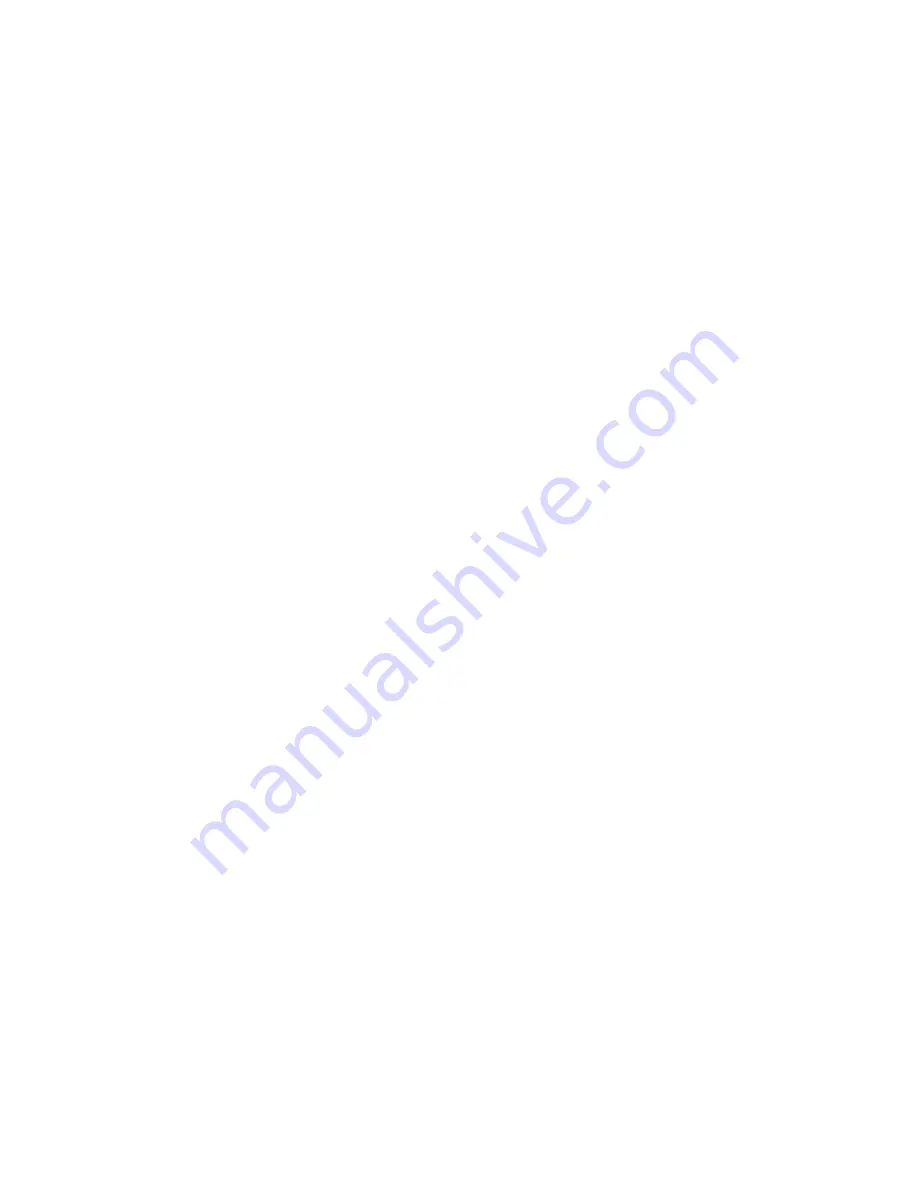
F 3
0903
.GB
3
Servicing and inspection
Thorough and expert servicing is one of the most important preconditions for safe op-
eration of the fork lift truck. The neglect of regular servicing intervals can lead to fork
lift truck failure and constitutes a potential hazard to personnel and equipment.
m
The indicated servicing intervals are based on single-shift operation under normal op-
erating conditions. For applications in dusty environments, or involving large temper-
ature fluctuations or multiple-shift operation, the servicing intervals must be
shortened accordingly.
The following servicing checklist indicates the operations to be performed and the re-
spective intervals to be observed. The servicing intervals are defined as follows:
W1 = every 50
operating
hours,
but at least once per week
M3 = every
500 operating hours, but at least every 3 months
M6 = every 1000 operating hours, but at least every 6 months
M12 = every 2000 operating hours, but at least every 12 months
A
The W1 maintenance intervals must be carried out by the operator / customer.
In the running-in phase of the truck, the following additional operations have to be car-
ried out:
After the first 50 to 100 operating hours, at the latest after two months:
– Retighten battery terminal screws and check condition of cell connectors.
– Perform visual checks of electrical and mechanical components.
– Check brake fluid.
– Check lifting chains for uniform tension.
– Check transmissions for leaks.
– Check screw connections and mechanical safety devices for tight seat.
– Check wheel nuts for tight seat and retighten, if required.
– Check hydraulic connections for leaks and retighten, if required.
F 3
0903
.GB
3
Servicing and inspection
Thorough and expert servicing is one of the most important preconditions for safe op-
eration of the fork lift truck. The neglect of regular servicing intervals can lead to fork
lift truck failure and constitutes a potential hazard to personnel and equipment.
m
The indicated servicing intervals are based on single-shift operation under normal op-
erating conditions. For applications in dusty environments, or involving large temper-
ature fluctuations or multiple-shift operation, the servicing intervals must be
shortened accordingly.
The following servicing checklist indicates the operations to be performed and the re-
spective intervals to be observed. The servicing intervals are defined as follows:
W1 = every 50
operating
hours,
but at least once per week
M3 = every
500 operating hours, but at least every 3 months
M6 = every 1000 operating hours, but at least every 6 months
M12 = every 2000 operating hours, but at least every 12 months
A
The W1 maintenance intervals must be carried out by the operator / customer.
In the running-in phase of the truck, the following additional operations have to be car-
ried out:
After the first 50 to 100 operating hours, at the latest after two months:
– Retighten battery terminal screws and check condition of cell connectors.
– Perform visual checks of electrical and mechanical components.
– Check brake fluid.
– Check lifting chains for uniform tension.
– Check transmissions for leaks.
– Check screw connections and mechanical safety devices for tight seat.
– Check wheel nuts for tight seat and retighten, if required.
– Check hydraulic connections for leaks and retighten, if required.
Summary of Contents for EKE 30-2 ac
Page 1: ...Operating instructions 50272276 EKE 30 2 ac G 08 02 09 03...
Page 3: ...0108 GB...
Page 7: ...0600 GB A 2...
Page 23: ...1002 GB D 6...
Page 26: ...E 3 0903 GB 1 2 17 18 12 13 14 19 15 16 3 4 5 6 7 8 9 10 11 20...
Page 37: ...0903 GB E 14...