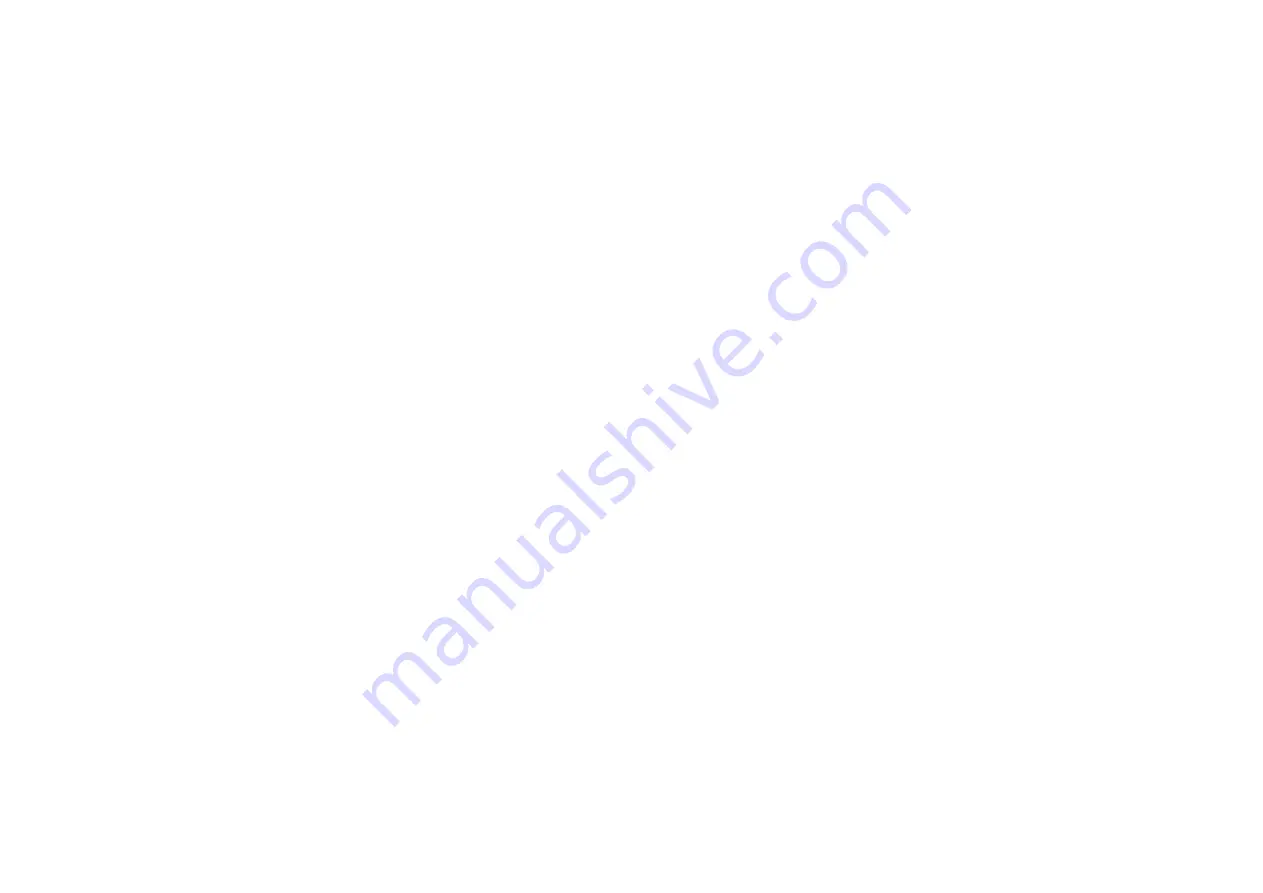
G 5
0
708
.USA
Inspection and repair of the forks used on industrial trucks:
The forks that are used must be inspected at least every 12 months (in the case of a
one-way swivel action) for damage or permanent deformation. If the vehicle is in
heavy use, they should be inspected more frequently.
The load capacity of an individual fork arm: Where forks are used in pairs (standard
configuration), the rated load capacity of the individual arms must be at least half the
rated load capacity of the industrial truck as specified by the manufacturer, and the
load center distance (nominal value) must be specified on the truck's nameplate.
Inspection:
The forks must be inspected carefully and at regular intervals by
qualified personnel for signs of damage, cracks, permanent deformation, etc., which
could adversely affect their safe use. All forks showing signs of such defects must be
replaced or removed from service and may not be used again if they cannot be
satisfactorily repaired by the fork manufacturer or by an appropriately qualified
specialist.
1. Surface cracks: The forks and, in particular, the underside and the weld seams
with which all attachments are joined to the body of the fork, must be given a
thorough visual inspection for cracks and – if necessary – subjected to non-
destructive material testing to identify cracks. The inspection for cracks must
include all special fixings between the body of the fork and the fork carrier,
including all bolted-on systems and wrought fixings for suspended devices or
undulating load suspension equipment. The forks must not be brought back into
service if cracks are found.
