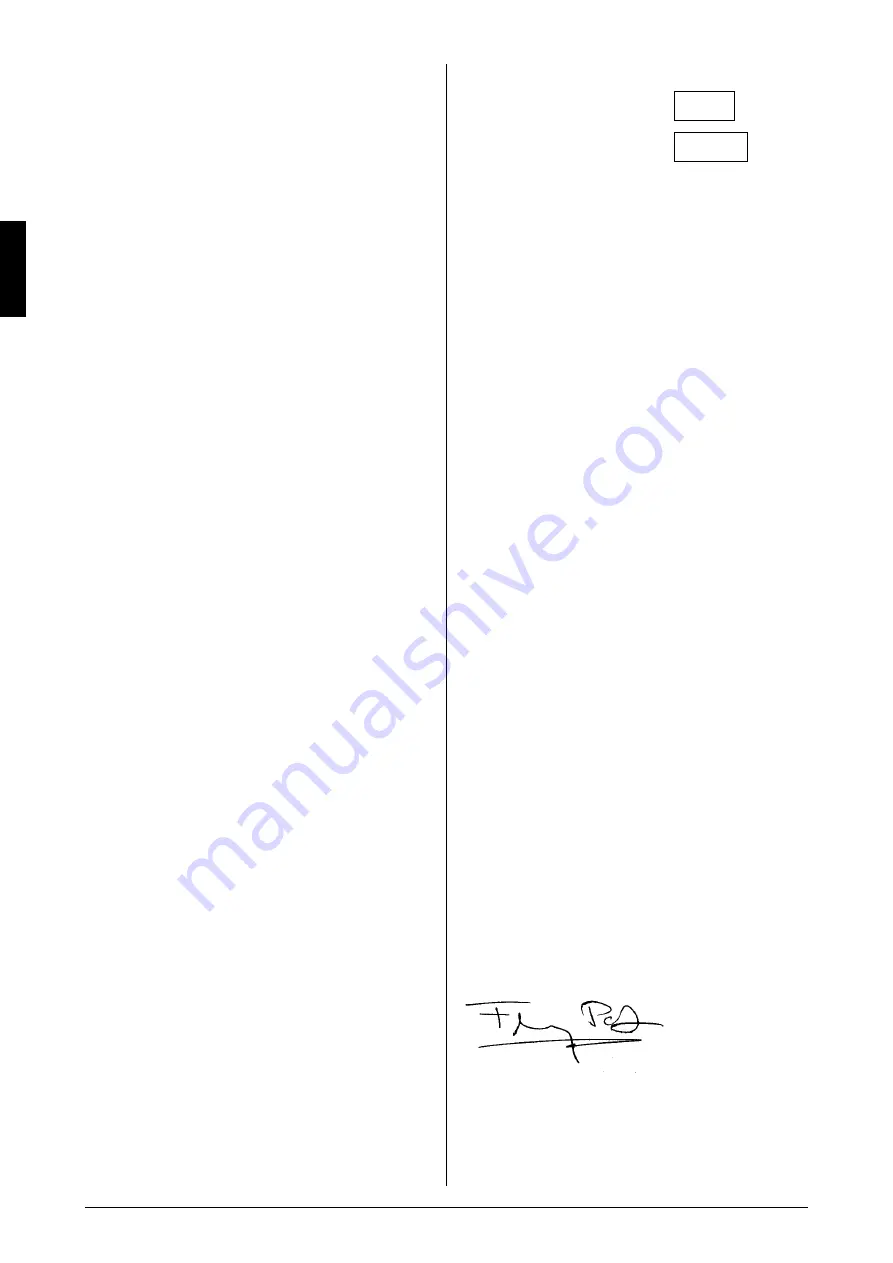
6
Pressure vessel
Pressure tested at: 425 liter:
4050 liter:
Directions for use
Application
Receiver for compressed air.
Receiver specifications See name plate.
Installation
Tubes, etc. must be made of
suitable materials.
Placement
Observe the working temperature
of the receiver.
Ensure that sufficient room for
inspection/maintenance is
available in a horizontal position.
The receiver must be kept in a
horizontal position.
Corrosion protection
The surface treatment must be
maintained as required.
Internal inspection at least every
5 years.
Drain moisture at least once a week.
Alternation/repair
No welding must be made on
pressurized parts.
Safety valve
Ensures that PS will not be exceeded.
Never adjust to a higher pressure
than PS.
The capacity of the valve must be
calculated in accordance
with the volume of air supplied by
the compressor.
(PS = Maximum working pressure
of the receiver)
Declaration of Conformity
NOTE: The declaration of conformity is only valid for units
operating at 20 V/50 Hz, x400 V/50 Hz, 12 V DC or 24 V DC.
The manufacturer, JUNAIR International A/S, declares that the
products mentioned in this manual are in conformity with:
• 87/404/EEC 90/488/EEC 9/68/EEC Council Directive
relating to Simple Pressure Vessels
• 89/92/EEC 91/68/EEC 9/44/EEC 9/68/EEC
Council Directive of Safety of Machinery
• 89/6/EEC Council Directive of Electric Magnetic
Compatibility
• 7/2/EEC Lowvoltage Directive
Flemming Petersen
Quality Manager
24 bar
18.3 bar
c) Failure in nonreturn valve which is creating a flow
restriction.
d) Check the piston gaskets. Replace, if necessary.
e) Desiccant has been contaminated and/or filter elements
have been clogged (this only applies to model „D“).
Replace. See "Adsorption Dryer Manual".
4. Loud noise from compressor:
a) Dirt or failure in nonreturn valve. Clean or replace.
b) Defective fan (this only applies to model „P“).
5. Compressor gets very hot:
a) Leaks. See point b.
b) Intake filter clogged. See point a.
c) Too high ambient temperature. Do not enclose unit in a
cupboard unless adequately ventilated. The compressor
should be placed in coolest possible place.
d) The cooling fan at the top of the cabinet does not run
(this only applies to model „P“). Check pipes and fuses.
e) Overloaded. Ensure compressor is correct model for
work load.
6. Compressor starts when no air is being tapped:
a) Leaks. See point b.
7. Compressor starts and stops more frequently than
usually:
a) Large amount of condensate in air receiver (on units
without dryer). On units with dryer condensate may be
found if dryer is defective (this only applies to model
„D“).
b) Leaks. See point b.
8. Compressor does not switch on against pressure or
does not switch off at max. pressure:
a) Defective pressure switch. Replace.
Operating manual
GB
Summary of Contents for 1000 motor
Page 2: ......
Page 11: ...11 10 4 A B 6 B A 6 8 90 120 psi 50 15 8 120 psi 15 14 2 30 psi 32 89 F BD PD 2000 RU...
Page 20: ...20 Motor spare parts model 1000 0100400 Spare parts...
Page 21: ...21 Motor spare parts model 2000 0200300 Spare parts...
Page 22: ...22 0200600 Spare parts model 2000 40B Spare parts...
Page 23: ...23 Spare parts model 2000 40BD2 0200610 Spare parts...
Page 24: ...24 0200620 Spare parts model 2000 40P Spare parts...
Page 25: ...25 0200630 Spare parts model 2000 40PD2 Spare parts...
Page 26: ...26 Spare parts model 4000 40B 0400200 Spare parts...
Page 27: ...27 Spare parts model 4000 40BD3 0400210 Spare parts...