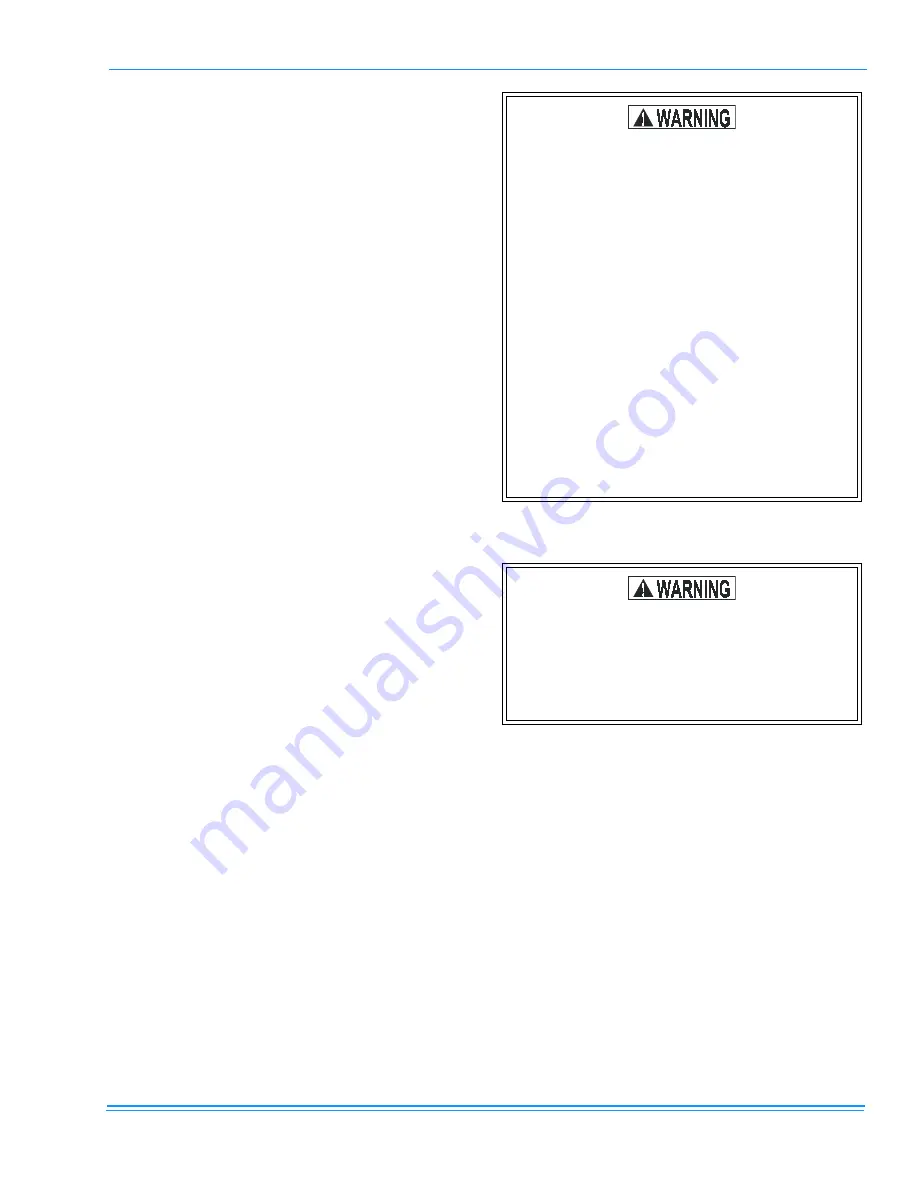
035-17443-000 Rev. A (800)
Unitary Products Group
3
GENERAL INFORMATION
DESCRIPTION
This Category I furnace is designed for installation in a resi-
dential or commercial application. A Category 1 furnace has
a fan assisted combustion system equipped with an integral
mechanical means to draw products of combustion through
the combustion chamber and heat exchanger. It may be
installed in a basement, garage, equipment room, alcove,
attic or any other indoor location where all required clear-
ances to combustibles and other restrictions are met. It is
designed for natural gas-fired operation, but may be con-
verted to propane (LP) using the INP0349 kit.
High altitude and propane (LP) changes or conversions
required in order for the appliance to satisfactorily meet the
application must be made by an authorized distributor: in
Canada, a certified conversion station or other qualified
agency, using factory specified and/or approved parts.
This furnace may be used only as a Category 1 unit.
The furnace must be installed so that all electrical compo-
nents are protected from water.
INSPECTION
As soon as a unit is received, it should be inspected for possi-
ble damage during transit. If the damage is evident, the
extent of the damage should be noted on the carrier’s freight
bill.
A separate request for inspection by the carrier's agent
should be made in writing. Also, before installation, the unit
should be checked for belt, screws or bolts which may have
loosened in transit.
NOTES, CAUTIONS & WARNINGS
The installer should pay particular attention to the words:
NOTE, CAUTION and WARNING. NOTES are intended to
clarify or make the installation easier. CAUTIONS are given
to prevent equipment damage. WARNINGS are given to alert
the installer that personal injury and/or equipment or property
damage may occur if installation procedures are not handled
properly.
LIMITATIONS AND LOCATION
This furnace should be installed in accordance with all
national / local building / safety codes and requirements, or in
the absence of local codes, with the National Fuel Gas Code,
ANSI Z223.1 - (latest edition) or, in Canada, CAN/CGA
B149.1 or.2 - (latest edition), and other applicable codes.
Use only the type of gas approved for this furnace; refer to
the furnace rating plate.
For installations above 2,000 feet, reduce input 4% for each
1,000 feet above sea level. Canadian installations must be
derated 10% for elevations from 2,000 ft. to 4,500 ft. Use
1PS0301 kit to properly derate this furnace.
The furnace shall not be connected to a chimney flue serving
a separate appliance designed to burn solid fuel.
Check the rating plate and power supply to be sure that elec-
trical characteristics match. All models are factory wired for
208 / 230 VAC, 1 phase, 60 Hertz power supply.
A furnace installed in a residential garage must be located so
that all burners and burner ignition devices are located no
less than 18" above the garage floor, and located or pro-
tected to prevent damage by vehicles.
Each furnace in this series is a Category I furnace,
suitable for common venting with other gas-fired
appliances as allowed by the National Fuel Gas
Code, NFPA 54/ANSI Z223.1-latest edition.
This appliance is not to be used for temporary
heating of buildings or structures under construc-
tion.
Do not install this furnace in a corrosive or contam-
inated atmosphere.
Do not install this furnace in a mobile home or rec-
reational vehicle.
Furnaces shall not be installed directly on carpet-
ing, tile or other combustible material other than
wood flooring.
Continuous return air temperature must not be
below 55 °F (13 °C).
Only use natural gas in furnaces designed for nat-
ural gas. Only use propane (LP) gas for furnaces
that have been properly converted to use propane
(LP) gas. Do not use this furnace with butane.
Using wrong gas could create a hazard, resulting
in damage, injury or death.