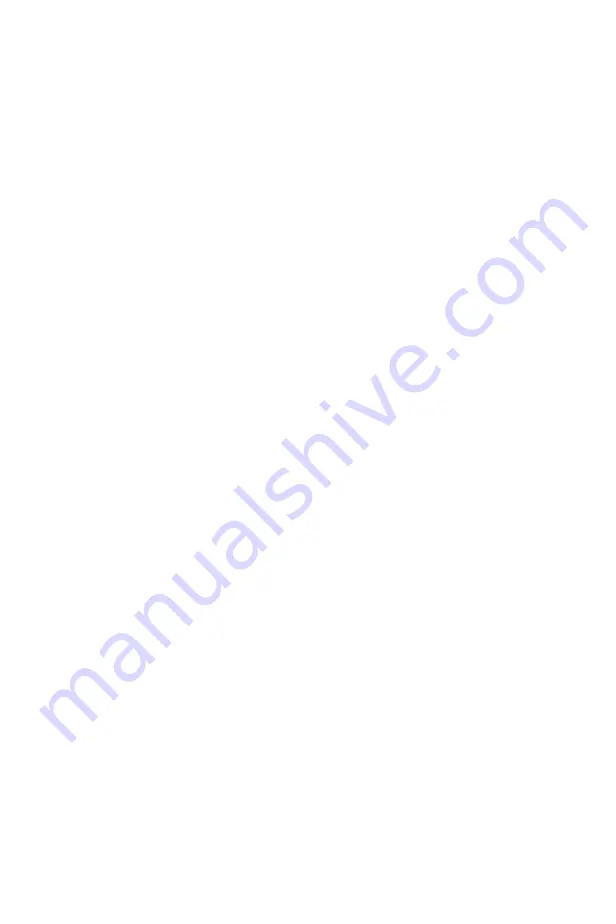
Instruction Manual
Section Five
wheel, 1/16 inch to the right of the wheel edge. It is not necessary to unlock
the hex nut fastening the Arm (B982-12) to the Toothrest Adjustment
Collar before moving the arm by means of the knob (3015-A). The posi
tion of the machine table and the Toothrest Holder (B982-11) must be
adjusted in order to allow sufficient spindle travel space for the length
of the end mill flutes. The toothrest blade end must catch the outer face
edge of a tooth and still leave clearance (ON THE ORDER OF 1/32 INCH)
between the rest and the wheel. Once the blade is positioned near the
wheel, set the two table stops against the stop block to prevent any move
ment. Adjust the micrometer of the toothrest to bring the tooth face
edge to the same height as the center of the fixture. Use the machine
height gauge to make this measurement.
5. Set the clearance angle. To do this, rotate the Toothrest Adjustment
Collar (B982CC) by loosening the top hex socket screw slightly with a 3/16
hex wrench (the bottom two screws should be left just tight enough so
that the collar can be swiveled by hand when the top one is loosened).
Rotate the collar so that the cutter teeth rotate toward the wheel (clock
wise facing the rear of the fixture), the required number of clearance
angle degrees. The clearance angle is read directly on the scale on the
periphery of the collar.
6. An alternate method of setting the clearance is to use the method em
ployed in Chapter 4, only using the toothrest blade. The blade can be
lowered by its micrometer according to the amounts stated in Table II,
rather than lowering the machine Wheelhead.
7. Set the front Index Collar (B982-35) and rear Stop Collar (B982-36) on
the sliding spindle in order to limit the travel to the right or left. The
⅛
inch wrench loosens these collars. Travel to the right should be just far
enough to allow the cutter to escape the toothrest so as to be indexed
(ROTATED) for the next tooth.
B. Grinding Procedure:
1. Each tooth's land back of the cutting edge is rotated past the wheel edge
while sliding on the fixed toothrest. The basic grinding action is the
same as when the mill is mounted in a fixed spindle workhead and the
table of the machine is moved in order to slide the mill past the wheel.
Except in this instance, the operator moves the cutter the full length of
the teeth to be ground toward the center of the wheel (past the peripheral
grinding edge), by depressing the entire fixture spindle away slightly from
the wheel, using the Rocker Arm and Knob (B982-21). Then after re
leasing the lever and lightly touching the wheel with the land to be ground,
draw the spindle tube back to the starting position, making sure that the
tooth face contacts the finger rest at all times. In other words, keep
light clockwise pressure on the spindle when it is retracted during the
grinding of each land. In order not to dull the cutting edges, it is best
to come off from the toothrest each time a land cut has been completed,
prior to indexing to the next tooth. Use the same grinding practices and
visual checks described in Chapter 4. Grind a secondary clearance angle
on the periphery of the mill by making an additional adjustment of the
clearance angle bracket.
2. It is possible to use the air-bearing fixture using the plain wheel method.
- 9 4 —