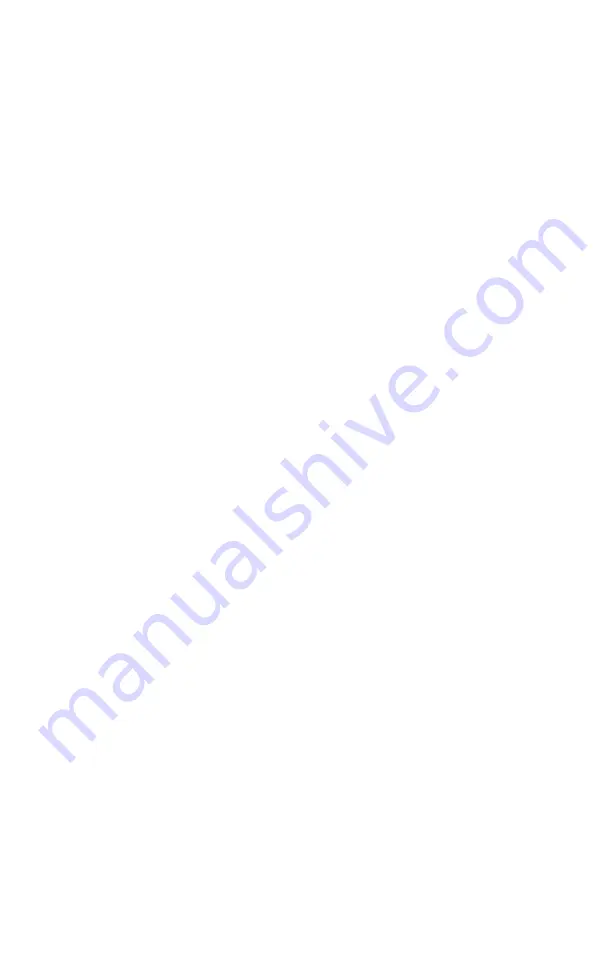
Instruction Manual
Section Five
a horizontal plane, is usually stamped on the cutter in thousandths of an
inch.
The cutter is passed across the wheel face with a steady motion, using the
hand traverse. During the grinding, the Crossfeed must not be changed
as this would change the radial line of the cutter face. Instead, the cutter
is given a slight forward rotation toward the wheel by slightly advancing
the micrometer toothrest. If the cutter is badly worn and there is much
grinding to be done, compensation for wheel wear can be made by resetting
the wheel radially just previous to a light finishing cut. To insure correct
spacing of the teeth using this method, it is advisable to first grind the
backs of the teeth, especially on a new cutter.
2.
FELLOWS GEAR SHAPER CUTTERS
(SEE PAGE 53 FOR ILLUSTRATION
AND DESCRIPTION OF A SPECIFIC SET-UP.)
The cutter is supported on a face plate and tapered stud mounted in the
universal workhead which is swiveled horizontally to an angle of 5 degrees,
representing the rake of the cutter. After grinding, the accuracy of the
cutter angle should be checked with a gauge to be sure it is exactly 5
degrees.
3.
HOBS
(SEE PAGE 51 FOR ILLUSTRATION AND DESCRIPTION OF A
SPECIFIC SET-UP.)
Like formed cutters, the teeth of hobs are made with uniform relief and
are sharpened by grinding radially on the faces of the teeth, using the
beveled side of a saucer wheel, or a " B " face straight wheel. See wheel
shapes, page 110. The most important precaution to be observed in setting
up for this operation is to line up the cutting face of the wheel with the
center of the hob. Also, after each cut, the hob should be revolved toward
the wheel for taking additional cuts, and not adjusted to the wheel by
means of the machine Crossfeed.
In the actual sharpening operation, whether it is done on a tool and cutter
grinding machine or on a special hob grinder provided with automatic work
spindle indexing arrangement, care must be taken to remove the same
amount of stock from each tooth. It can readily be seen that if some teeth
are ground back more than others, those which are left high will have all
the work to do, resulting in irregular cutting action which will affect the
accuracy and finish of the teeth produced.
Hobs of average size are ground successfully with standard cutter sharpen
ing wheels, usually saucer shaped For larger hobs, wheels which are of
slightly less friable aluminum oxide are recommended
4.
FORMING TOOLS
(SEE PAGE 92 FOR ILLUSTRATION AND DESCRIP
TION OF A SPECIFIC SET-UP.)
Most forming tools are used in lathes and are created in the tool room by
too) design engineers for a special application. If they are of slab type,
they will be created by surface grinding activity and ground to measure
ment or to a predetermined template outline on an optical viewing screen.
See Chapter 14, page 92, for application of this task to a K. O. Lee tool
grinder.
If the forming tool is circular, it must be placed on an arbor between
centers and cutting face ground with any existing radial relief, as in the
case of formed cutters. These cutters are created by cylindrical grinding —
usually with a pre-formed straight wheel.
- 3 1 —