2. Linearity of the fork blade and fork back: Check the linearity of the top of the fork
blade and the front of the fork back. If the deviation from the straight line is more
than 0.5% of the length of the fork blade or the height of the fork back, the fork
must not be brought back into service until it has been properly repaired.
3. Fork angle (between the top of the fork blade and fork back, facing the load): Any
fork with a deviation of more than 3 degrees from the original specification must
not be brought back into service. After being removed from service, the fork must
be realigned and then inspected again.
4. Difference in height between fork tips: They determine the difference in height
between a pair of forks mounted on the fork carrier. If the difference in height
between the fork tips is more than 3% of the length of the fork blade, the forks
must not be brought back into service until they have been properly repaired.
5. Position lock (if provided in original configuration): Check that the position lock is
in good repair and is operating correctly. If a fault is found, the fork must not be
brought back into service until it has been properly repaired.
6. Wear:
– Fork blade and fork back: The fork blade and fork back – particularly in the area
of the fork stop – must be thoroughly inspected for wear. The fork must not be
brought back into service if the thickness of the fork back is less than or equal
to 90% of its original value.
– Positioning hooks (if provided in original configuration): The load-bearing
surface of the top hook and the retaining surfaces of both hooks must be
inspected for wear, cracks and other local deformation. If deformation is found
which leads to excessive play between the fork and the fork carrier, the fork
must not be brought back into service until it has been properly repaired.
G 5
0
708
.USA
Inspection and repair of the forks used on industrial trucks:
The forks that are used must be inspected at least every 12 months (in the case of a
one-way swivel action) for damage or permanent deformation. If the vehicle is in
heavy use, they should be inspected more frequently.
The load capacity of an individual fork arm: Where forks are used in pairs (standard
configuration), the rated load capacity of the individual arms must be at least half the
rated load capacity of the industrial truck as specified by the manufacturer, and the
load center distance (nominal value) must be specified on the truck's nameplate.
Inspection:
The forks must be inspected carefully and at regular intervals by
qualified personnel for signs of damage, cracks, permanent deformation, etc., which
could adversely affect their safe use. All forks showing signs of such defects must be
replaced or removed from service and may not be used again if they cannot be
satisfactorily repaired by the fork manufacturer or by an appropriately qualified
specialist.
1. Surface cracks: The forks and, in particular, the underside and the weld seams
with which all attachments are joined to the body of the fork, must be given a
thorough visual inspection for cracks and – if necessary – subjected to non-
destructive material testing to identify cracks. The inspection for cracks must
include all special fixings between the body of the fork and the fork carrier,
including all bolted-on systems and wrought fixings for suspended devices or
undulating load suspension equipment. The forks must not be brought back into
service if cracks are found.
2. Linearity of the fork blade and fork back: Check the linearity of the top of the fork
blade and the front of the fork back. If the deviation from the straight line is more
than 0.5% of the length of the fork blade or the height of the fork back, the fork
must not be brought back into service until it has been properly repaired.
3. Fork angle (between the top of the fork blade and fork back, facing the load): Any
fork with a deviation of more than 3 degrees from the original specification must
not be brought back into service. After being removed from service, the fork must
be realigned and then inspected again.
4. Difference in height between fork tips: They determine the difference in height
between a pair of forks mounted on the fork carrier. If the difference in height
between the fork tips is more than 3% of the length of the fork blade, the forks
must not be brought back into service until they have been properly repaired.
5. Position lock (if provided in original configuration): Check that the position lock is
in good repair and is operating correctly. If a fault is found, the fork must not be
brought back into service until it has been properly repaired.
6. Wear:
– Fork blade and fork back: The fork blade and fork back – particularly in the area
of the fork stop – must be thoroughly inspected for wear. The fork must not be
brought back into service if the thickness of the fork back is less than or equal
to 90% of its original value.
– Positioning hooks (if provided in original configuration): The load-bearing
surface of the top hook and the retaining surfaces of both hooks must be
inspected for wear, cracks and other local deformation. If deformation is found
which leads to excessive play between the fork and the fork carrier, the fork
must not be brought back into service until it has been properly repaired.
Summary of Contents for ETR 314
Page 1: ...Operating instructions 50 452 907 ETR 314 320 u 06 06 11 09 07 08 E Manual de instrucciones...
Page 7: ...0608 USA I 4 0608 USA I 4...
Page 9: ...0606 USA A 2 0606 USA A 2...
Page 24: ...D 9 0107 USA D 9 0107 USA...
Page 26: ...D 11 0107 USA D 11 0107 USA...
Page 103: ...0107 USA F 10 0107 USA F 10...
Page 123: ...0708 USA G 20 0708 USA G 20...
Page 135: ...0608 E I 4 0608 E I 4...
Page 137: ...0606 E A 2 0606 E A 2...
Page 152: ...D 9 0107 E D 9 0107 E...
Page 154: ...D 11 0107 E D 11 0107 E...
Page 225: ...0608 E E 66 0608 E E 66...
Page 235: ...0107 E F 10 0107 E F 10...
Page 255: ...0708 E G 20 0708 E G 20...