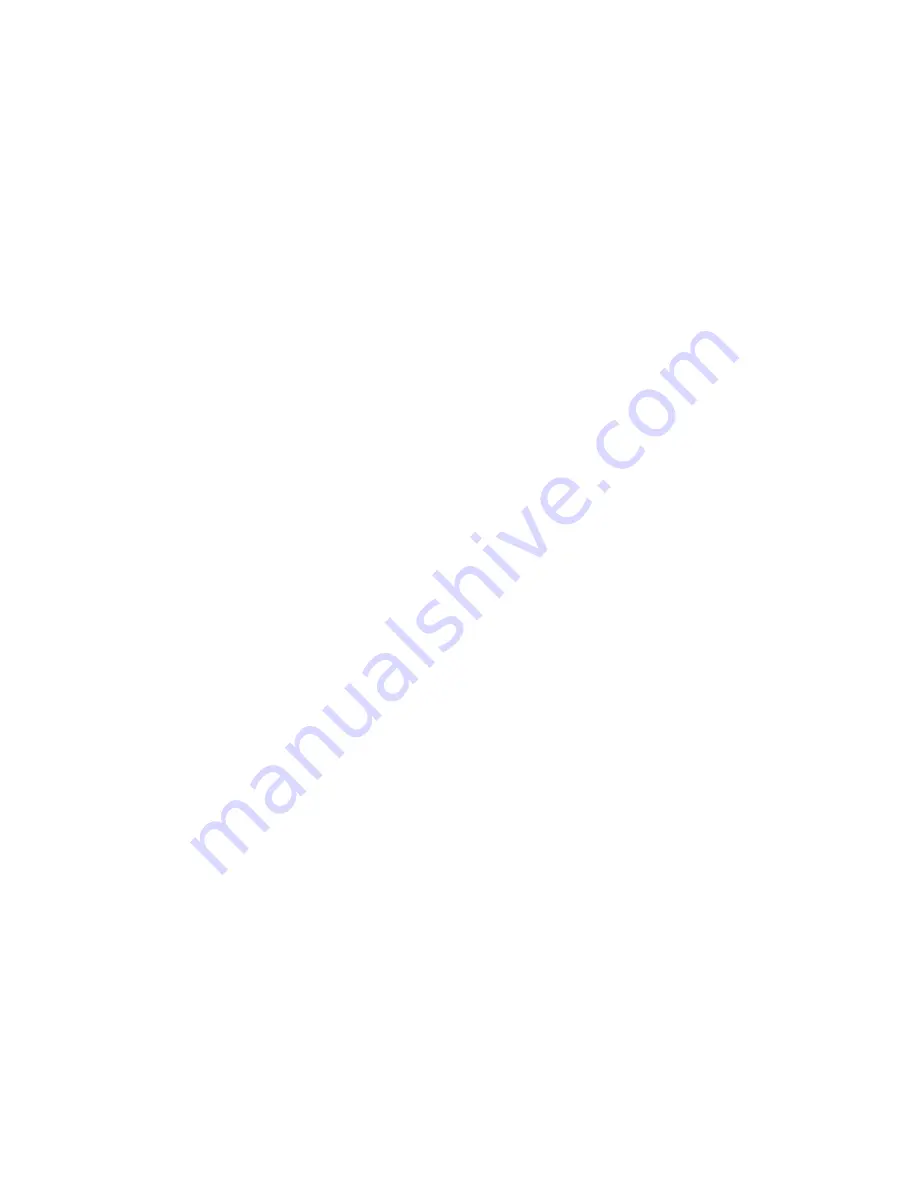
0506
.GB
10
4. Filling (manual/automatic)
The batteries should be filled with battery water as soon as possible before the battery
charging comes to an end; this ensures that the refilled water quantity is mixed with
the electrolyte. In normal operation it is usually sufficient to fill once a week.
5. Connection pressure
The water refilling unit is to be operated in such a way that the water pressure in the
water pipe is between 0.3 bars and 1.8 bars. The Aquamatic System has an operating
pressure range of between 0.2 bars and 0.6 bars. The BFS system has an operating
pressure range of 0.3 bars to 1.8 bars. Deviations from the pressure ranges impair
the system's functional reliability. This wide pressure range permits three types of fil-
ling.
