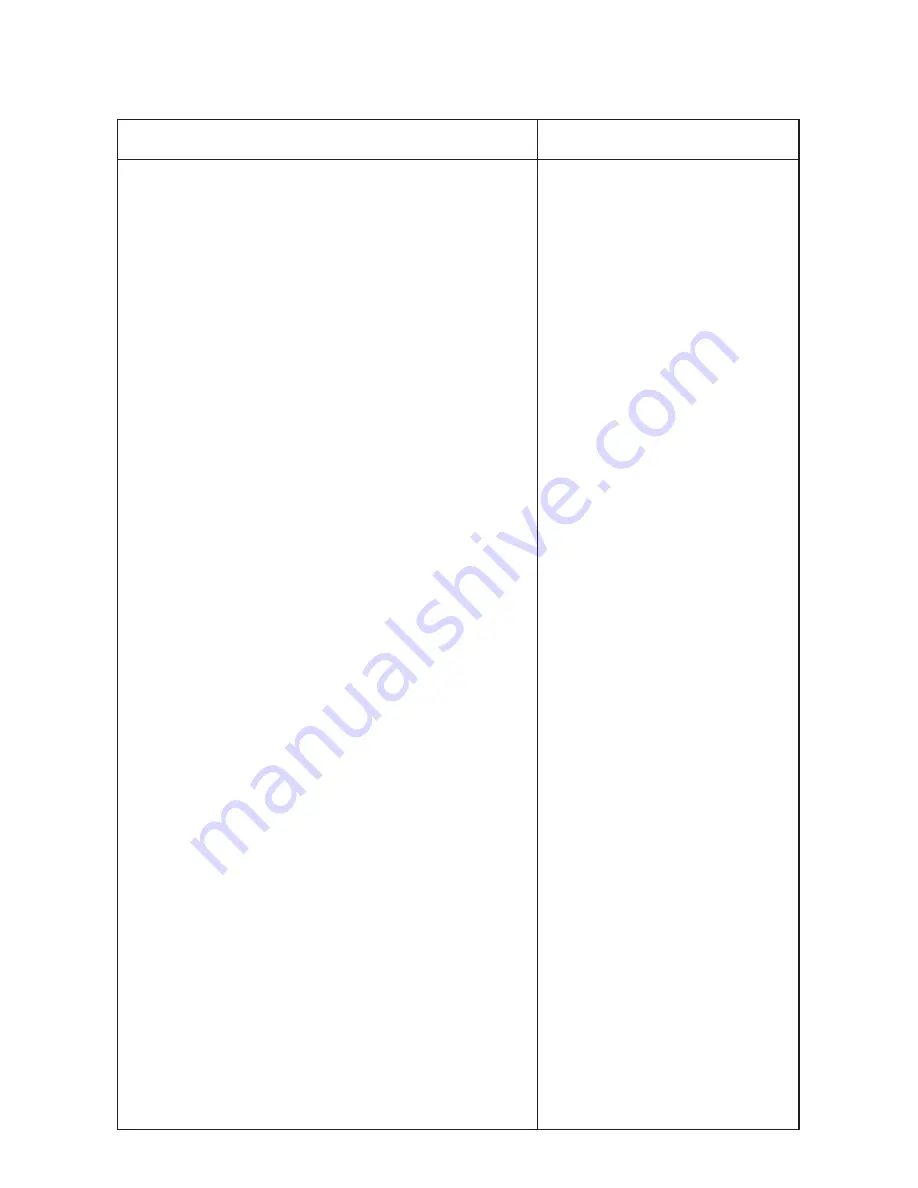
–
10
–
Standard Adjustment
Results of lmproper Adjustment
1. Loosen setscrews
3
, adjust the height of respective needle thread
guide rods
1
, and fix the rods with setscrews
3
.
(Caution) 1. Move the lateral position of needle thread guide base
2
fully to the right of slot.
2. When adjusting the height of needle thread guide rods
1
, install the rods so that the thread holes are parallel to
the thread holes of silicon container thread guide
4
so
that excessive resistance is not applied to threads.
2. Adjusting the position of needle thread guide base and silicon
container thread guide
(1) Loosen setscrews
5
and
6
and move silicon container thread
guide
4
up or down to adjust the height.
(2) Loosen setscrew
7
and adjust the lateral position of needle thread
guide base
2
.
™
When needle thread guide rod
1
is
raised, needle thread is loosened.
™
When needle thread guide rod
1
is
lowered, needle thread is tightened.
™
When silicon container thread guide
4
is raised, needle thread is loosened.
™
When silicon container thread guide
4
is lowered, needle thread is
tightened.
™
When needle thread guide base
2
is
moved to the left, needle thread is
loosened.