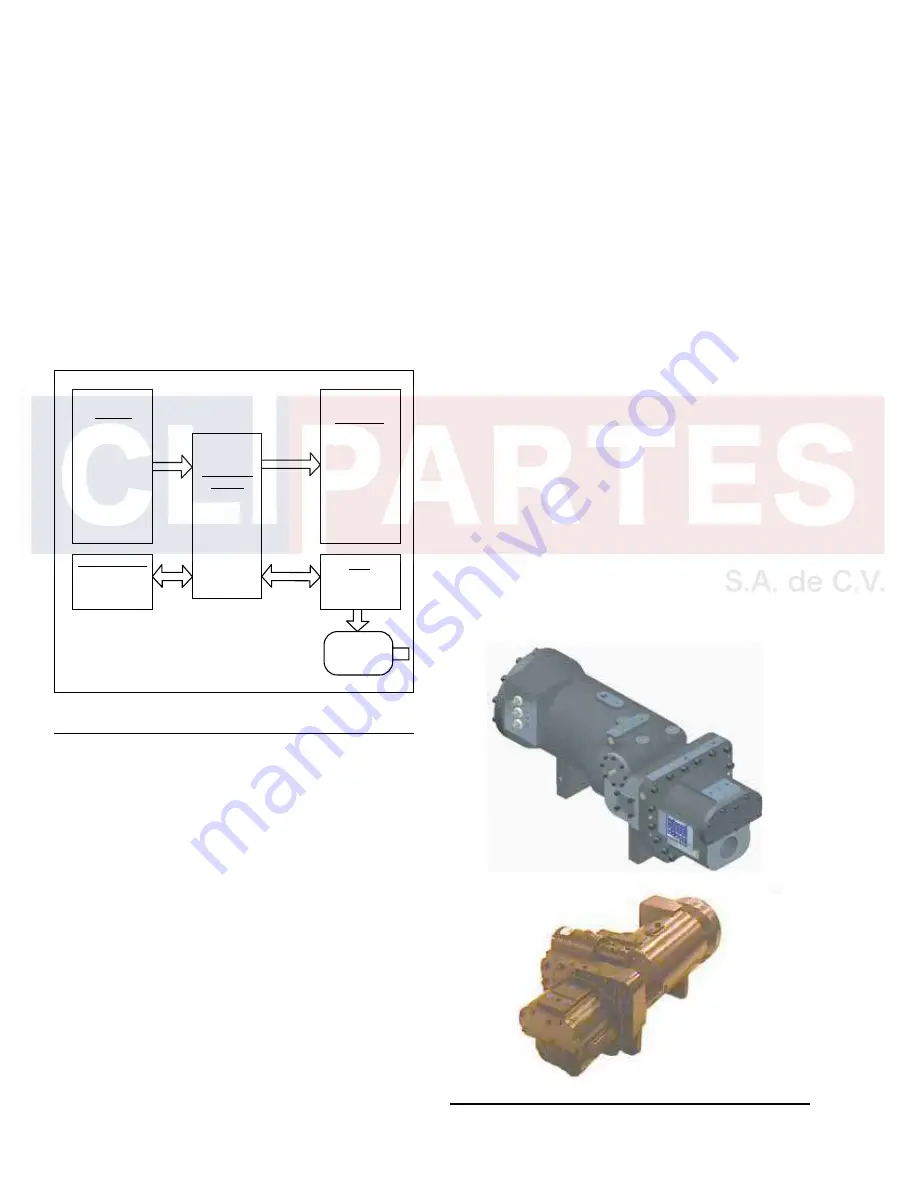
JOHNSON CONTROLS
24
FORM 201.23-NM2
ISSUE DATE: 3/9/2015
SECTION 2 - PRODUCT DESCRIPTION
An integral liquid cooled, transistorized, PWM, Vari-
able Speed Drive (VSD) is controlled by the chiller
microprocessor control panel to start/stop, select com-
pressors to run, and select compressor speed. Power
Factor is 95% at part or full load.
The chiller microprocessor communicates with the
VSD Logic Board via a 3-wire RS-485 opto coupled
data link. The VSD Logic Board runs the number of
compressors required to meet the load and the com-
pressors to the speed requested by the chiller micro-
processor.
The basic system control architecture is shown in the
diagram below:
CHILLER CONTROL SYSTEM
INPUTS
COMMUNICATIONS
OUTPUTS
VSD
MOTOR
CONTROL
PANEL
Pressure Transducers
Temperature Sensors
Level Sensor
Switches
Liquid Flow
High Pressure
Start/Stop
Customer Supplied
Contacts
(Chiller Control
Board)
Microprocessor
User Interface
Display
&
Keypad
Building Automation
Printer
Modem
VSD Logic Board
SCR Trigger Board
Power Components
PWM (Speed Control)
(Relay Output
Board)
Solenoids
Contactors
Alarm
Pump
Compressor Heater
Run Status
Evap Heater
LD10478
FIGURE 1 -
CHILLER CONTROL SYSTEM
The chiller is designed to operate in ambient tempera-
tures of 0°F to 125°F (-18°C to 52°C). Capacity control
is capable of reducing chiller capacity to 10% of full
load without the need for Hot Gas Bypass.
Compressor
The direct drive semi-hermetic rotary twin-screw MTS
compressor is designed for industrial refrigeration ap-
plications and ensures high operational efficiencies
and reliable performance. Capacity control is achieved
by stepless VSD speed changes. No slide valve is re-
quired. Smooth capacity control is achieved between
10% and 100% of chiller capacity in most operating
conditions. The compressor is a positive displacement
type characterized by two helically grooved rotors,
which are manufactured from forged steel. The 4 pole
motor operates at speeds up to 6000 RPM to direct
drive the male rotor, which in turn drives the female
rotor on a light film of oil.
Refrigerant gas is injected into the void created by the
un-meshing of the five lobed male and seven lobed fe-
male rotors. Further meshing of the rotors closes the
rotor threads to the suction port and progressively com-
presses the gas in an axial direction to the discharge
port. The gas is compressed in volume and increased
in pressure before exiting at a designed volume at the
discharge end of the rotor casing. Since the intake and
discharge cycles overlap, a resulting smooth flow of
gas is maintained.
The rotors are housed in a cast iron compressor hous-
ing precision machined to provide optimal clearances
for the rotors. Contact between the male and female
rotor is primarily rolling on a contact band on each of
the rotor’s pitch circle. This results in virtually no rotor
wear and increased reliability, a trademark of the screw
compressor.
The MTS compressor incorporates a complete anti-
friction bearing design for reduced power input and
increased reliability. Separated, cylindrical, roller bear-
ings handle radial loads. Angular-contact ball bearings
handle axial loads. Together they maintain accurate ro-
tor positioning at all pressure ratios, thereby minimiz-
ing leakage and maintaining efficiency.
LD10481
LD10482
FIGURE 2 -
COMPRESSOR
Summary of Contents for YCIV0157
Page 38: ...JOHNSON CONTROLS 38 FORM 201 23 NM2 ISSUE DATE 3 9 2015 THIS PAGE INTENTIONALLY LEFT BLANK ...
Page 42: ...JOHNSON CONTROLS 42 FORM 201 23 NM2 ISSUE DATE 3 9 2015 THIS PAGE INTENTIONALLY LEFT BLANK ...
Page 50: ...JOHNSON CONTROLS 50 FORM 201 23 NM2 ISSUE DATE 3 9 2015 THIS PAGE INTENTIONALLY LEFT BLANK ...
Page 333: ...JOHNSON CONTROLS 333 FORM 201 23 NM2 ISSUE DATE 3 9 2015 NOTES ...