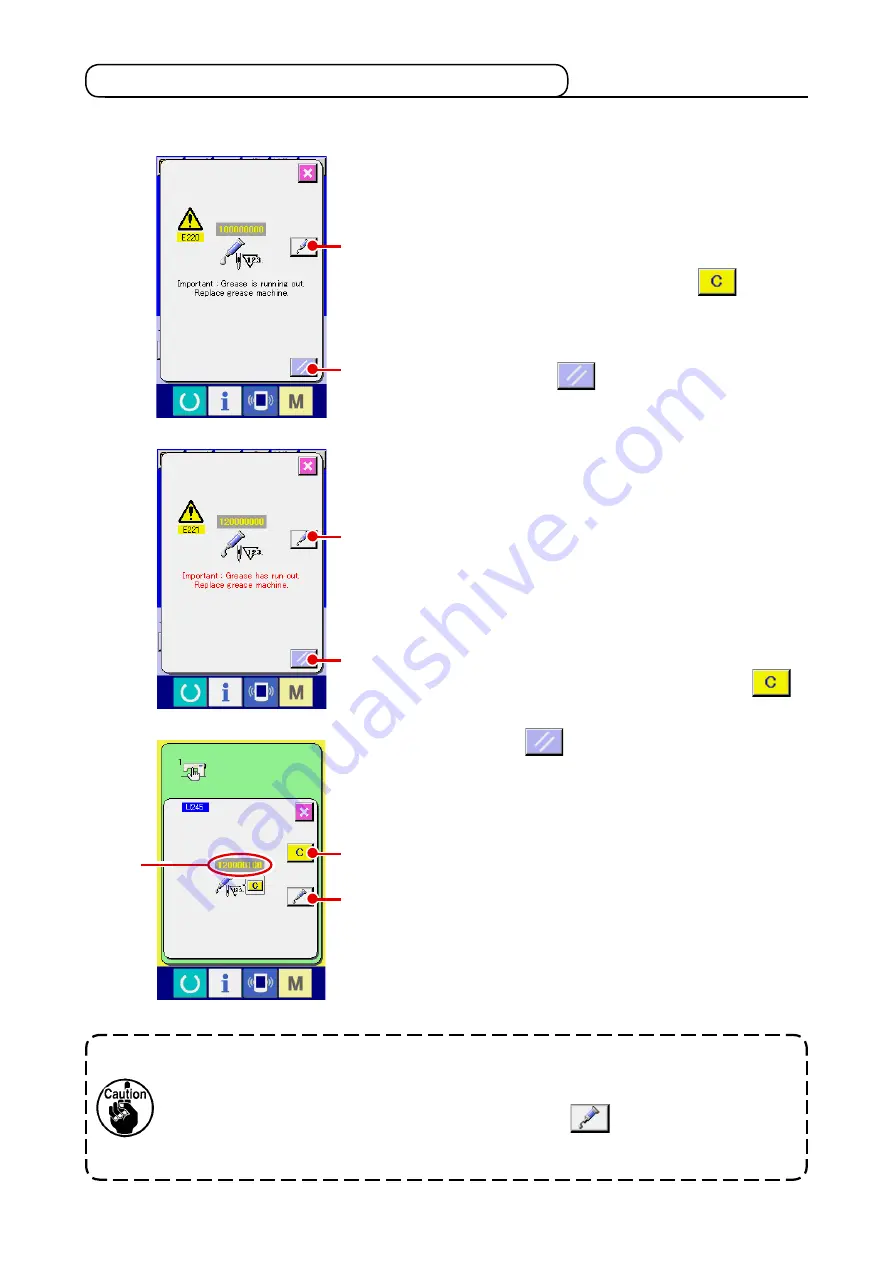
– 101 –
1-13. replenishing the designated places with grease
C
B
C
B
A
C
D
* Perform grease supplement when the errors below are displayed or once a year (either one
which is earlier).
When the sewng machne has been used for a certan
number of sttches, error "E220 Grease-up warnng" s
dsplayed. Ths dsplay nforms the operator of the tme of
replenshng the desgnated places wth grease. Be sure to
replensh the places wth the grease below. Then call the
memory swtch U245, press CLEAR button
A
and
set NUMBER OF STITCHES
D
to "0".
Even after the dsplay of the error "E220 Grease-up warn-
ng", when RESET key
B
s pressed, the error s re-
leased, and the sewng machne can be contnuously used.
Afterwards, however, error code "E220 Grease-up warnng"
s dsplayed every tme the power s re-turnng ON.
In addton, when the sewng machne s used further for a
certan perod of tme wthout replenshng the places wth
grease after the dsplay of error No. E220, error "E221
Grease-up error" s dsplayed and the sewng machne fals
to operate snce the error cannot be released even when
the RESET key s pressed.
When error "E221 Grease-up error" s dsplayed, be sure to
replensh the desgnated places below wth grease. Then
call the memory swtch U245, press CLEAR button
A
and set NUMBER OF STITCHES
D
to "0".
When RESET key
B
s pressed wthout replensh-
ng the desgnated places wth grease, error code "E221
Grease-up warnng" s dsplayed every tme the power s
re-turnng ON afterwards and the sewng machne fals to
operate. So, be careful.
1. Error code E220 or E221 is displayed again unless NuMBEr oF StItcHES
D
is
changed to "0" after replenishing the designated places with grease. When E221 is
displayed, the sewing machine fails to operate. So, be careful.
2. When GrEaSE aPPLYING PoSItIoN DISPLaY button
C
is pressed in each
screen, the grease applying position can be confirmed in the panel display. Be sure,
however, to perform the grease applying after turning oFF the power.