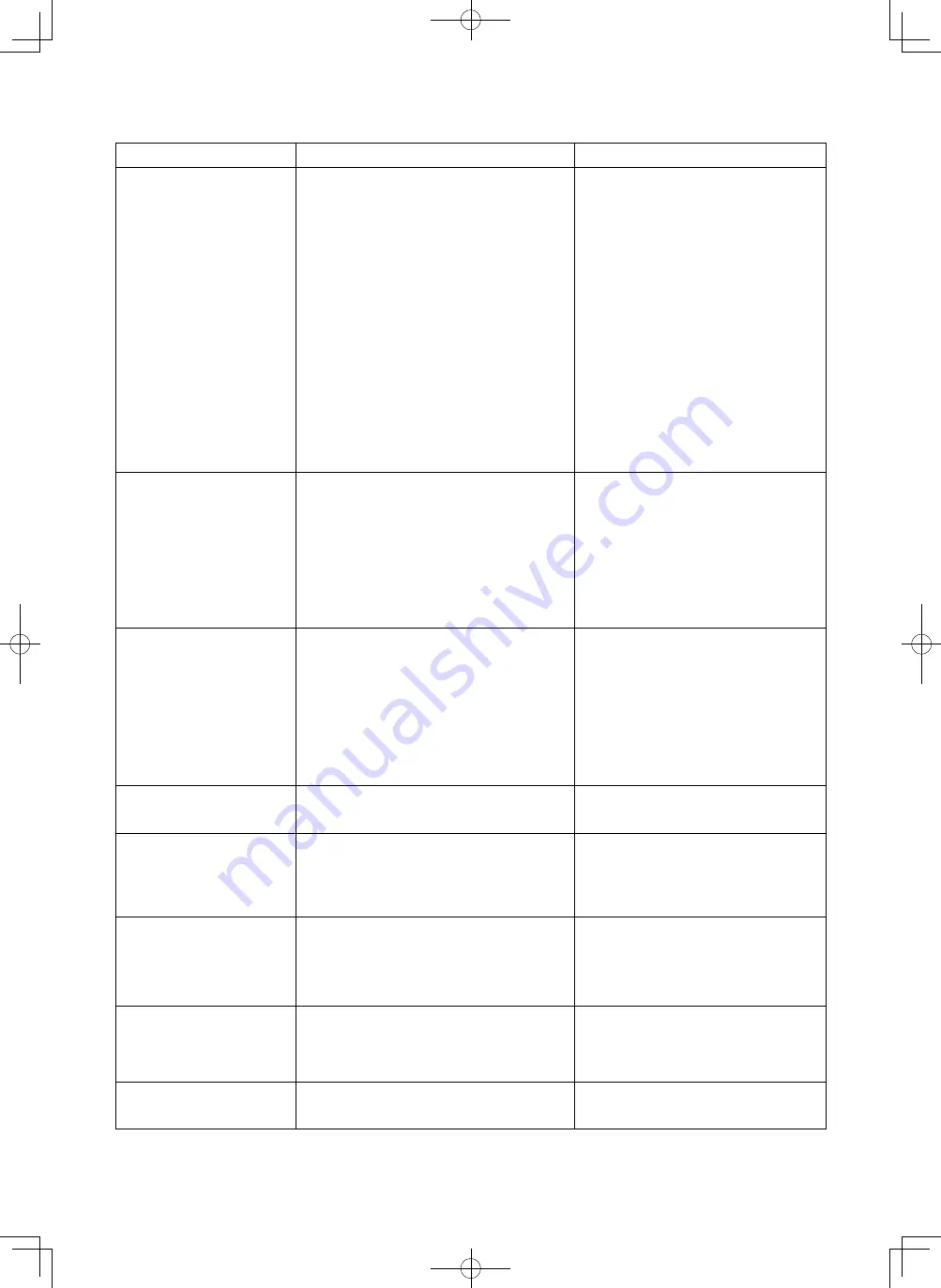
– 55 –
27. TROUBLES IN SEWING AND CORRECTIVE MEASURES
Troubles
Causes
Corrective measures
1. Thread breakage
(Thread frays or is worn out.)
(Needle thread trails 2 to 3
cm from the wrong side of the
fabric.)
