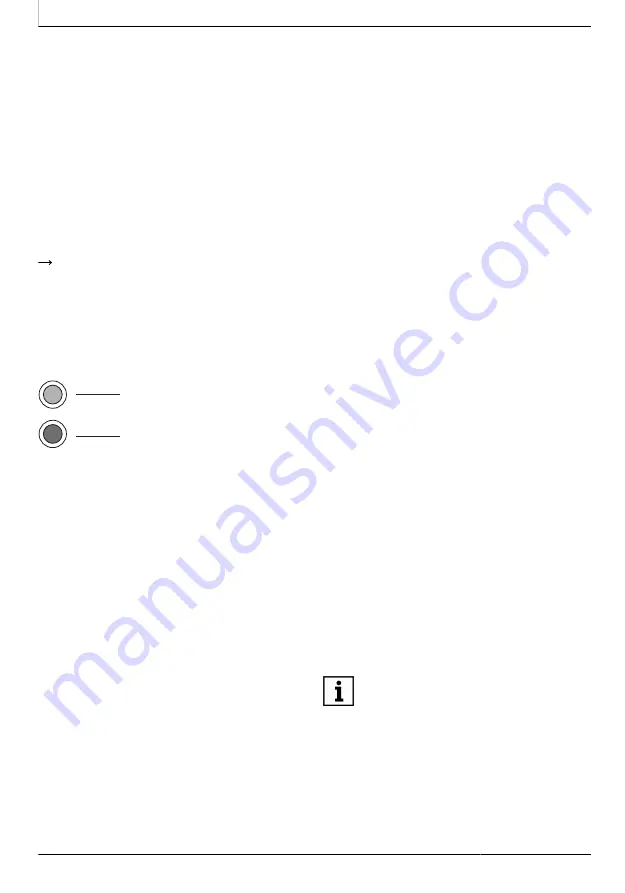
Installation
3.5
Commissioning
Prior to initial commissioning (or to com-
missioning after maintenance work) fill the
installed device with water and vent:
1.
Open the upstream shut-off valve to
fill the device with water. The device is
now under mains pressure.
2. Attention:
Immediately plug the power
supply unit in. This automatically carries
out backwashing and the trapped air
can escape. This prevents damage to
the installation due to pressure surges.
After backwashing, the device is vented
and ready for operation.
4
Operation
4.1
Warning lights
1
2
Fig. 6:
Warning lights
1
Operation (green warning light)
The device is now ready for operation.
2
Fault (red warning light)
A fault exists (see chapter 6).
4.2
Setting the downstream pres-
sure
To compensate for pressure fluctuations
and to protect the downstream installation,
the downstream pressure can be regulated
via the pressure reducer. The factory pre-
set downstream pressure of 4 bar can be
changed to a value between 1.5 bar and
6 bar depending on the upstream pressure:
1.
Remove the pressure reducer cover
(only for device of connection range
¾" - 1¼").
2.
Undo the countersunk screw on the
handwheel of the pressure reducer.
3.
Turn the handwheel clockwise
(= pressure increase), or turn counter-
clockwise (= pressure reduction).
4.
Open a drawing point behind the device
for a short time. This results in a pres-
sure relief and the set downstream
pressure can be read off from the
downstream pressure gauge.
5.
When the desired downstream pressure
has been reached, retighten the coun-
tersunk screw on the pressure reducer
handwheel to prevent automatic adjust-
ment of the downstream pressure.
6.
Attach the pressure reducer cover
again (only for device of connection
range ¾" - 1¼").
4.3
Cleaning of the sieve insert
(backwashing)
A regular cleaning process is necessary to
remove the residues from the sieve fabric
of the device. This process is called
back-
washing
.
Suction pipes are provided for backwash-
ing, which rotate around the sieve fabric
of the fine filter. The backwashing valve
opens on the bottom side of the device. By
reversing the water flow from inside to out-
side, deposits on the sieve fabric are car-
ried away and rinsed out with the back-
wash water. The suction pipes also clean
the inside of the transparent filter bowl with
wiper lips during their movement.
The degree of contamination and cleaning
process can be observed from the outside.
INFO_NO_HEADER
The device is backwashed with
filtered water. The filtered water
supply of the domestic installation
remains intact during the backwash-
ing process. No dirty water can reach
the pure water side during the back-
washing.
1701431 • 2022/01
JUDO JUKOMAT-LF-AT
13