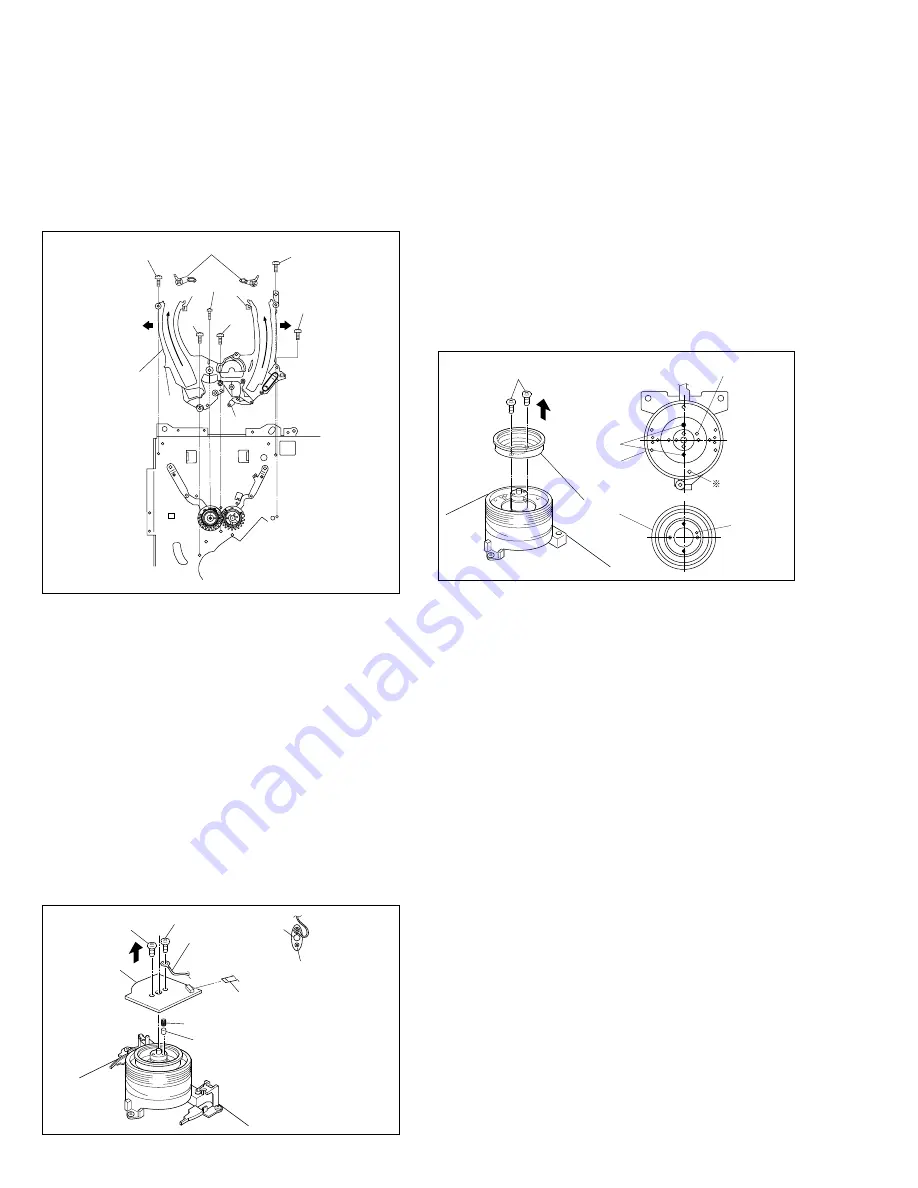
2-8
2.2.16
Guide rail
(1) Take out the 5 screws (A) and 1 screw (B).
(2) By expanding the rails on the outer sides of the guide
rail, remove the 2 pole base assemblies (supply, take up).
(3) Disengage the 4 claws and remove the guide rail.
Note:
• Before removing the guide rail, it is required to remove
the drum assembly.
Fig.2-2-16a
2.2.19
Upper drum assembly
Notes:
• To replace the upper drum assembly only may not be
possible with some models. For upper drum assem-
bly replacement, refer to the parts list. (When the parts
number of the upper drum assembly is not listed on
the parts list, then this cannot be replaced.)
• When replacement is required, control the up- down
movement of the brush. Never apply grease.
• When replacing the upper drum assembly, replace it
the together with the washer.
1. How to remove
(1) Remove the stator assembly and rotor assembly.
(2) Loosen the screw of the collar assembly using a 1.5 mm
hexagonal wrench and remove the collar assembly. Also
remove the brush, spring and cap at one time.
(3) Remove the upper drum assembly and remove the
washer using tweezers.
2.2.17 Stator assembly
(1) Remove the flat cable.
(2) Remove the two screws (A), (B) and remove the lug wire.
(3) Remove the stator assembly by lifting in the arrow-indi-
cated direction. (Take care that the brush spring does not
jump out.)
Notes:
• Be careful not to lose the brush and spring.
• There are some models that do not use the lug wire.
Refer to the parts list for these models.
• When tightening the screw (B), place the caulked part
of the lug terminal near to the shaft of the drum and
then tighten it.
• After installation, be sure to perform the switching
point adjustment according to the electrical adjustment
procedure.
2.2.18 Rotor assembly
1. How to remove
(1) Remove the stator assembly.
(2) Remove the two screws (B) and remove the rotor assem-
bly.
2. How to install
(1) Match the phases of the upper drum assembly and the
rotor assembly as indicated in Fig.2-2-18a.
(2) Place the upper drum assembly hole (a) over the rotor
assembly holes (b) (with three holes to be aligned) and
tighten the two screws (B). (See Fig.2-2-18a.)
Note:
• When installing the rotor assembly, note that a normal
picture cannot be obtained without ensuring the phase
matching as mentioned below.
(A)
(A)
(A)
(A)
(A)
(B)
Claw
Claw
Claw
Claw
Pole base assembly
Guide rail
Fig.2-2-17a
Stator
assembly
Lug wire
(Note)
Spring
Brush
Flat cable
(Take care not to mix up the
polar faces when installing.)
Screw (A)
Screw (A)
Lug wire
Drum
shaft
Screw (B)
Fig.2-2-18a
Screws (B)
Rotor assembly
Hole(a)
Hole(b)
Screw holes
Upper drum
assembly
The hole is not in
line but is offset
toward the right.