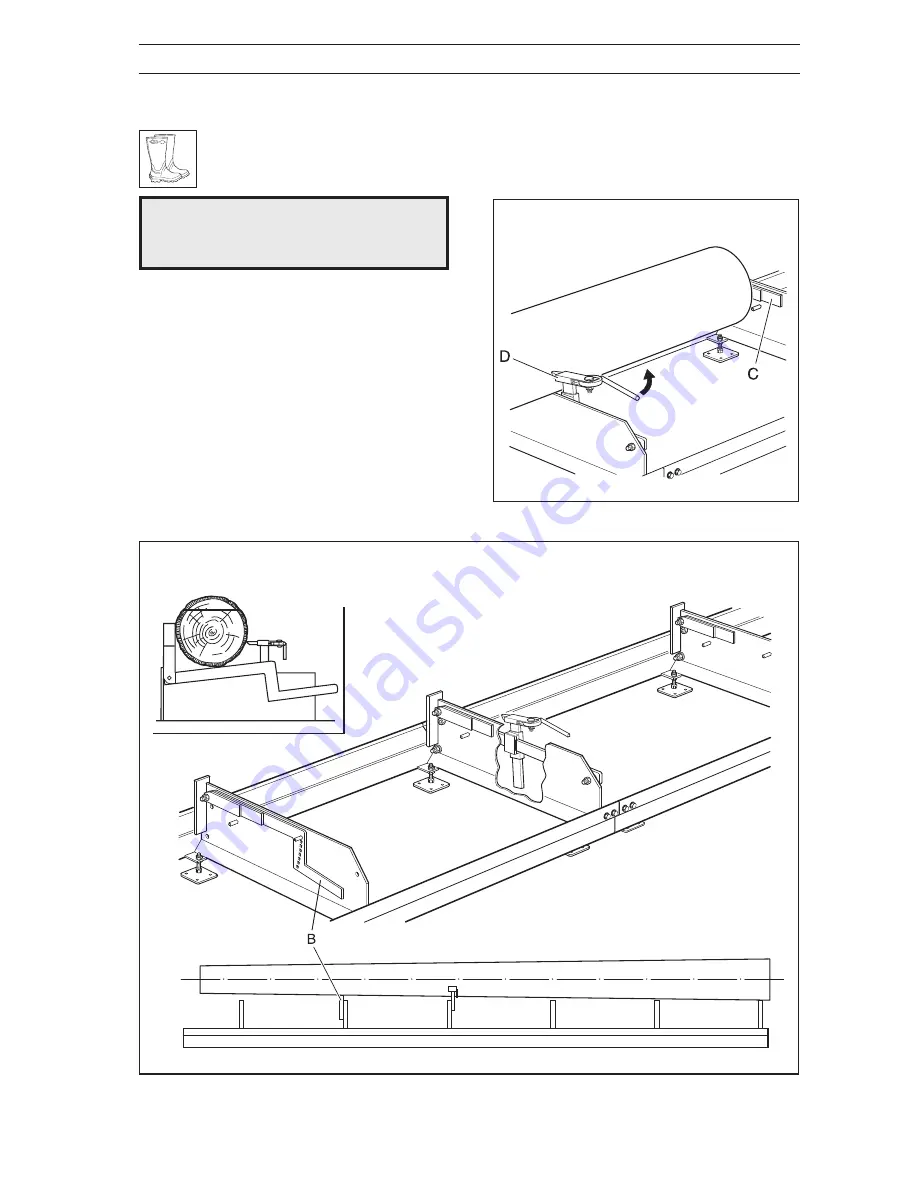
English –
25
Securing the Log
WARNING!
Exercise care during all log hand-
ling. Heavy lift! Wear boots or
shoes fitted with steel toecaps.
1.
Fold up the stops (C) on the left-hand side of the
rails.
2.
Roll the log up against either the long or the short
log support, depending on the timber dimensions.
• than 300 mm to the end of the rails
• than 500 mm to the start of the rails
This means that when using two rail sections, the
maximum log length is 5200 mm.
3.
Raise the log using the log lifter (B) so that the
log’s core is horizontal.
4.
Lock the log in position with the log lock (D).
USE
!
FIG. 43
FIG. 44
Summary of Contents for SM 2055 E
Page 35: ......
Page 36: ...2003W50 z x 6 108 89 11 26 ...