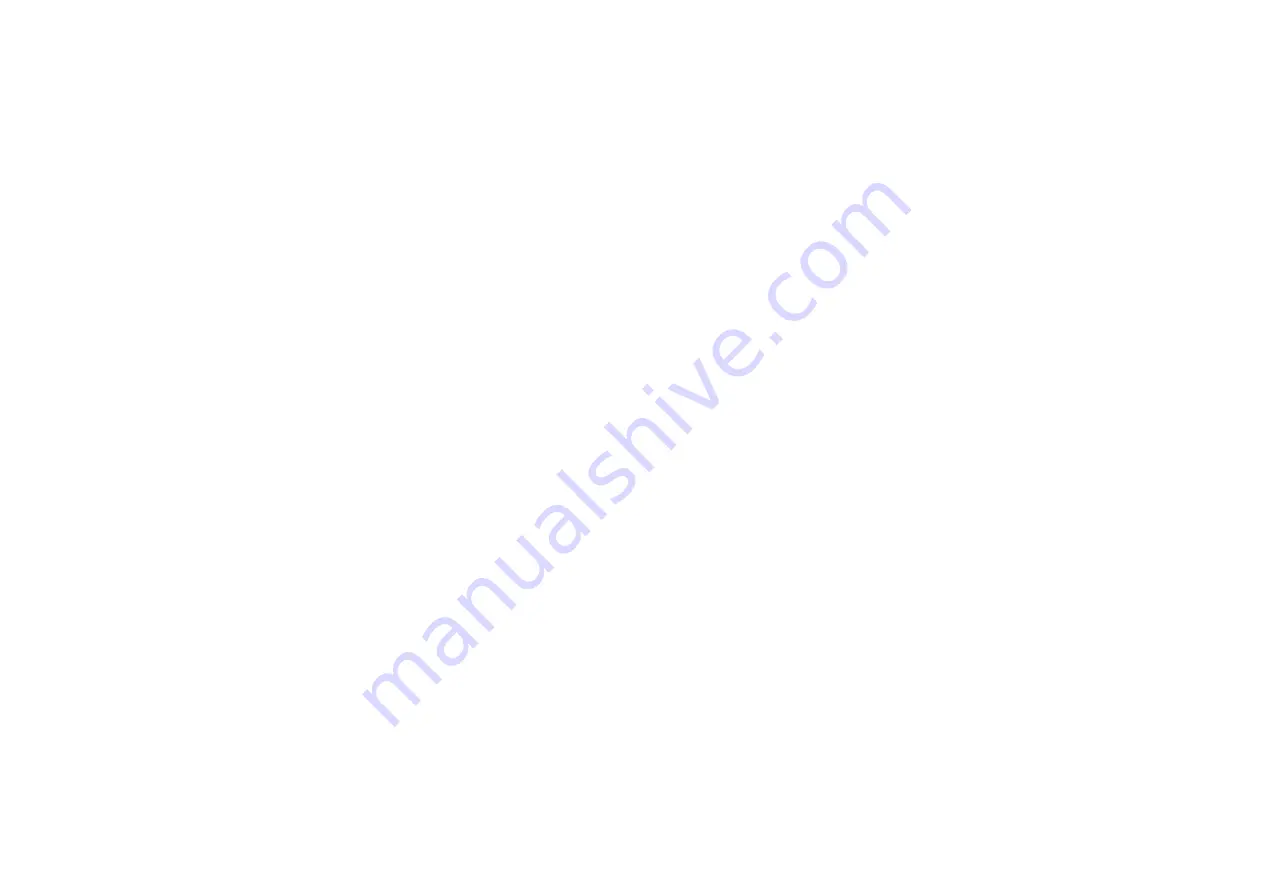
5
0506
.GB
3. Maintenance
3.1 Daily
Charge the battery after every discharge. Towards the end of charge the electrolyte
level should be checked and if necessary topped up to the specified level with purified
water. The electrolyte level must not fall below the anti-surge baffle or the top of the
separator or the electrolyte „min“ level mark.
