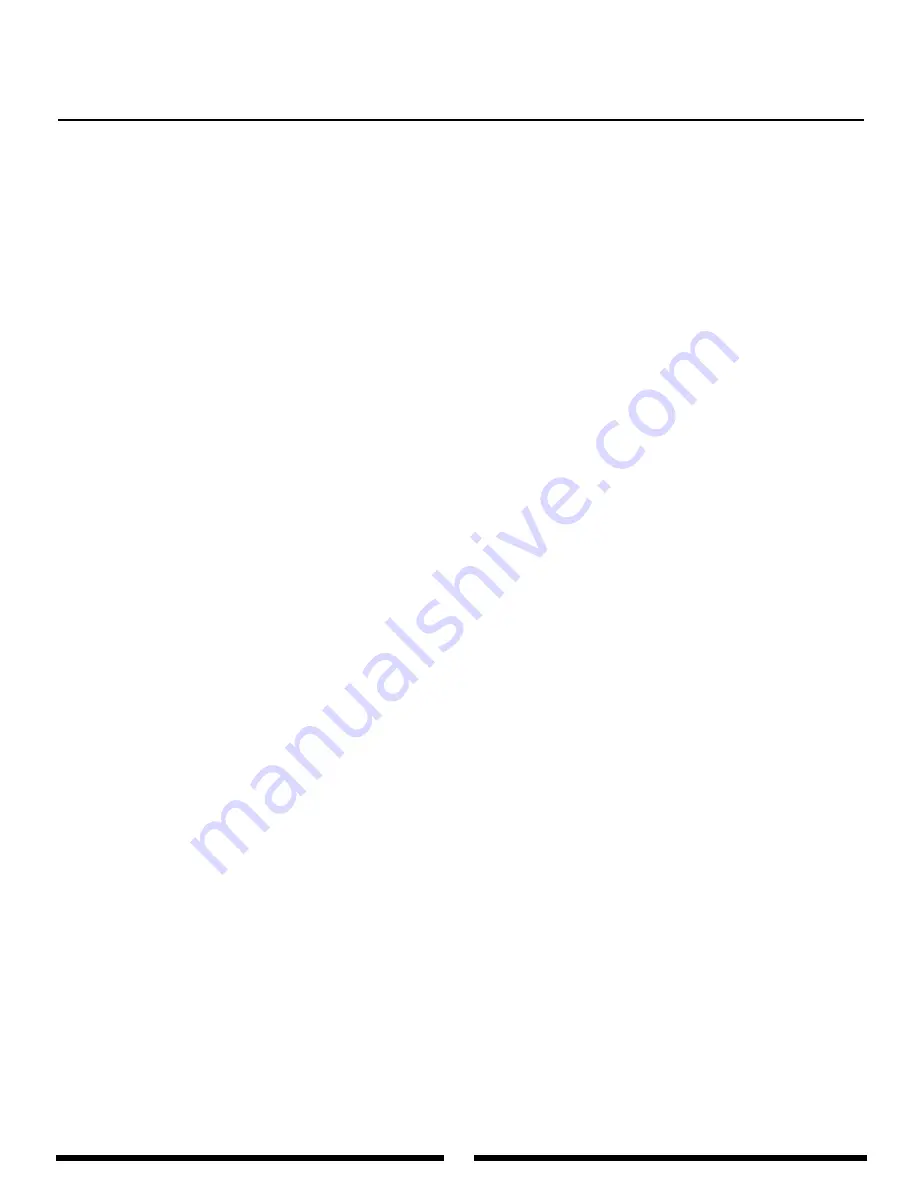
83
VIGOR
™
CS MANUAL PARTS LISTINGS
Swashplate/CCPM Control System
Part #
Description
Quantity
Comments/ Additional Contents
JRP970001 Joint Balls w/8 mm screws
10
JRP970002 Joint Balls w/10 mm screws
10
JRP970004 Universal Links
10
JRP970018 Mixing Lever Spacer
2
JRP970020 Main Frame Standoff, 32 mm
2
JRP970053 Control Ball Spacer
2
JRP970078 Control Ball Spacer, 2.75 mm
2
JRP970082 Washer, 3 x 4.5 x 4 mm
2
JRP970104 Servo Mounting Plates
8
JRP970201 Control Ball, 4 mm
2
JRP970206 CCPM T Lever Spacer
2
JRP970209 CCPM A Arm Collar
2
JRP970211 Shaft Washer, CCPM
2
JRP980002 Set Screws,3 x 4 mm
10
JRP980004 Set Screws,4 x 4 mm
10
JRP980013 Socket Head Bolts,3 x 8 mm
10
JRP980016 Socket Head Bolts,3 x 15 mm
10
JRP980020 Socket Head Bolts,3 x 28 mm
10
JRP980022 Socket Head Bolts,3 x 40 mm
10
JRP980027 Self Tapping Screws,2 x 8 mm
10
JRP980035 Plate Washer, 2.6 mm
10
JRP980037 Hex Nuts, 2 mm
10
JRP980039 Nylon Lock Nuts, 3 mm
10
JRP980040 Nylon Lock Nuts, 4 mm
10
JRP980046 Control Rod, 2.3 x 60 mm
2
JRP980052 Control Rod, 2.3 x 15 mm
2
JRP980056 Control Rod, 2.3 x 85 mm
2
JRP980057 Control Rod, 2.3 x 95 mm
2
JRP980067 Set Screws, 3 x 3 mm
10
JRP980071 Plate Washers, 4 mm
10
JRP980102 Socket Head Bolts, 4 x 10 mm
10
JRP980105 Control Rod, 2.3 x 80 mm
2
JRP980148 Self Tapping Screws,2.6 x 15 mm
10
JRP991003 CCPM Control Arm Block w/bb
1
JRP994018 CCPM Elevator Control Arm
1
JRP994019 Control Ball, 20 mm
2
JRP994020 CCPM Control Arm Shaft
1
JRP994021 Special Universal Link (White)
10
JRP996038 CCPM Swashplate Assembly
1
Complete with control balls and screws
JRP996040 CCPM T Lever Assm. w/BB
1
JRP996041 CCPM Top Servo Mounting Post
1
JRP996042 CCPM A Arm Assembly
1
JRP996043 CCPM Elevator Arm Assembly
1
JRP996039 Aluminum Washout Base
1
Summary of Contents for Vigor CS
Page 64: ...64 E A C D G F DECAL PLACEMENT ...
Page 65: ...65 B 3 2 5 1 DECAL PLACEMENT ...