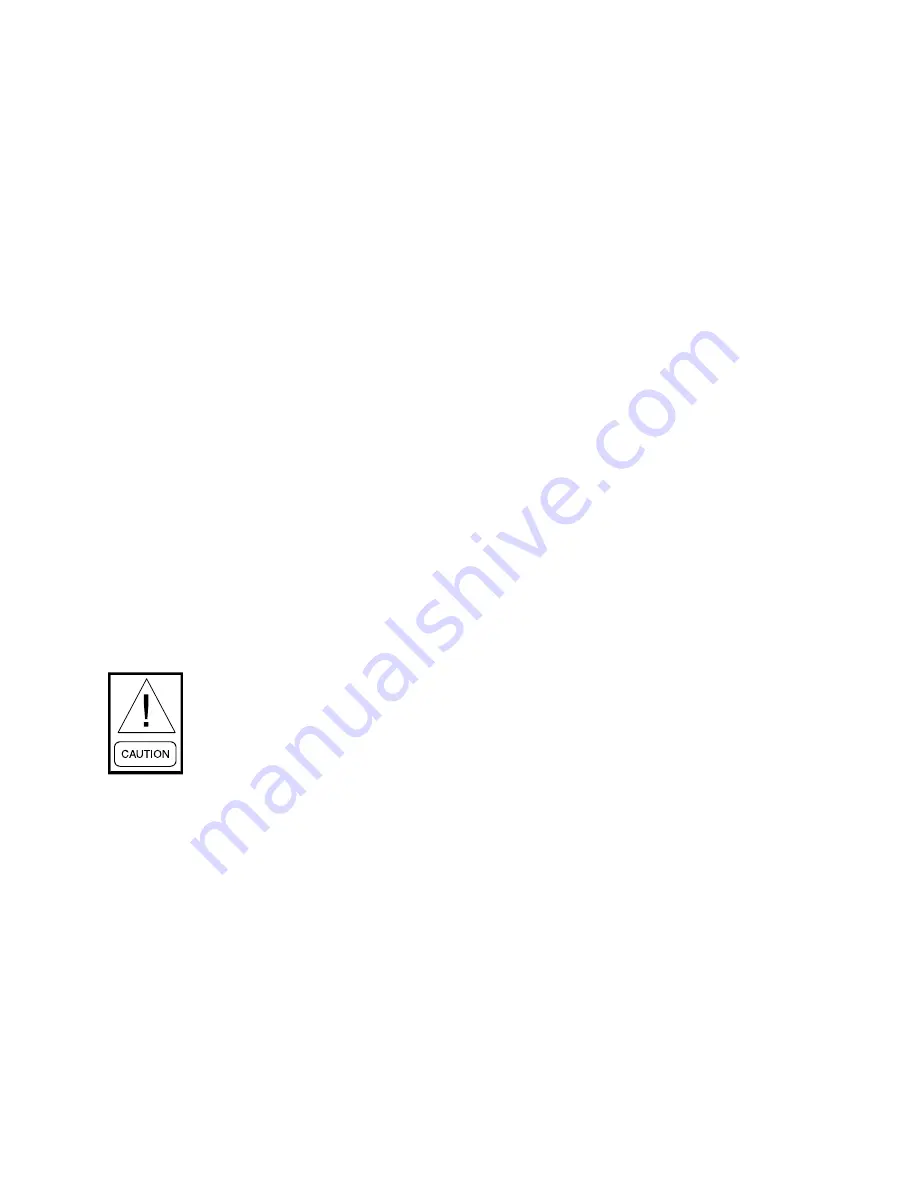
FORM 201.19-CL1 (309)
JOHNSON CONTROLS
3
Programmed Settings
Ensure the system cut-out and operational settings
are in accordance with the instructions provided in
Section 8 of the IOM and with the general chiller op-
erational requirements by pressing the
“
Program
”
key.
The chilled liquid temperature control settings need to
be set according to the unit model and required operat-
ing conditions.
Date and Time
Program the date and time by first ensuring that the
CLK jumper J18 on the microprocessor board is in the
ON position (top two pins). Then press the
“
Clock Set
Time
”
key and set the date and time.
Start/Stop Schedule
Program the daily and holiday start/stop by pressing the
“
Set Schedule/Holiday
”
key.
Setpoint and Remote Offset
Set the required leaving chilled liquid temperature
setpoint and control range. If remote temperature reset
(offset) is to be used, the maximum reset must be pro-
grammed by pressing the
“
Remote Reset Temp
”
key.
First time start-up
During the commissioning period there
should be sufficient heat load to run
the unit under stable full load opera
-
tion to enable the unit controls, and
system operation to be set up correctly
and a commissioning log taken. Be
sure that the Micro Panel is properly
programmed and the System Start-up
Check List is completed.
Interlocks
Verify that liquid is flowing through the evaporator and
that heat load is present. Ensure that any remote run in-
terlocks are in the run position and that the run schedule
requires the unit to run or is overridden.
System Switches
Place the
“
Sys 1
”
switch on the microprocessor board
to the
“
ON
”
position.
Start-up
Remove the locking device from the unit Auto/OFF
switch which prevents unauthorized starting of the unit
before commissioning. Press the
“
Status
”
key, then turn
the unit switch to the “1” position to start the unit (there
may be a few seconds delay before the first compressor
starts because of the anti-recycle timer). Be ready when
each compressor starts, to switch the unit OFF immedi-
ately if any unusual noises or other adverse conditions
develop. Use the appropriate emergency stop device if
necessary.
Oil Pressure
When a compressor starts, press the relevant
“
System
Pressures
”
key and verify that oil differential pressure
develops immediately (Discharge Pressure minus Oil
Pressure). If oil pressure does not develop, the automatic
controls will shut down the compressor. Under no cir-
cumstances should a restart attempt be made on a com-
pressor which does not develop oil pressure immediately.
Switch the unit switch to the
“
0
”
position (OFF).
Refrigerant Flow
When a compressor starts, a flow of liquid refrigerant
will be seen in the liquid line sight glass. After several
minutes operation and providing a full charge of refrig-
erant is in the system, the bubbles will disappear and be
replaced by a solid column of liquid.
Fan Rotation
As discharge pressure rises, the condenser fans oper-
ate in stages to control the pressure. Verify that the fan
operation is correct for the type of unit.
Suction Superheat
Check suction superheat at steady full compressor
load only. Measure suction temperature on the copper
line about 6" (150 mm) before the compressor suction
service valve. Measure suction pressure at the compres-
sor service valve. Superheat should be 10°F to 12°F
(5.6°C to 6.7°C).
Expansion Valve
The electronic expansion valves are factory set and
should not need adjustment.