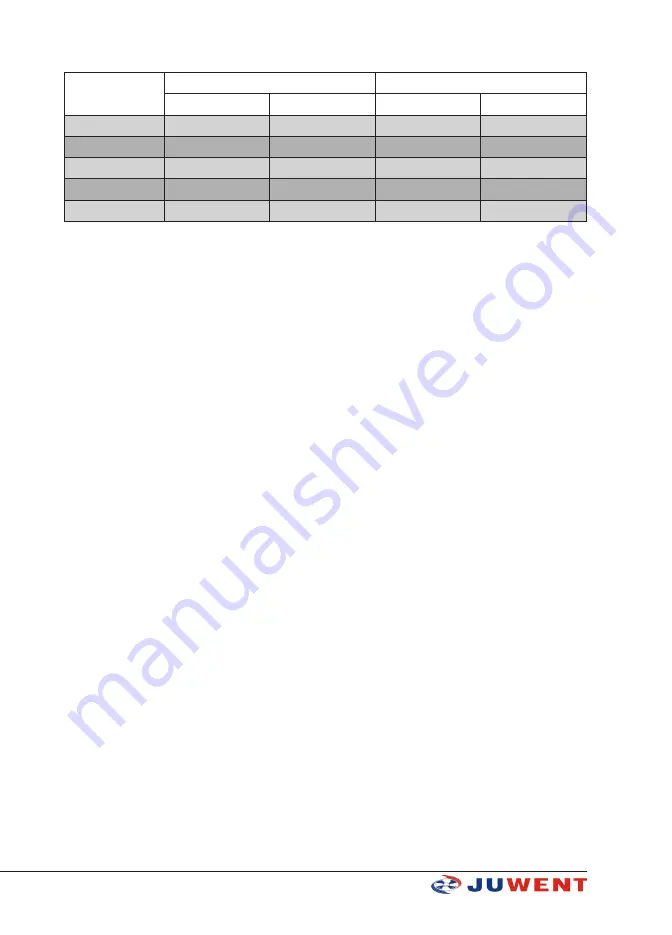
32
www.juwent.com.pl
Unit size
Preliminary filter M5
Very fine filter F7
Dimensions
No. of pieces
Dimensions
No. of pieces
OptiMax-10
695x300x48
2
695x300x360
1
OpitMax-20
495x450x48
4
495x450x500
2
OptiMax-30
645x600x48
4
645x600x500
2
OptiMax-40
545x775x48
6
545x775x600
3
OptiMax-50
645x925x48
6
645x925x600
3
15.3. WATER HEATING COIL
Water heating coil in use should be equipped with automatic anti-freeze protection system.
Alternatively, in the winter period, the heating coil can be supplied with a non-freezing agent (e.g.
glycol solution). If the supply of a non-freezing agent is cut or during the unit idle period and
possibility of decreasing air temperature below +5°C, the heating coil should be emptied.
At least every 6 months check whether heating coil panels are not contaminated. Dust deposits on
the heating coil surface reduce its heating capacity and increase in pressure drop at the air side.
Even if the unit is equipped with filters, it is natural that at the air supply side dust will deposit on the
heating coil panels. If excessive soiling is found, clean using the following methods:
»
using vacuum-cleaner with soft nozzle from the air supply side,
»
blowing compressed air jet in the direction opposite to the normal air flow, directing the air
jet in line with panel arrangement,
»
washing with water with cleaning agents which cause no corrosion to aluminium and copper.
Before cleaning provide protection of the adjacent unit sections against released dirt and dust.
In order to achieve full thermal efficiency, the heating coil must be well deaerated. Therefore air
vents plugs are used. They should be placed in the top most point of the supply system.
When the device remains in standstill condition, the heating medium flow should be limited to a
minimum so that the temperature inside the device is no more than +60°C. Increase in temperature
above this value may cause damage to some components or sub-assemblies (motor, bearings,
plastic parts, etc.) installed in sections adjacent to the heating coil.
For heating coil supplied with a solution of glycol, additionally check the contents and density of
glycol in the circuit.
15.4. WATER COOLING COIL
At least every 6 months check whether cooling coil panels are not contaminated. Dust deposits on
the cooling coil surface reduce its capacity and increase pressure drop at the air side. Even if the unit
is equipped with filters, it is natural that at the air supply side dust will deposit on the cooling coil
panels. If excessive soiling is found, clean using the following methods:
»
using vacuum-cleaner with soft nozzle from the air supply side,
»
blowing compressed air jet in the direction opposite to the normal air flow, directing the air
jet in line with panel arrangement,
»
washing with water with cleaning agents which cause no corrosion to aluminium and copper.
Before cleaning provide protection of the adjacent unit sections against released dirt and dust.
In order to achieve full efficiency, the cooling coil must be well deaerated. Therefore air vents plugs
are used. They should be placed in the top most point of the supply system.
When inspecting cleanliness, also make sure to check whether droplet eliminator is clean and
condensate tray drainage is operable, and so as the water siphon. Before the unit is started, fill
the water siphon with water. When contaminated, wash droplet eliminator with warm water with
detergents.
For cooling coil supplied with a solution of glycol, additionally check the contents and density of
glycol in the circuit.