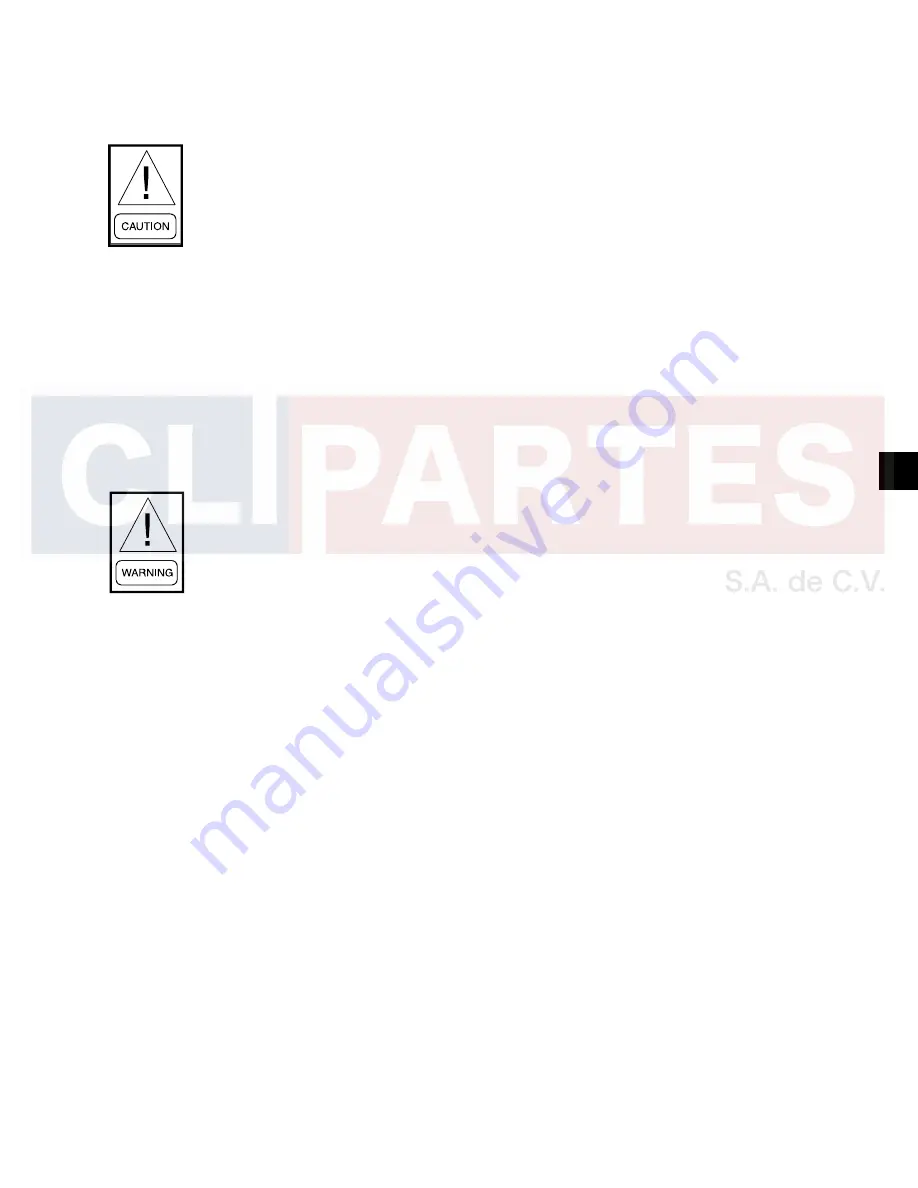
JOHNSON CONTROLS
51
FORM 201.23-NM2
ISSUE DATE: 3/9/2015
5
SECTION 5 - COMMISSIONING
PREPARATION
Commissioning of this unit should only
be carried out by Johnson Controls Au-
thorized personnel.
Commissioning personnel should be thoroughly famil-
iar with the information contained in this document be-
fore starting the unit.
Commission the unit using the detailed checks outlined
in the Equipment Pre Start-up and Start-up Checklist
on
.
PREPARATION – GENERAL
The following basic checks should be made with the
customer power to the unit switched OFF.
Proper electrical lock out and tag out
procedures must be followed.
Inspection
Inspect unit for installation damage. If found, take ac-
tion and/or repair as appropriate.
Refrigerant Charge
Packaged units are normally shipped as standard with
a full refrigerant operating charge. Check that refrig-
erant pressure is present in both systems and that no
leaks are apparent. If no pressure is present, a leak test
must be undertaken, the leak(s) located and repaired.
Remote systems and units are supplied with a nitrogen
holding charge. These systems must be evacuated with
a suitable vacuum pump/recovery unit as appropriate
to below 500 microns.
Do not liquid charge with static water in the cooler.
Care must also be taken to liquid charge slowly to
avoid excessive thermal stress at the charging point.
Once the vacuum is broken, charge into the condenser
coils with the full operating charge as given in
Service and Oil Line Valves
Open each compressor suction, economizer, and dis-
charge service valve. If valves are of the back-seat
type, open them fully (counterclockwise) then close
one turn of the stem to ensure operating pressure is fed
to pressure transducers. Open the liquid line service
valve and oil return line ball valve fully in each system.
Compressor Oil
To add oil to a circuit - connect a YORK hand oil pump
(Part No. 470-10654-000) to the 1/4" oil charging valve
on the oil separator piping with a length of clean hose
or copper line, but do not tighten the flare nut. Using
clean oil of the correct type (“L” oil), pump oil until all
air has been purged from the hose then tighten the nut.
Stroke the oil pump to add oil to the oil system. The oil
level should be between the middle of the lower and
middle of the upper sight glasses of the oil separator.
Approximately 4 to 5 gallons are present in each refrig-
erant system, with typically 1 to 2 gallons in each oil
separator. Oil levels in the oil separators above the top
sight glass in either oil separator should be avoided and
may cause excessive oil carryover in the system. High
oil concentration in the system may cause nuisance
trips resulting from incorrect readings on the level sen-
sor and temperature sensors. Temperature sensor errors
may result in poor liquid control and resultant liquid
overfeed and subsequent damage to the compressor.
Fans
Check that all fans are free to rotate and are not dam-
aged. Ensure blades are at the same height when ro-
tated. Ensure fan guards are securely fixed.
Isolation / Protection
Verify all sources of electrical supply to the unit are
taken from a single point of isolation. Check that the
maximum recommended fuse sizes given in
has not been exceeded.
Control Panel
Check the panel to see that it is free of foreign materi-
als (wire, metal chips, etc.) and clean out if required.
Power Connections
Check that the customer power cables are connected
correctly to the terminal blocks or optional circuit break-
er. Ensure that connections of power cables within the
panels to the circuit breaker or terminal blocks are tight.
Summary of Contents for YCIV0157
Page 38: ...JOHNSON CONTROLS 38 FORM 201 23 NM2 ISSUE DATE 3 9 2015 THIS PAGE INTENTIONALLY LEFT BLANK ...
Page 42: ...JOHNSON CONTROLS 42 FORM 201 23 NM2 ISSUE DATE 3 9 2015 THIS PAGE INTENTIONALLY LEFT BLANK ...
Page 50: ...JOHNSON CONTROLS 50 FORM 201 23 NM2 ISSUE DATE 3 9 2015 THIS PAGE INTENTIONALLY LEFT BLANK ...
Page 333: ...JOHNSON CONTROLS 333 FORM 201 23 NM2 ISSUE DATE 3 9 2015 NOTES ...