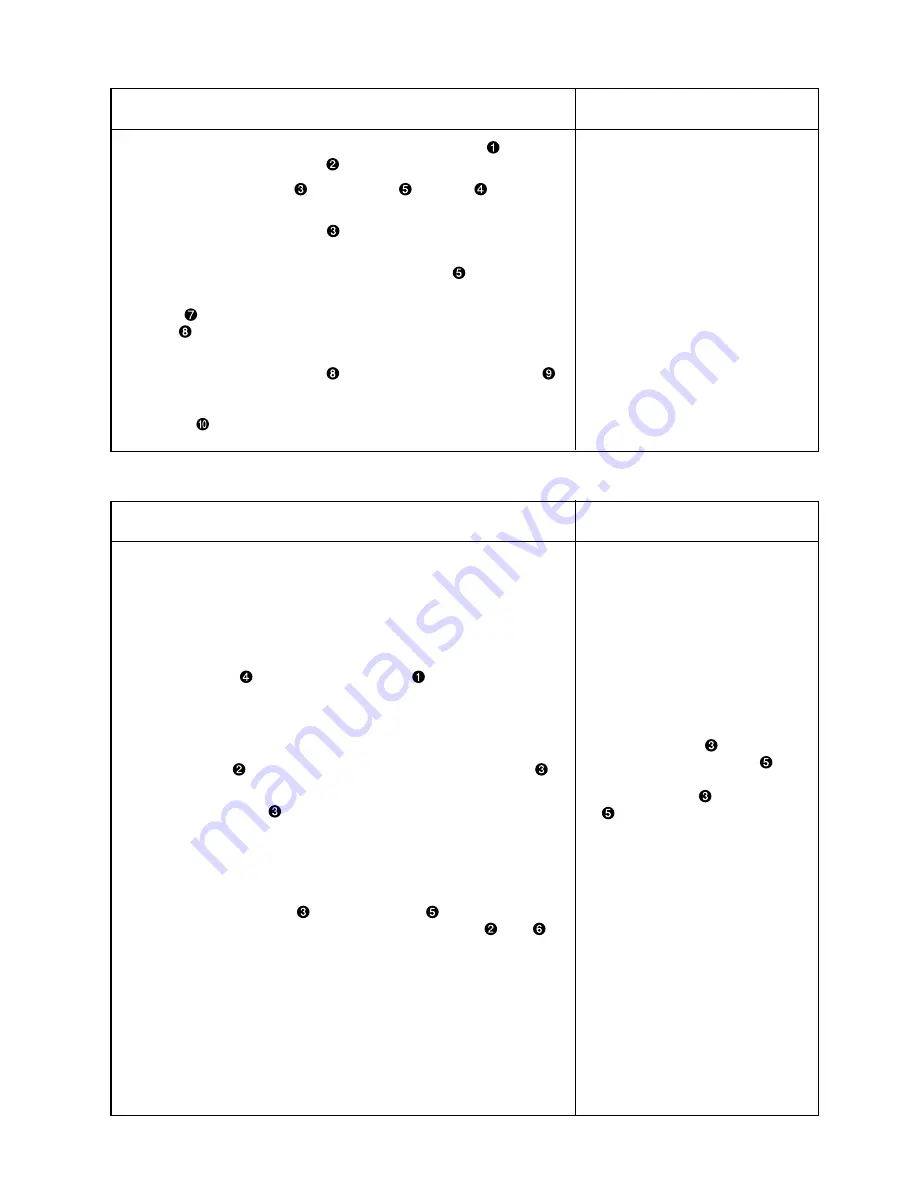
– 21 –
1. With the machine in stop mode, remove six setscrews
of the top
cover, and take off top cover
.
2. Apply L-shaped wrench
to socket bolt
of clamp
, and loosen
the socket bolt.
3. Push down L-shaped wrench
to increase the lift of the work clamp
hoot, or pull it up to decrease the lift.
4. After the adjustment, securely tighten socket bolt
.
5. If the right and left work clamp feet are not levelled, loosen fixing
screw
and adjust the position of the work clamp foot lever support
plate
to level them.
(Caution) At this time, be careful not to cause work clamp foot
lever support plate
to interfere with feed bracket
.
If the work clamp foot levers support plate interferes with
the wiper, readjust the height of the wiper using setscrew
in the wiper installing base.
Adjustment Procedures
Results of Improper Adjustment
Adjustment Procedures
Results of Improper Adjustment
1. Start the test mode CP-6.
2. Tread on the pedal to perform origin retrieval for the thread trimmer
cam.
(Confirm that the origin is in the correct position. Then, proceed to
the procedures shown below. Refer to “(12) Thread trimmer and
presser foot origin sensor adjustment.”)
3. Press the ] key
. Confirm that the display
of the operation panel
is changed over from [10]
→
[00] when the key is pressed within the
range of 6 to 8 times.
4. If the display changeover occurs deviating from the range of 6 times
to 8 times, or if the display changeover does not occur at all, loosen
the set screw
and make fine adjustments of the sensor slit
in
the directions of the arrow.
5. After the sensor slit
has been fixed, tread on the pedal and make
origin retrieval for the thread trimmer cam. Examine the sensor
changeover position in the steps 3 and 4 above.
6. Repeat the steps 2 ~ 5 above until the coincidence is secured.
(Caution) During adjustments, check the clearances A, B, and C of
the sensor slit
and the sensor
. If the clearances
seem to be insufficient, use the set screws
and
to
correct the gradient. While taking this action, continue
to work on the steps above.
o If the thread trimmer sensor
changeover takes place outside
the range, the moving knife may
interfere with the needle. This will
be a cause of injury or the
breakage of parts.
o If the thread trimmer sensor
changeover does not take place,
Error 305 occurs and the sewing
machine fails to start operating.
o If the sensor slit
has no clear-
ance against the sensor
, this
can be a cause of destruction in
the sensor slit
or the sensor
.
Summary of Contents for LK-1900A
Page 20: ... 16 10 Hook adjustment Standard Adjustment 0mm 0mm 7 5mm 0 05 0 1mm For DPX5 For DPX17 ...
Page 90: ... 86 Grease Grease Grease Grease Grease 8 Needle thread clamp mechanism area ...
Page 91: ... 87 Grease Grease A Grease Grease Grease Grease 9 LK 1901A relations ...
Page 92: ... 88 10 LK 1903A relations Grease Grease ...
Page 114: ... 111 12 Circuit diagrams 1 Block diagram A ...
Page 115: ... 112 2 Power supply circuit diagram A ...
Page 116: ... 113 3 Power supply circuit diagram B ...
Page 117: ... 114 4 Power supply circuit diagram C ...
Page 118: ... 115 5 Servo motor circuit diagram ...
Page 119: ... 116 6 Sensor pedal VR circuit diagram ...
Page 120: ... 117 7 MAIN PANEL board circuit diagram ...
Page 121: ... 118 8 Motor solenoid circuit diagram Thread trimmer Lifting the work clamp foot motor ...