5.1 Falling water
The height of the tank is chosen to suit whichever water refilling system is used. For
the Aquamatic System the installation height is 2 m to 6 m and for the BFS system
the installation height is 3 m to 18 m over the battery surface.
5.2 Pressurised water
The pressure-reducing valve in the Aquamatic System is set from 0.2 bars to 0.6 bars
and from 0.3 bars to 1.8 bars in the BFS system.
5.3 Water Refill Trolley (serviceMobil)
The submergible pump located in the ServiceMobil's tank generates the necessary
filling pressure. No difference in height is permitted between the standing level of the
ServiceMobil and the standing level of the battery.
6. Filling duration
The length of time needed to fill the batteries depends on the conditions under which
the battery is used, the ambient temperatures and the type of filling and/or the filling
pressure. The filling time is approx. 0.5 to 4 minutes. Where filling is manual, the wa-
ter feed pipe must be separated from the battery after filling.
7. Water quality
Only refilling water which conforms in quality to DIN 43530 part 4 may be used to fill
the batteries. The refilling unit (tank, pipelines, valves etc.) may not contain any kind
of dirt which could impair the functional reliability of the Aquamatic/BFS plug. For
safety reasons it is recommendable to insert a filter element (optional) with a max.
passage opening of 100 to 300 µm into the battery's main supply pipe.
0506
.GB
10
4. Filling (manual/automatic)
The batteries should be filled with battery water as soon as possible before the battery
charging comes to an end; this ensures that the refilled water quantity is mixed with
the electrolyte. In normal operation it is usually sufficient to fill once a week.
5. Connection pressure
The water refilling unit is to be operated in such a way that the water pressure in the
water pipe is between 0.3 bars and 1.8 bars. The Aquamatic System has an operating
pressure range of between 0.2 bars and 0.6 bars. The BFS system has an operating
pressure range of 0.3 bars to 1.8 bars. Deviations from the pressure ranges impair
the system's functional reliability. This wide pressure range permits three types of fil-
ling.
5.1 Falling water
The height of the tank is chosen to suit whichever water refilling system is used. For
the Aquamatic System the installation height is 2 m to 6 m and for the BFS system
the installation height is 3 m to 18 m over the battery surface.
5.2 Pressurised water
The pressure-reducing valve in the Aquamatic System is set from 0.2 bars to 0.6 bars
and from 0.3 bars to 1.8 bars in the BFS system.
5.3 Water Refill Trolley (serviceMobil)
The submergible pump located in the ServiceMobil's tank generates the necessary
filling pressure. No difference in height is permitted between the standing level of the
ServiceMobil and the standing level of the battery.
6. Filling duration
The length of time needed to fill the batteries depends on the conditions under which
the battery is used, the ambient temperatures and the type of filling and/or the filling
pressure. The filling time is approx. 0.5 to 4 minutes. Where filling is manual, the wa-
ter feed pipe must be separated from the battery after filling.
7. Water quality
Only refilling water which conforms in quality to DIN 43530 part 4 may be used to fill
the batteries. The refilling unit (tank, pipelines, valves etc.) may not contain any kind
of dirt which could impair the functional reliability of the Aquamatic/BFS plug. For
safety reasons it is recommendable to insert a filter element (optional) with a max.
passage opening of 100 to 300 µm into the battery's main supply pipe.
Summary of Contents for EMC 110/B 10
Page 1: ...Operating instructions 10003627 EMC 110 B 10 G 06 96 07 08...
Page 3: ...0108 GB...
Page 7: ...0506 GB 2...
Page 9: ...0600 GB A 2...
Page 14: ...B 5 0708 GB C Q h 1 h 3 h 13 l2 y 150 l1 Ast b 1 Wa b 1 b 2 b 5 e b 4...
Page 26: ...E 3 0600 GB 5 2 1 10 11 6 8 9 4 3 7...
Page 33: ......
Page 73: ...0506 GB 18...