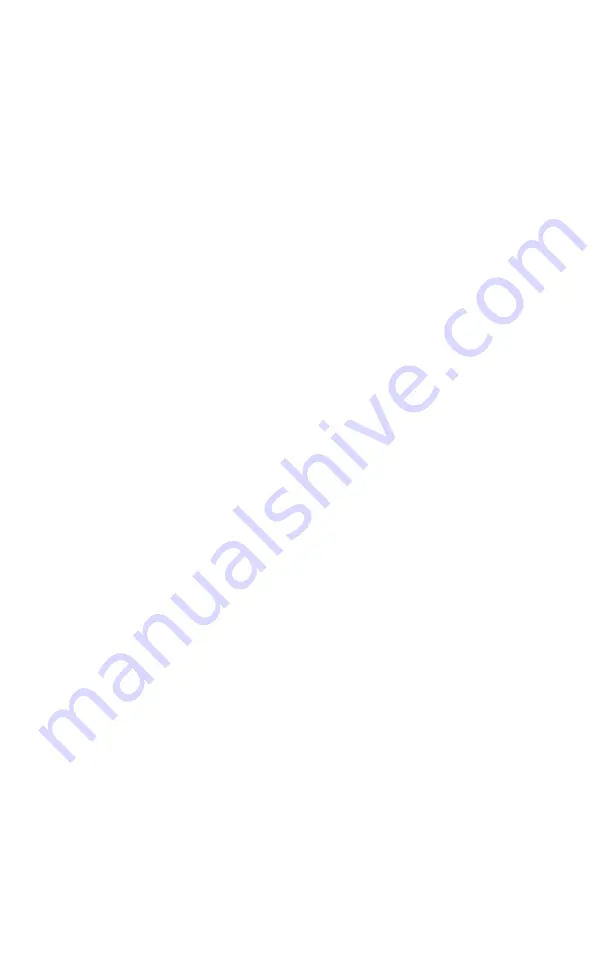
instruction Manual
Section Five
advantageously be increased to about 7 degrees while on larger saws, around
10 inches in diameter, for example, it should be reduced to about 3 degrees.
To minimize the effect of wheel wear, a light finishing cut should be taken
completely around the saw.
Except in the case of very small saws, the same grit and grade of cutting
wheels may be used as for sharpening milling cutters.
While a straight wheel or a cup wheel can be used, some machinists prefer
to grind these saws with the narrow periphery of a dish wheel to avoid
overheating and possibly burning the teeth. For certain smaller saws, a
straight wheel formed to a " V " of approximately 60 degrees will suffice
not only to create the proper rake (IF ANY) on the teeth, but also to
produce a sharp cutting edge while maintaining necessary flute depth and
secondary clearance for all teeth in succession. Small saws may be ganged.
Large metal cutting saws are generally sharpened on special, automatic
saw sharpeners If such a machine is not available, the saws can still be
sharpened on a tool and cutter grinder with the aid of a special fixture,
such as the B988 illustrated on page 102. In this case, they are mounted
horizontally with special stiffening plates and toothrest to index on the
tooth being ground. In the case of high-speed steel saws, to offset the
effect of wheel wear, divide the saw into quarters and start grinding on a
new quarter with each complete rotation of the saw,
8.
CHUCKING REAMERS
(SEE PAGE 67 FOR ILLUSTRATION AND DES
CRIPTION OF A SPECIFIC SET-UP.)
There appears to be no standard method of sharpening reamers. In the
case of machine or chucking reamers of the solid type, the size obviously is
lost as soon as the periphery is touched with a grinding wheel. Inasmuch
as most of the cutting is done by the entering corners of the blades, it is
common practice to sharpen such reamers by simply grinding the lead or
front bevel, usually at an angle of 45 degrees.
When the straight cutting edges become dull to the point of requiring
sharpening, the reamer is ground cylindrically to the next smaller size.
The cutting edges are then "backed off", leaving a primary land from a few
thousandths to about
1
/
32
inch wide depending upon the material being
reamed and the size of the reamer. The reamer will be found to cut
better if it is left with a back taper of about .0005 inch per inch sloped
down to the shank.
Before resharpening chucking reamers of the expansion or adjustable type
are adjusted outward a small amount. They are then ground cylindrically
with a straight wheel to the exact size desired, with the reamer supported
between centers The cutting edges are then "backed off" in a conven
tional manner for milling cutters, leaving a primary land (MARGIN) of
the proper width for the material being reamed.
For steel, the best results are generally obtained with a primary land from
.005 inch to .008 inch wide. For cast iron, a slightly wider land, about
1
/
64
inch, may be used For nonferrous metals like brass and soft bronze, the
land should be reduced to a "white line", no more than .002 inch wide.
9.
HAND REAMERS
(SEE PAGES 65-67 FOR ILLUSTRATION AND DES
CRIPTION OF A SPECIFIC SET-UP.)
Except in the smaller sizes, the majority of hand reamers in use today are
of the expansion or adjustable type. The usual procedure in sharpening
such a reamer is to "set out" the blades a sufficient amount, grind it
- 2 9 -