1
Thread path, needle point, hook blade point or
bobbin case resting groove on the throat plate
has sharp edges or burrs.
2
Needle thread tension is too high.
3
Bobbin case opening lever provides an exces-
sive clearance at the bobbin case.
4
Needle comes in contact with the blade point of
hook.
5
Amount of oil in the hook is too small.
6
Needle thread tension is too low.
7
Thread take-up spring works excessively or the
stroke of the spring is too small.
8
Timing between the needle and the hook is ex-
cessively advanced or retarded.
™
Remove the sharp edges or burrs on the
blade point of hook using a
fi
ne emery pa-
per. Buff up the bobbin case resting groove
on the throat plate.
™
Decrease the needle thread tension.
™
Decrease the clearance provided between
the bobbin case opening lever and the bob-
bin.
Refer
to
“21.
ADJUSTING
THE
BOBBIN
CASE OPENING LEVER”.
™
Refer to “19. NEEDLE-TO-HOOK RELA-
TION”.
™
Adjust the amount of oil in the hook prop-
erly.
Refer to “7. LUBRICATION”.
™
Increase the needle thread tension.
™
Decrease the tension of the spring and in-
crease the stroke of the spring.
™
Refer to “19. NEEDLE-TO-HOOK RELA-
TION”.
2. Stitch skipping
1
Timing between the needle and the hook is ex-
cessively advanced or retarded.
2
Pressure of the presser foot is too low.
3
The clearance provided between the top end of
the needle eyelet and the blade point of hook is
not correct.
4
Hook needle guard is not functional.
5
Improper type of needle is used.
™
Refer to “19. NEEDLE-TO-HOOK RELA-
TION”.
™
Tighten the presser spring regulator.
™
Refer to “19. NEEDLE-TO-HOOK RELA-
TION”.
™
Refer to “20. ADJUSTING THE HOOK
NEEDLE GUARD”.
™
Replace the needle with one which is thicker
than the current needle by one count.
3. Loose stitches
1
Bobbin thread does not pass through the ten-
sion spring of the inner hook.
2
Thread path has been poorly
fi
nished.
3
Bobbin fails to move smoothly.
4
Bobbin case opening lever provides too much
clearance at the bobbin.
5
Bobbin thread tension is too low.
6
Bobbin has been wound too tightly.
™
Thread the bobbin thread correctly.
™
Remove rough parts with a
fi
ne emery pa-
per or buff it up.
™
Replace the bobbin or hook with a new one.
™
Refer to “21. ADJUSTING THE BOBBIN
CASE OPENING LEVER”.
™
Increase the bobbin thread tension.
™
Decrease the tension applied to the bobbin
winder.
4. Thread slips off the needle
eyelet simultaneously with
thread trimming.
1
Thread tension given by the tension controller
No. 1 is too high.
™
Decrease the thread tension given by the
tension controller No. 1.
5. Thread slips off the needle
eyelet at the start of sewing.
1
Thread tension given by the tension controller
No. 1 is too high.
2
Clamp spring has improper shape.
3
Bobbin thread tension is too low.
™
Decrease the thread tension given by the
tension controller No. 1.
™
Replace the clamp spring with a new one
or correct the current one.
™
Increase the bobbin thread tension.
6. Thread is not cut sharply.
1
The blades of moving knife and counter knife
have been improperly adjusted.
2
The knives have blunt blades.
3
Bobbin thread tension is too low.
™
Refer to “22. POSITION OF THE COUN-
TER KNIFE AND ADJUSTMENT OF THE
KNIFE PRESSURE”.
™
Replace the moving knife and counter knife
with new ones, or correct the current ones.
™
Increase the bobbin thread tension.
7. Thread remains uncut after
thread trimming.
( B o b b i n t h r e a d t r i m m i n g
failure when stitch length is
comparatively short.)
1
Initial position of the moving knife has been
improperly adjusted.
2
Bobbin thread tension is too low.
™
Refer to the Engineer’s Manual.
™
Increase the bobbin thread tension.
8. Thread breaks at the start of
sewing after thread trimming.
1
The needle thread is caught in the hook.
™
Shorten the length of thread remaining on
the needle after thread trimming.
Refer to “15. THREAD TENSION”.