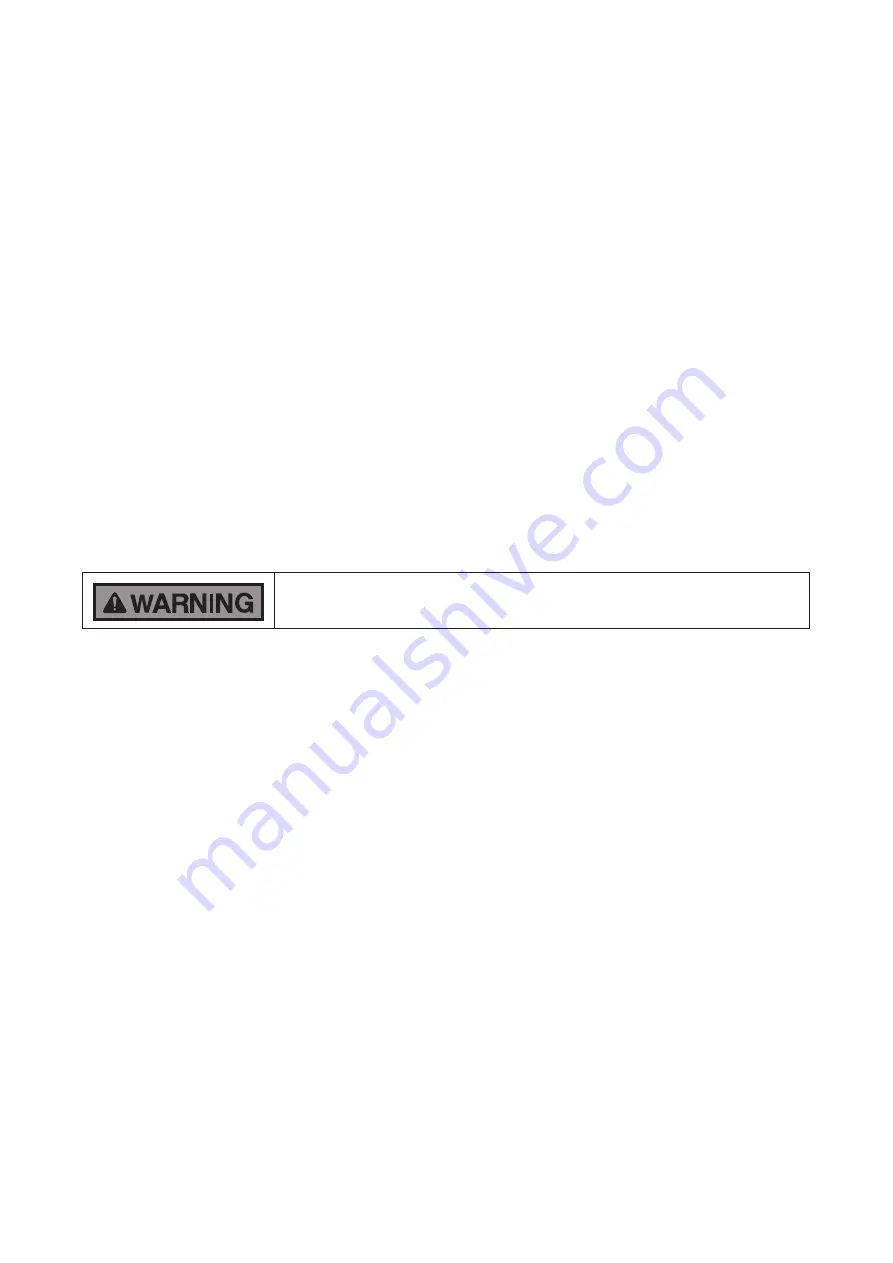
P5417009-rev.6
3
●
Do not position the drain pipe for the indoor unit near any sanitary sewers where corrosive gases
may be present. If you do, toxic gases can seep into breathable air spaces and can cause respiratory
injuries. If the drainpipe is installed incorrectly, water leakage and damage to the ceiling, floor,
furniture, or other possessions may result. If condensate piping becomes clogged, moisture can back
up and can drip from the indoor unit. Do not install the indoor unit where such dripping can cause
moisture damage or uneven locations: Use a raised concrete pad or concrete blocks to provide a
solid, level foundation for the unit to prevent water damage and abnormal vibration.
●
Before performing any brazing work, be sure that there are no flammable materials or open flames
nearby.
●
Perform a test run to ensure normal operation. Safety guards, shields, barriers, covers, and protective
devices must be in place while the compressor/unit is operating. During the test run, keep fingers and
clothing away from any moving parts.
●
Clean up the site when finished, remembering to check that no tools, metal scraps, or bits of wiring
have been left inside the unit being installed.
●
During transportation, do not allow the backrest of the forklift make contact with the unit, otherwise,
it may cause damage to the heat exchanger and also may cause injury when stopped or started
suddenly.
●
Remove gas inside the closing pipe when the brazing work is performed. If the brazing filler metal is
melted with remaining gas inside, the pipes will be blown off and it may cause injury.
●
Be sure to use nitrogen gas for an airtight test. If other gases such as oxygen gas, acetylene gas or
fluorocarbon gas are accidentally used, it may cause explosion or gas intoxication.
After installation work for the system has been completed, explain the “Safety Precautions,” the proper use
and maintenance of the unit to the customer according to the information in all manuals that came with the
system. All manuals and warranty information must be given to the user or left near the Indoor Unit.
Refrigerant Precautions
To reduce the risk of serious injury or death, the following refrigerant
precautions must be followed.
●
As originally manufactured, this unit contains refrigerant installed by Johnson Controls. Johnson
Controls uses only refrigerants that have been approved for use in the unit’s intended home country
or market. Johnson Controls distributors similarly are only authorized to provide refrigerants that
have been approved for use in the countries or markets they serve. The refrigerant used in this unit
is identified on the unit’s faceplate and/or in the associated manuals. Any additions of refrigerant into
this unit must comply with the country’s requirements with regard to refrigerant use and should be
obtained from Johnson Controls distributors. Use of any non-approved refrigerant substitutes will void
the warranty and will increase the potential risk of equipment damage, property damage, personal
injury, or death.
●
Take measures to ensure that the refrigerant limitations in ASHRAE Standard 15 (Canada: B52), or
other local codes, are followed. If refrigerant gas has leaked during the installation work, ventilate the
room immediately.
●
Check the design pressure for this product is 601 psi (4.15MPa). The pressure of the refrigerant
R410A is 1.4 times higher than that of the refrigerant R22. Therefore, the refrigerant piping for
R410A shall be thicker than that for R22. Make sure to use the specified refrigerant piping. If not, the
refrigerant piping may rupture due to an excessive refrigerant pressure. Besides, pay attention to
the piping thickness when using copper refrigerant piping. The thickness of copper refrigerant piping
differs depending on its material.
●
The refrigerant R410A is adopted. The refrigerant oil tends to be affected by foreign matters such as
moisture, oxide film, or other non-condensables. Perform the installation work with care to prevent
moisture, dust, or different refrigerant from entering the refrigerant cycle. Foreign matter can be
introduced into the cycle from such parts as expansion valve and the operation may be unavailable.
●
To avoid the possibility of different refrigerant or refrigerant oil being introduced into the cycle, the
sizes of the charging connections have been changed from R407C type and R22 type. It is necessary
to prepare the following tools listed in Section 3 before performing the installation work.
●
Use refrigerant pipes and joints which are approved for use with R410A.
●
A compressor/unit comprises a pressurized system. Never loosen threaded joints while the system is
under pressure and never open pressurized system parts.