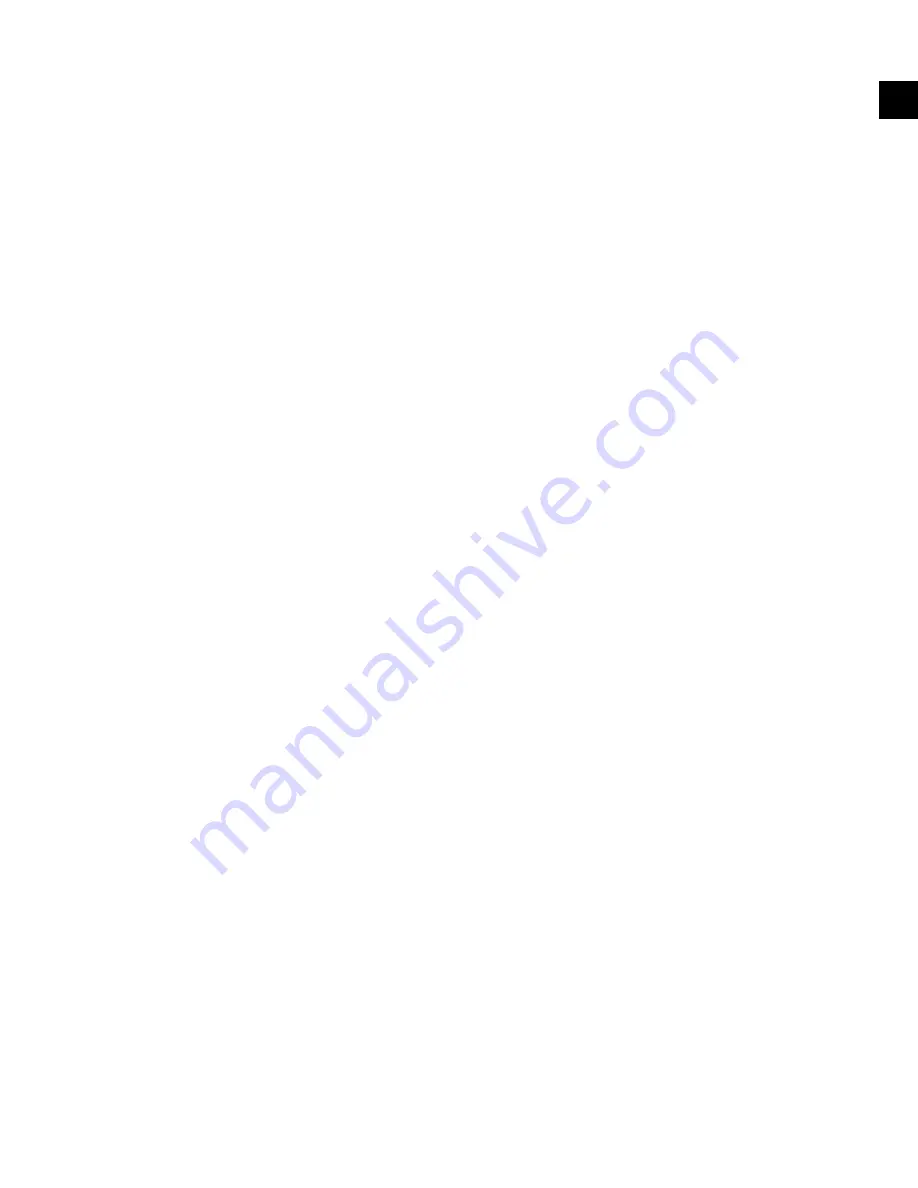
JOHNSON CONTROLS
9
FORM 160.77-O1
ISSUE DATE: 10/22/2020
SECTION 1 - SYSTEM FUNDAMENTALS
Compressors
Two centrifugal compressors are provided, operating
partially in parallel and discharging to a common con-
denser on the chiller. Check valves are supplied on the
discharge of the economizer compressor to control re-
frigerant flow during single compressor operation.
Each of the YKEP’s two compressors is a single-stage
centrifugal type powered by an open-drive electric mo-
tor. The casing is fully accessible with vertical circular
joints and fabricated of close-grain cast iron. The com-
plete operating assembly is removable from the com-
pressor and scroll housing.
The rotor assembly consists of a heat-treated alloy steel
drive shaft and impeller shaft with a high strength, cast
aluminum alloy, fully shrouded impeller. The impeller
is designed for balanced thrust and is dynamically bal-
anced and overspeed tested for smooth, vibration free
operation.
The insert-type journal and thrust bearings are fabri-
cated of aluminum alloy and are precision bored and
axially grooved. The specially engineered, single heli-
cal gears with crowned teeth are designed so that more
than one tooth is in contact at all times to provide even
distribution of compressor load and quiet operation.
Gears are integrally assembled in the compressor rotor
support and are film lubricated. Each gear is individu-
ally mounted in its own journal and thrust bearings to
isolate it from impeller and motor forces
Motors
YORK YKEP centrifugal chillers utilize air-cooled
motors. This means that refrigerant never comes in
contact with the motor.
Starters
Medium Voltage VSD
A variable speed drive is factory-packaged and con-
figured for easy remote mounting. It is designed to
vary the compressor motor speed by controlling the
frequency and voltage of the electrical power to the
motor. The adaptive capacity control logic automati-
cally adjusts motor speed and compressor pre-rotation
vane position independently for maximum part load ef-
ficiency by analyzing information fed to it by sensors
located throughout the chiller. Operational information
for the VSD can be found in
MV VSD (2300v - 6600v)
- Operation (Form 160.00-O6)
, and
MV VSD (10,000v
- 13,800v) - Operation (Form 160.00-O8)
.
Medium Voltage Solid-State Starter
A Solid-State Starter is a unit mounted reduced volt-
age in-line bypass starter that controls and maintains
a constant current flow to the motor during startup.
Power and control wiring between the starter and
the chiller are factory-installed. Available for 4160V
3-phase 60Hz, 2300V 3-phase 60 Hz or 3300V
3-phase 50 Hz applications, the starter enclosure is
NEMA-1, with a hinged access door with lock and
key. Electrical lugs for incoming power wiring are not
provided. Operational information for the solid state
starter can be found in
Unit Mounted Medium Volt-
age Solid State Starter (2300v - 4160v) - Operation
(Form 160.00-O7)
.
Flash Economizer (Intercooler)
The Flash Economizer is a single-stage type, con-
sisting of a horizontal pressure vessel with internally
mounted baffles and liquid spray pipe, an externally
mounted level transmitter located with a liquid level
pipe assembly, and an external control valve mounted
in the liquid outlet to the evaporator. Refrigerant from
the condenser, after expanding through the condenser
subcooler level control valve, enters through the inter-
nal spray pipe, where flash gas is removed and chan-
neled through baffles, out the top and on to the econo-
mizer compressor suction. The remaining liquid feeds
out of the economizer through a liquid level control
valve to the evaporator.
Heat Exchangers
Shells
Evaporator and condenser shells are fabricated from
rolled carbon steel plates with fusion welded seams or
carbon steel pipe. Carbon steel tube sheets, drilled and
reamed to accommodate the tubes, are welded to the
end of each shell. Intermediate tube supports are fab-
ricated from carbon steel plates, drilled and reamed to
eliminate sharp edges, and spaced no more than four
feet apart. The refrigerant side of each shell is designed,
tested, and stamped in accordance with ASME Boiler
and Pressure Vessel Code, Section VIII – Division I, or
other pressure vessel codes, as appropriate.
1