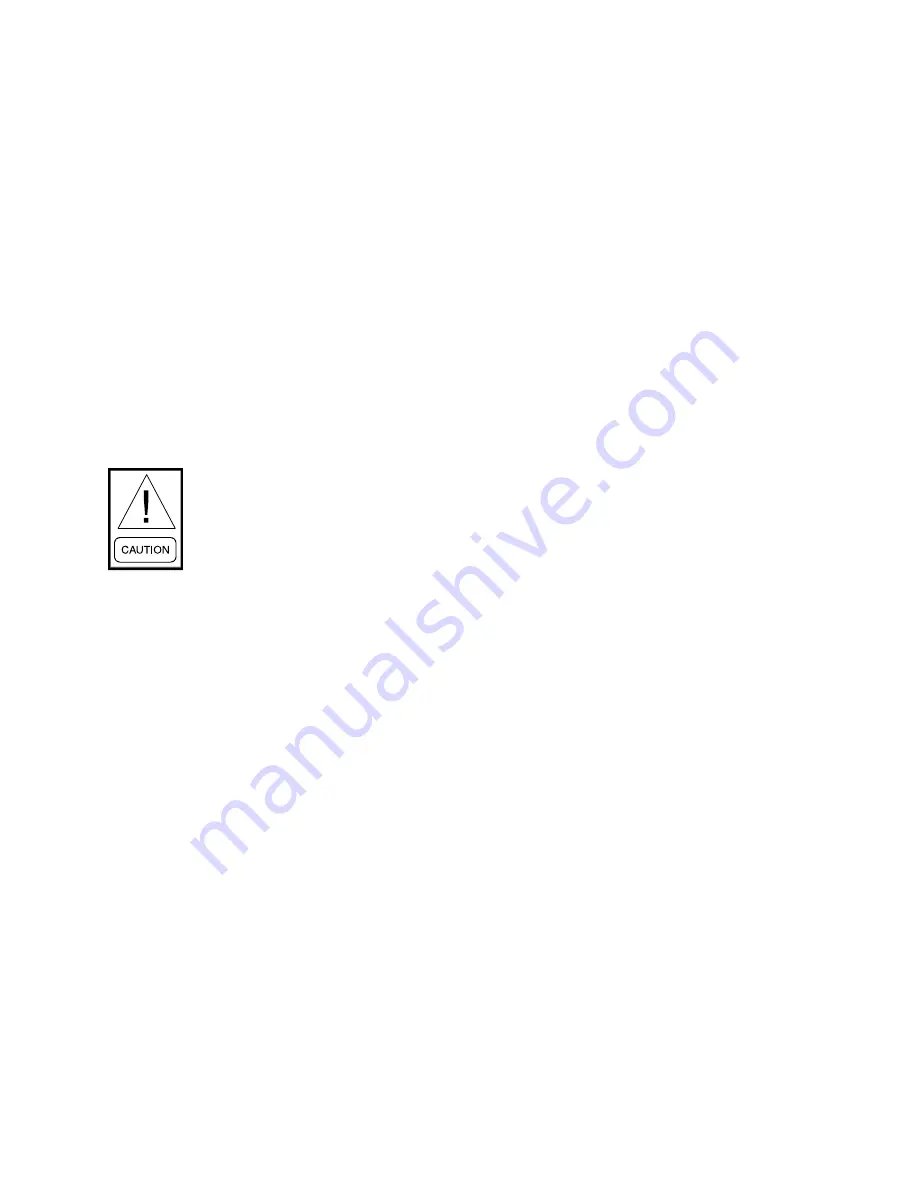
FORM 201.19-CL1 (309)
JOHNSON CONTROLS
7
1. Place the System Switches on the Microproces-
sor Board to the ON position.
2. The compressor will start and a flow of refriger
-
ant will be noted in the sight glass. After several
minutes of operation, the bubbles in the sight
glass will disappear and there will be a solid col-
umn of liquid when the TXV stabilizes. After the
water temperature stabilizes at desired operating
conditions, the sight glass should be clear.
3. Allow the compressor to run a short time, being
ready to stop it immediately if any unusual noise
or adverse conditions develop. Immediately at
start-up, the compressor will make sounds dif-
ferent from its normal high pitched sound. This
is due to the compressor coming up to speed and
lubrication changing from liquid refrigerant to
oil. This should be of no concern and lasts for
only a short time.
4. Check the system operating parameters. Do this
by selecting various displays such as pressures
and temperatures. Compare these to test gauge
readings.
CHECkIng SUBCOOLIng AnD SUPERHEAt
The subcooling should always be checked when charg-
ing the system with refrigerant and/or before setting
the superheat.
When the refrigerant charge is correct, there will be no
bubbles in the liquid sight glass with the system operat-
ing under full load conditions, and there will be 12 - 15°F
(6 - 8°C) subcooled liquid leaving the condenser.
An overcharged system should be guarded against.
Evidences of overcharge are as follows:
a. If a system is overcharged, the discharge pressure
will be higher than normal. (Normal discharge/
condensing pressure can be found in the refriger-
ant temperature/pressure chart; use entering air
tempe30°F (17°C) for normal condens-
ing temperature.
b. The temperature of the liquid refrigerant out of
the condenser should be not be more than 15°F
(8°C) less than the condensing temperature (The
temperature corresponding to the condensing
pressure from the refrigerant temperature/pres-
sure chart).
8. Set the Time and Date.
9. Program the Daily Schedule start and stop
times.
10. Check the Factory Service Mode programming
values, assure they are correct, and record the
values below:
Refrigerant Type = ____________________________
R407C Chiller Type = ____________________________
Unit Type = ___________________________________
Heat Recovery = _______________________________
Sys #1 100% FLA = _________________________Amps
Sys #2 100% FLA = _________________________Amps
Sys #1 Motor Protector Input = ________________ Volts
Sys #2 Motor Protector Input = ________________ Volts
Typically, these values should not be
changed. Incorrect programming
may cause catastrophic chiller fail-
ure.
11. Check the Motor Protector Dip Switch program-
ming. The switches should correctly set at the
factory. The switches may be checked visibly
and the total ON switches added using binary
addition to determine the setting or by reading
the display on the motor protector. See Section
8 for programming information. Record the
values below:
Sys #1 Wires thru each hole of the C.T. = ____________
Sys #1 MP Setting = ____________
Sys #2 Wires thru each hole of the C.T. = ____________
Sys #2 MP Setting = ____________
InItIAL StARt-UP
After the control panel has been programmed and the
compressor heater has been on for 24 hours prior to
start-up, the chiller may be placed into operation.