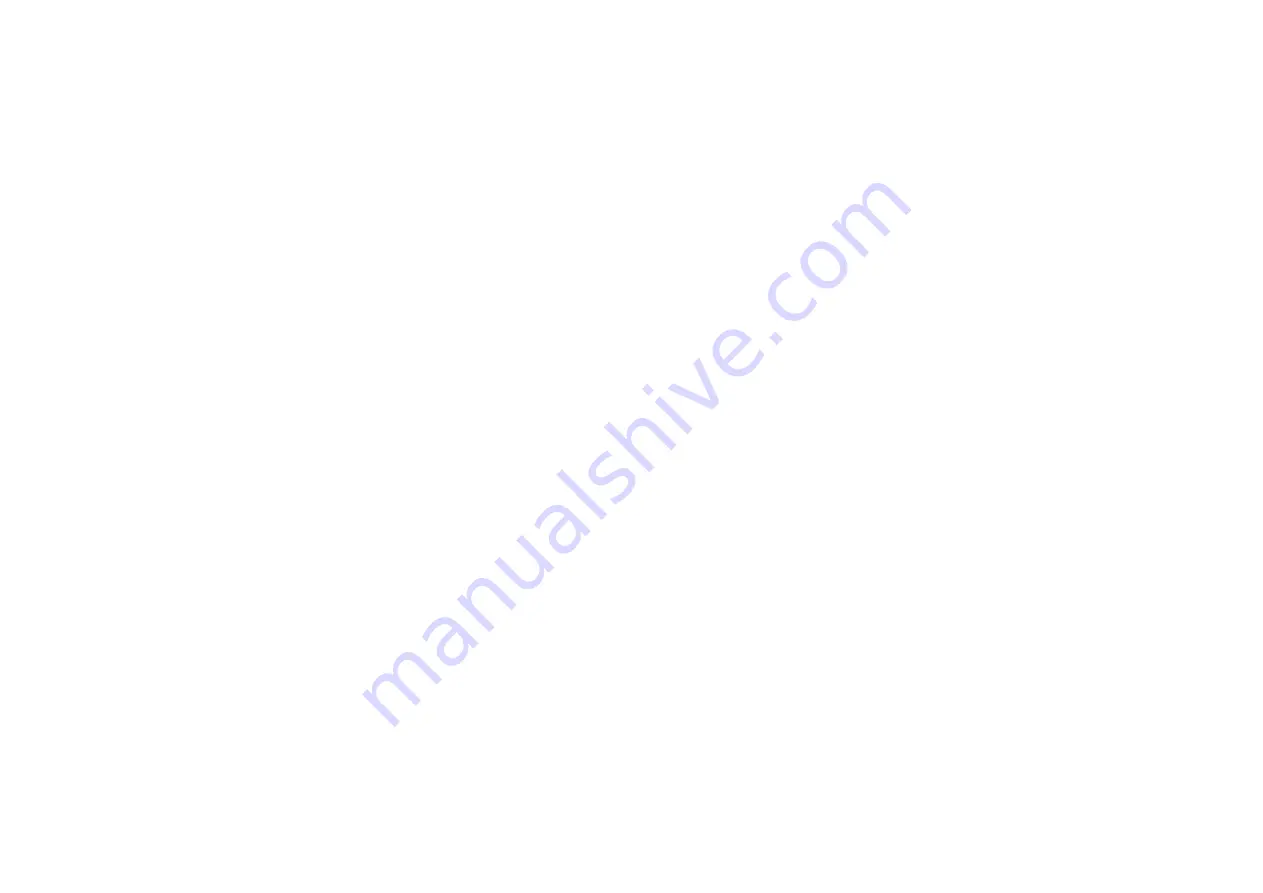
0
708
.USA
G 2
Cleaning:
The industrial truck must not be cleaned with flammable liquids. Before
cleaning the truck, all safety measures to prevent sparking (through short-circuits, for
example) must be taken. On battery-powered industrial trucks, the battery connector
must be pulled out. Electrical and electronic components must be cleaned with gentle
suction or compressed air and a non-conducting, antistatic brush.
IMPORTANT
If the industrial truck is cleaned with a water jet or a high-pressure cleaner, all
electrical and electronic components must be carefully covered first, since
moisture can lead to malfunctions.
Cleaning with a steam cleaner is prohibited.
On completion of cleaning, the procedures listed in "Restarting the vehicle" must be
carried out.
Working on the electrical system:
Only appropriately qualified employees are
permitted to work on the truck's electrical system. Before working on the electrical
system, all necessary measures must be taken to prevent electric shocks. On battery-
powered industrial trucks, the power supply to the truck must also be disconnected
by pulling out the battery connector.
Welding operations:
Before starting welding operations, electrical and electronic
components should be removed from the vehicle to prevent them from being
damaged.
