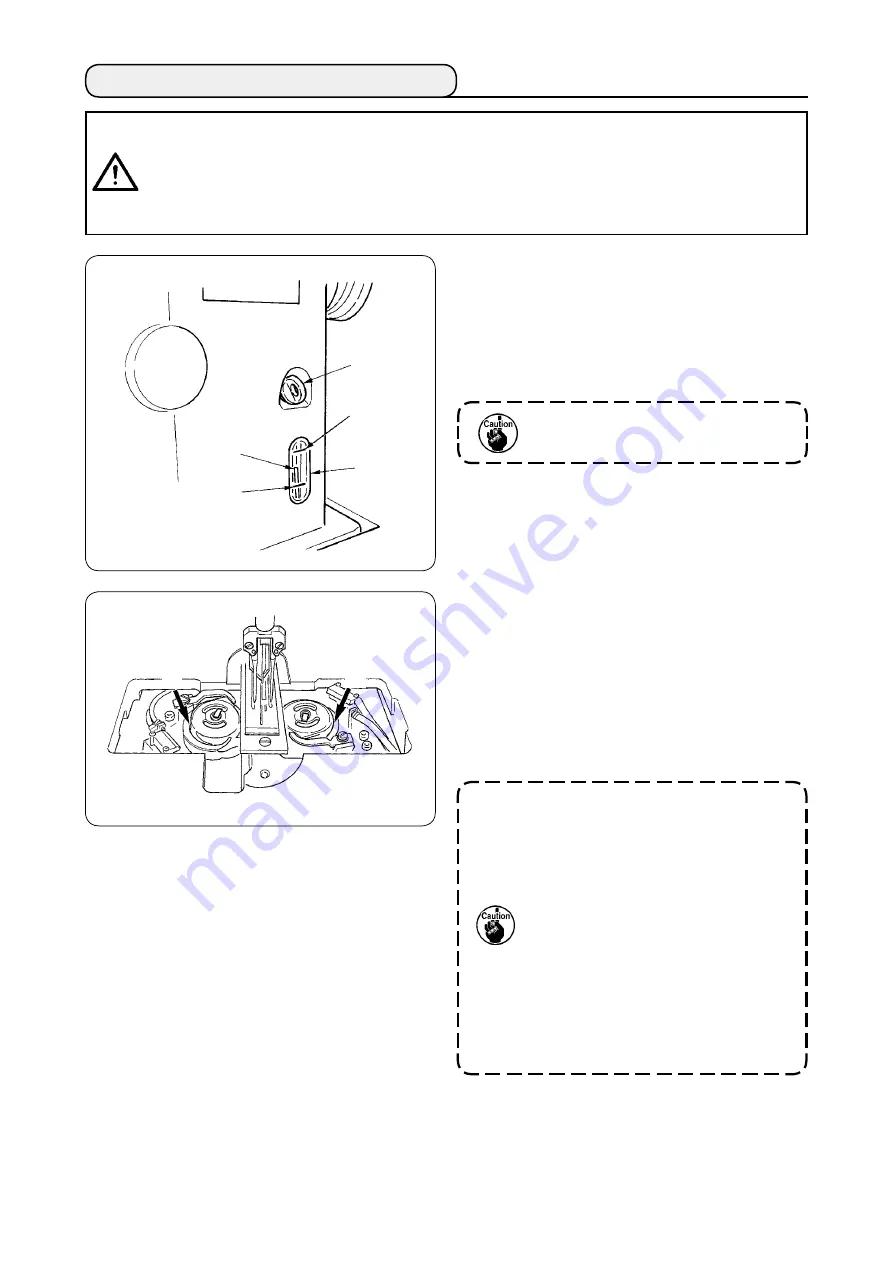
− 0 −
12. LUBRICATING THE OIL TANK
3
2
1
Fill the oil tank with the oil for hook lubrication
before operating the sewing machine.
1
Remove oil cap
1
and fill the oil tank
with JUKI MACHINE OIL No. (Part No. :
MDFRX600C0) using the oiler supplied with
the machine as accessories.
• At the time of initial filling, fill the oil
tank with oil of 200cc as the standard
and confirm that the oil amount
indicating rod is working.
• When operating a newly installed
machine or a machine which has not
been used for a relatively long period
of time, make the machine run at 2,000
sti/min or less for the purpose of
break-in. In addition, use the machine
after applying oil to races
A
of the
right/left hooks.
• For the oil for hook, purchase JUKI
MACHINE OIL No. 1 (Part No. :
MDFRX1600C0).
• Be sure to fill the oil tank with clean
oil.
Upper
engraved
marker line
A
A
2
Fill the oil tank with the oil until the top end of
oil amount indicating rod
3
comes between
the upper engraved marker line and the lower
engraved marker line of oil amount indicating
window
2
.
When oil amount is excessively large, oil
leaks from the air hole or adequate lubrication
cannot be performed. So, be careful.
3
When operating the sewing machine and
the top of oil amount indicating rod
3
has
lowered up to oil amount indicating window
2
,
start lubricating.
To prevent entering of dust, be sure to
attach the cap for use.
CAUTION
:
1. To prevent accidents caused by abrupt start of the sewing machine, do not connect the power
plug until lubrication has been completed.
2. To prevent inflammation or rash, immediately wash the part when oil has stuck to your eyes or
body.
3. If oil has been swallowed, diarrhea or vomiting may occur. Put oil to the place where children
cannot reach.
Lower
engraved
marker line