3.2 Weekly
Visual inspection after recharging for signs of dirt and mechanical damage. If the bat-
tery is charged regularly with a IU characteristic curve an equalising charge must be
carried out (see point 2.3).
3.3 Monthly
At the end of the charge the voltages of all cells or bloc batteries should be measured
with the charger switched on, and recorded. After charging has ended the specific
gravity and the temperature of the electrolyte in all cells should be measured and re-
corded.
If significant changes from earlier measurements or differences between the cells or
bloc batteries are found further testing and maintenance by the service department
should be requested.
3.4 Annually
In accordance with DIN VDE 0117 at least once per year, the insulation resistance of
the truck and the battery must be checked by an electrical specialist.
The tests on the insulation resistance of the battery must be conducted in accordance
with DIN EN 60254-1.
The insulation resistance of the battery thus determined must not be below a value of
50
Ω
per Volt of nominal voltage, in compliance with DIN EN 50272-3.
For batteries up to 20 V nominal voltage the minimum value is 1000
Ω
.
4. Care of the battery
The battery should always be kept clean and dry to prevent tracking currents. Clea-
ning must be done in accordance with the ZVEI code of practice «The Cleaning of
Vehicle Traction batteries».
Any liquid in the battery tray must be extracted and disposed of in the prescribed man-
ner. Damage to the insulation of the tray should be repaired after cleaning, to ensure
that the insulation value complies DIN EN 50272-3 and to prevent tray corrosion. If it
is necessary to remove cells it is best to call in our service department for this.
5
0506
.GB
3. Maintenance
3.1 Daily
Charge the battery after every discharge. Towards the end of charge the electrolyte
level should be checked and if necessary topped up to the specified level with purified
water. The electrolyte level must not fall below the anti-surge baffle or the top of the
separator or the electrolyte „min“ level mark.
3.2 Weekly
Visual inspection after recharging for signs of dirt and mechanical damage. If the bat-
tery is charged regularly with a IU characteristic curve an equalising charge must be
carried out (see point 2.3).
3.3 Monthly
At the end of the charge the voltages of all cells or bloc batteries should be measured
with the charger switched on, and recorded. After charging has ended the specific
gravity and the temperature of the electrolyte in all cells should be measured and re-
corded.
If significant changes from earlier measurements or differences between the cells or
bloc batteries are found further testing and maintenance by the service department
should be requested.
3.4 Annually
In accordance with DIN VDE 0117 at least once per year, the insulation resistance of
the truck and the battery must be checked by an electrical specialist.
The tests on the insulation resistance of the battery must be conducted in accordance
with DIN EN 60254-1.
The insulation resistance of the battery thus determined must not be below a value of
50
Ω
per Volt of nominal voltage, in compliance with DIN EN 50272-3.
For batteries up to 20 V nominal voltage the minimum value is 1000
Ω
.
4. Care of the battery
The battery should always be kept clean and dry to prevent tracking currents. Clea-
ning must be done in accordance with the ZVEI code of practice «The Cleaning of
Vehicle Traction batteries».
Any liquid in the battery tray must be extracted and disposed of in the prescribed man-
ner. Damage to the insulation of the tray should be repaired after cleaning, to ensure
that the insulation value complies DIN EN 50272-3 and to prevent tray corrosion. If it
is necessary to remove cells it is best to call in our service department for this.
Summary of Contents for EME 112
Page 1: ...Operating instructions 77800386 EME 112 G 05 00 07 08 ...
Page 3: ...0108 GB 0108 GB ...
Page 7: ...0506 GB 2 0506 GB 2 ...
Page 9: ...0600 GB A 2 0600 GB A 2 ...
Page 25: ...1001 GB D 6 1001 GB D 6 ...
Page 28: ...E 3 0301 GB 5 2 1 4 3 6 7 8 9 10 E 3 0301 GB 5 2 1 4 3 6 7 8 9 10 ...
Page 35: ...0301 GB E 10 0301 GB E 10 ...
Page 47: ......
Page 65: ...0506 GB 18 0506 GB 18 ...