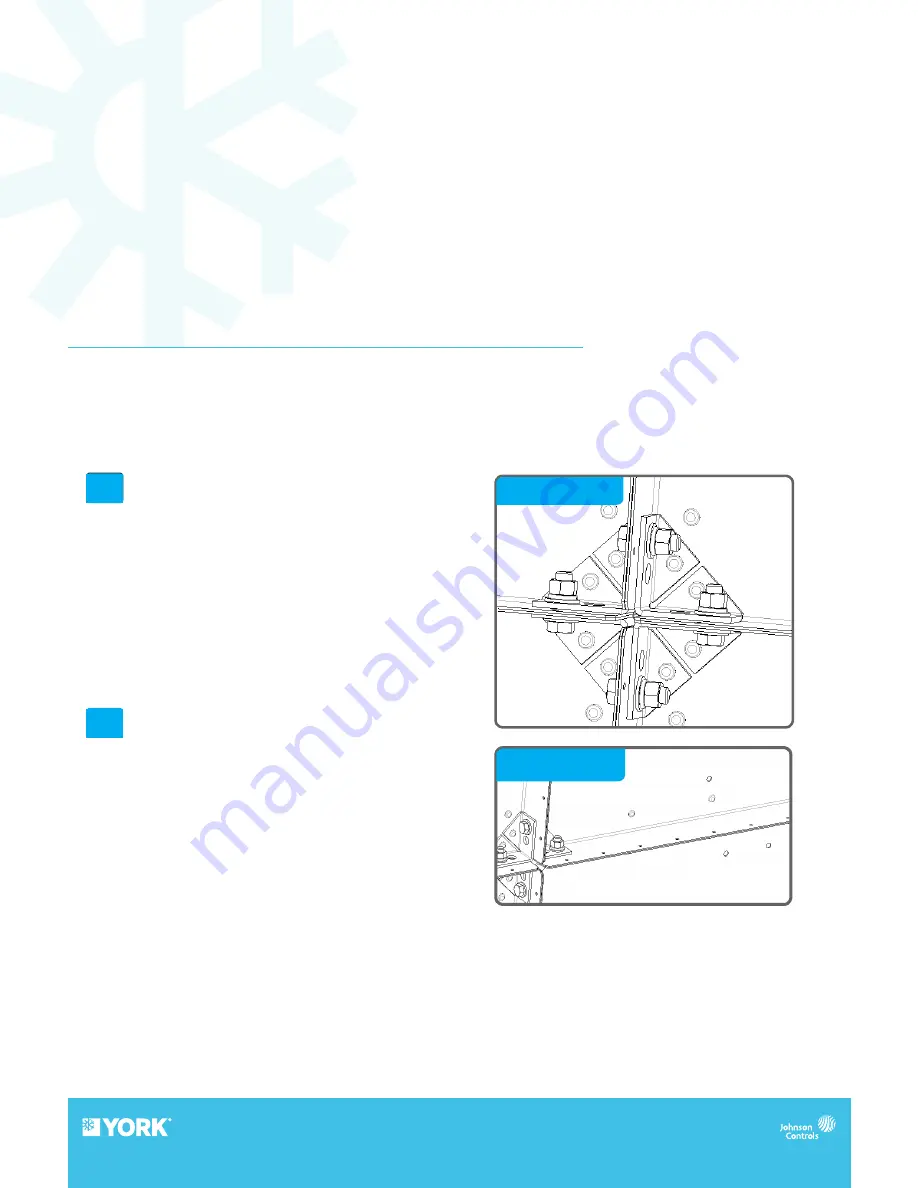
9
Installation (Continued)
YORK
®
STACK FAN
Top, Bottom and Side Connections
*Intake Side Shown
•
1/2-13 x 1.00 Grade 5 Hex Head Cap Screw (or
equivalent) 4 required (1 in each corner)
• 1/2 Flat Washer, 8 required (2 in each corner)
• 1/2-13 Hex Nut (or equivalent), 4 required (1 in each
corner). Recommended torque setting of 18 (ft-lb)
• Split Lock Washer (or equivalent), 4 required
(1 in each corner)
Middle Connections *Intake Side Shown
•
Intake Side Panel Connection:
A
series of
.22” diameter holes, 3” on center are provided to
connect the front panel of the fan assembly to the
customer’s equipment. The holes are sized for 1/4”
sheet metal screws.
•
All installation hardware supplied by end user.
A
B
A
*Intake Side
B
*Intake Side