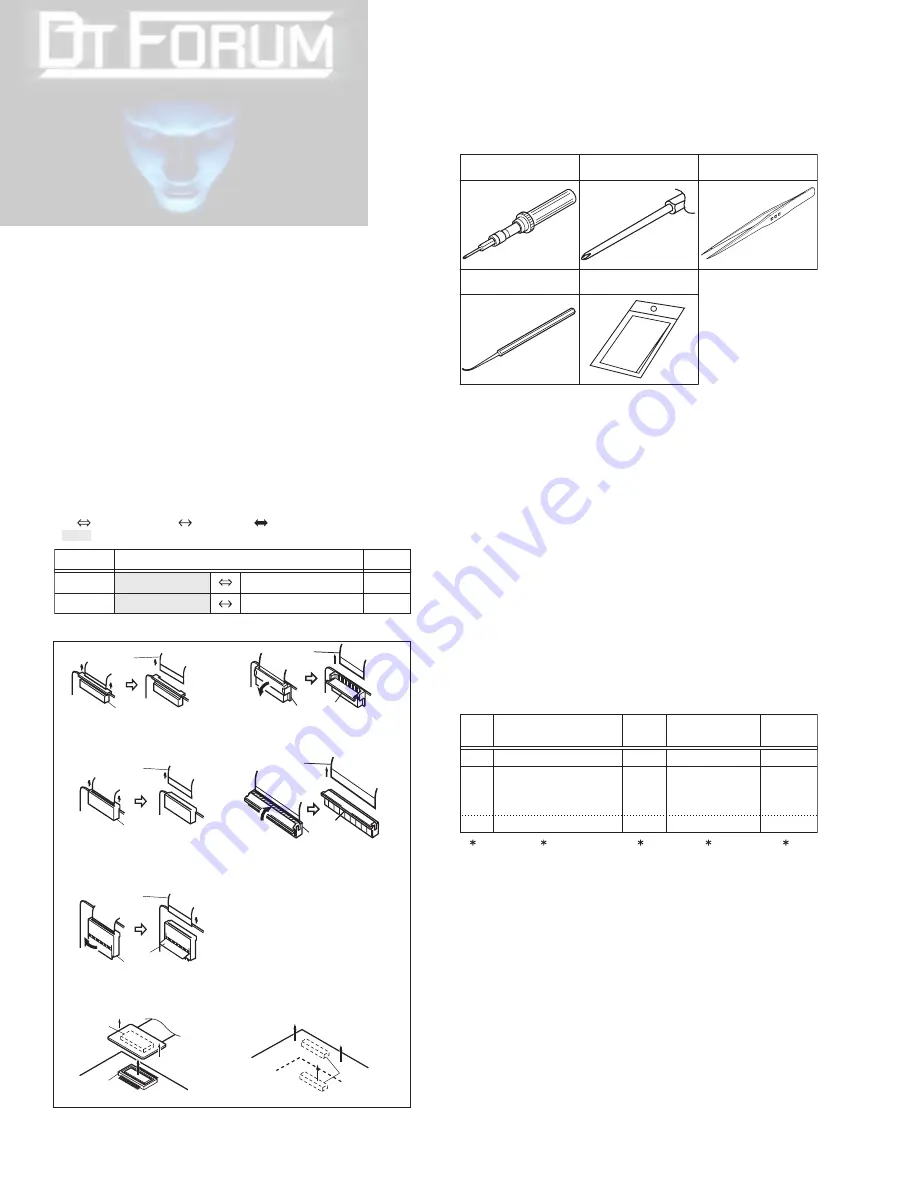
1-6 (No.YF219)
SECTION 3
DISASSEMBLY
3.1
BEFORE ASSEMBLY AND DISASSEMBLY
3.1.1 Precautions
• Be sure to disconnect the power supply unit prior to mounting
and soldering of parts.
• Prior to removing a component part that needs to disconnect
its connector(s) and its screw(s), first disconnect the wire(s)
from the connector(s), and then remove the screw(s).
• When connecting/disconnecting wires, pay enough attention
not to damage the connectors.
• When inserting the flat wire to the connector, pay attention to
the direction of the flat wire.
