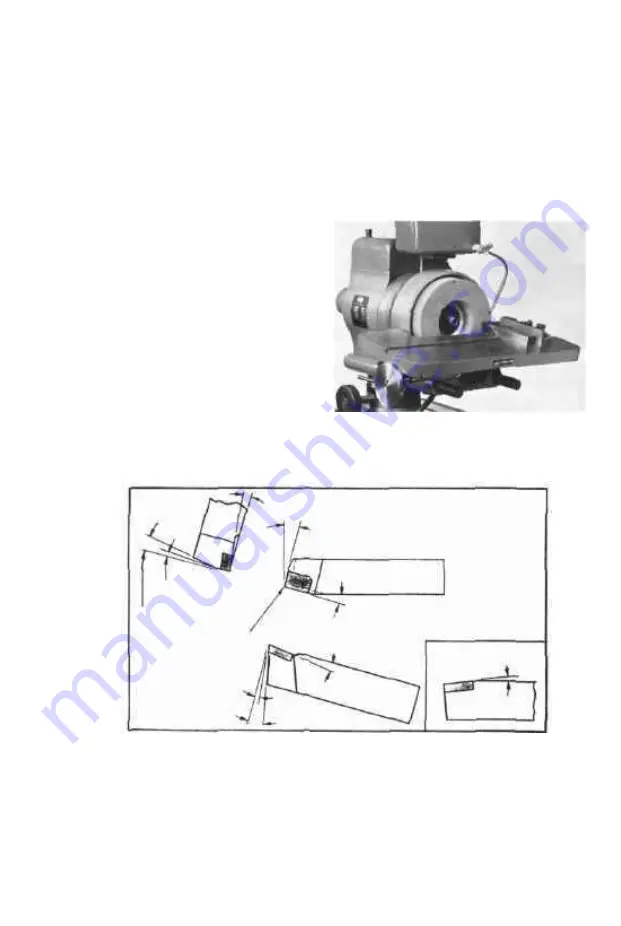
Instruction Manual
Section Five
2. Photo 66 shows the typical set-up for sharpening the periphery of a Wood
ruff Keyseat cutter. These cutters are sharpened only on the periphery
as the sides are relieved by a slightly concave surface. The cutter shank
is most easily held by a collet in a universal workhead. Grinding procedure
is the same as that given for straight tooth side milling cutters in Chapter
5. In general, keyway cutters are of specific width, as are keyseat cutters,
and sharpened only on the periphery.
C. Single Point Tools
USE OF B945 TILTING TABLE FIXTURE:
Although tools with carbide replace
able-tips are widely used nowadays,
there is often need for a fixture which
can be used in grinding precise relief
angles on cemented carbide and high
speed single point tools. The K. 0.
Lee B945 Tilting Table Attachment
'Photo 67) makes it possible to
address a silicon carbide or diamond
recessed wheel at a relief angle on
the end or side of a tool up to 20
degrees. The protractor can be used
to guide the tool toward the wheel
while maintaining a set end cutting
edge angle or side cutting edge angle.
The protractor also has a diamond screw nib for dressing the wheel. Figure
67A gives the nomenclature for a typical single point tool.
PHOTO 67
Figure 67A
—
Tool Angle Nomenclature
General Procedure for Set-up:
(a) Loosen the handle screw underneath the right side of the table; this
allows the table to be tilted. Move the eccentric mounted wheel at
the left of the table to the desired relief angle Lock the handle
screw again. Now re-adjust the whole tilting table slide mechanism
toward the wheel until it is about 1/16 inch from the wheel. Lock the
set screws on the sliding bracket. If several angles will be used
—86—
FRONT R E L I E F
NOSE RADIUS'
B A C K R A K E
NEGATIVE
BACK R A K E
SECONDARY
R E L I E F
S I D E C U T T I N G E D G E A N G L E
SECONDARY
R E L I E F
SIDE RELIEF
E N D C U T T I N G E D G E A N G L E
SIDE R A K E