Setting values:
In the event of repairs to or replacement of hydraulic / electrical /
electronic components, the vehicle-specific setting values must be retained.
Wheels / tires:
The quality of the wheels / rollers has a significant influence on the
stability and driving behavior of the industrial truck.
To ensure compliance with the specifications set out in the technical data sheet, only
manufacturer's original parts should be used if the wheels / rollers fitted by the
manufacturer have to be replaced.
If the wheels or tires are replaced, you must ensure that the truck's horizontal
alignment is retained (wheels / rollers must always be replaced in pairs, in other
words both left and right at the same time).
Lifting chains:
Lifting chains (if fitted) must be inspected at regular intervals. Chains
with torn, broken or missing link plates or protruding, twisted or pitted pins, or with
severe corrosion must be replaced. If chains are fitted in pairs, both chains must be
replaced. New chain anchor pins should be used if the chains are replaced. Lifting
chains wear quickly if they are not lubricated sufficiently. The intervals specified in the
maintenance checklist apply for normal use. More frequent lubrication is required
under more extreme conditions (dust, temperature). The specified chain spray must
be used in accordance with the instructions. Adequate lubrication cannot be achieved
by the external application of grease.
Hydraulic hose lines:
The hose lines must be replaced after a period of use of six
years.
Q
wW
Only trained service personnel may replace wheel arms.
0
708
.USA
G 2
Cleaning:
The industrial truck must not be cleaned with flammable liquids. Before
cleaning the truck, all safety measures to prevent sparking (through short-circuits, for
example) must be taken. On battery-powered industrial trucks, the battery connector
must be pulled out. Electrical and electronic components must be cleaned with gentle
suction or compressed air and a non-conducting, antistatic brush.
IMPORTANT
If the industrial truck is cleaned with a water jet or a high-pressure cleaner, all
electrical and electronic components must be carefully covered first, since
moisture can lead to malfunctions.
Cleaning with a steam cleaner is prohibited.
On completion of cleaning, the procedures listed in "Restarting the vehicle" must be
carried out.
Working on the electrical system:
Only appropriately qualified employees are
permitted to work on the truck's electrical system. Before working on the electrical
system, all necessary measures must be taken to prevent electric shocks. On battery-
powered industrial trucks, the power supply to the truck must also be disconnected
by pulling out the battery connector.
Welding operations:
Before starting welding operations, electrical and electronic
components should be removed from the vehicle to prevent them from being
damaged.
Setting values:
In the event of repairs to or replacement of hydraulic / electrical /
electronic components, the vehicle-specific setting values must be retained.
Wheels / tires:
The quality of the wheels / rollers has a significant influence on the
stability and driving behavior of the industrial truck.
To ensure compliance with the specifications set out in the technical data sheet, only
manufacturer's original parts should be used if the wheels / rollers fitted by the
manufacturer have to be replaced.
If the wheels or tires are replaced, you must ensure that the truck's horizontal
alignment is retained (wheels / rollers must always be replaced in pairs, in other
words both left and right at the same time).
Lifting chains:
Lifting chains (if fitted) must be inspected at regular intervals. Chains
with torn, broken or missing link plates or protruding, twisted or pitted pins, or with
severe corrosion must be replaced. If chains are fitted in pairs, both chains must be
replaced. New chain anchor pins should be used if the chains are replaced. Lifting
chains wear quickly if they are not lubricated sufficiently. The intervals specified in the
maintenance checklist apply for normal use. More frequent lubrication is required
under more extreme conditions (dust, temperature). The specified chain spray must
be used in accordance with the instructions. Adequate lubrication cannot be achieved
by the external application of grease.
Hydraulic hose lines:
The hose lines must be replaced after a period of use of six
years.
Q
wW
Only trained service personnel may replace wheel arms.
Summary of Contents for ETR 314
Page 1: ...Operating instructions 50 452 907 ETR 314 320 u 06 06 11 09 07 08 E Manual de instrucciones...
Page 7: ...0608 USA I 4 0608 USA I 4...
Page 9: ...0606 USA A 2 0606 USA A 2...
Page 24: ...D 9 0107 USA D 9 0107 USA...
Page 26: ...D 11 0107 USA D 11 0107 USA...
Page 103: ...0107 USA F 10 0107 USA F 10...
Page 123: ...0708 USA G 20 0708 USA G 20...
Page 135: ...0608 E I 4 0608 E I 4...
Page 137: ...0606 E A 2 0606 E A 2...
Page 152: ...D 9 0107 E D 9 0107 E...
Page 154: ...D 11 0107 E D 11 0107 E...
Page 225: ...0608 E E 66 0608 E E 66...
Page 235: ...0107 E F 10 0107 E F 10...
Page 255: ...0708 E G 20 0708 E G 20...