• Be careful in removing the parts to which some spacer or
shield is attached for reinforcement or insulation.
• When replacing chip parts (especially IC parts), first remove
the solder completely to prevent peeling of the pattern.
• Tighten screws properly during the procedures. Unless
otherwise specified, tighten screws at a torque of 0.078N
·
m
(0.8kgf
·
cm). However, as this is a required value at the time of
production, use the value as a measuring stick when
proceeding repair services. (See "SERVICE NOTE" as for
tightening torque.)
3.1.2 Destination of connectors
3.1.3 Disconnection of connectors (Wires)
Fig.3-1-1
3.1.4 Tools required for disassembly and assembly
Fig.3-1-2
•
Torque driver
Be sure to use to fastening the mechanism and exterior parts be-
cause those parts must strictly be controlled for tightening torque.
•
Bit
This bit is slightly longer than those set in conventional torque
drivers.
•
Tweezers
To be used for removing and installing parts and wires.
•
Chip IC replacement jig
To be used for replacement of IC.
•
Cleaning cloth
Recommended cleaning cloth to wipe down the video heads,
mechanism (tape transport system), optical lens surface.
3.2
ASSEMBLY AND DISASSEMBLY OF MAIN PARTS
3.2.1 Assembly and disassembly
When reassembling, perform the step(s) in reverse order.
(
∗
1) Order of steps in Procedure
When reassembling, preform the step(s) in the reverseorder.
These numbers are also used as the identification (location)
No. of parts Figures.
(
∗
2) Part to be removed or installed.
(
∗
3) Fig. No. showing Procedure or Part Location.
(
∗
4) Identification of part to be removed, unhooked, unlocked,
released, unplugged, unclamped or unsoldered.
S = Screw L = Lock, Release, Hook
SD = Solder CN = Connector
[Example]
• 4 (S1a) = Remove 4 S1a screws.
• 3 (L1a) = Disengage 3 L1a hooks.
• 2 (SD1a) = Unsolder 2 SD1a points.
• CN1a = Remove a CN1a connector.
(
∗
5) Adjustment information for installation.
CN2a
CN2b
MAIN CN101
MAIN CN103
40
10
CONN. No.
PIN No.
CONNECTOR
Two kinds of double-arrows in connection tables respectively
show kinds of connector/wires.
: The connector of the side to remove
: Wire
: Flat wire
: Board to board (B-B)
MONI BW
CN761
MINI BW
CN762
B-B Connector
B-B Connector
B-B Connector
· Pull the both ends of the board in the direction of the arrow, and remove the B-B Connector.
· Pull the both ends of the board in the direction
of the arrow, and remove the B-B Connector.
FPC Connector
Wire
· Pull both ends of the connector in the arrow
direction, remove the lock and disconnect the flat
wire.
FPC Connector
Lock
Wire
· Extend the locks in the direction of the arrow for
unlocking and then pull out the wire. After
removing the wire, immediately restore the locks
to their original positions because the locks are
apt to come off the connector.
· Extend the locks in the direction of the arrow for
unlocking and then pull out the wire. After
removing the wire, immediately restore the locks
to their original positions because the locks are
apt to come off the connector.
· Extend the locks in the direction of the arrow for
unlocking and then pull out the wire. After
removing the wire, immediately restore the locks
to their original positions because the locks are
apt to come off the connector.
FPC Connector
Wire
FPC Connector
Lock
Wire
FPC Connector
Wire
Lock
Lock
Cleaning cloth
KSMM-01
Torque driver
YTU94088
Bit
YTU94088-003
Chip IC replacement jig
PTS40844-2
Tweezers
P-895
( 4)
( 5)
( 2)
( 3)
( 1)
TOP COVER ASSY
UPPER ASSY
(Inc. VF ASSY,
SPEAKER/MONITOR)
E.VF UNIT(B/W)
C1
C2-1
C2-2
4(S1a), 3(L1a),CN1a
(S2a),2(S2b),3(S2c)
2(SD1a),
L2,CN2a,b
2(S8),L8,CN8a
-
-
NOTE 8
[1]
[2]
[8]
STEP
No.
PART
NOTE
Fig.
No.
POINT