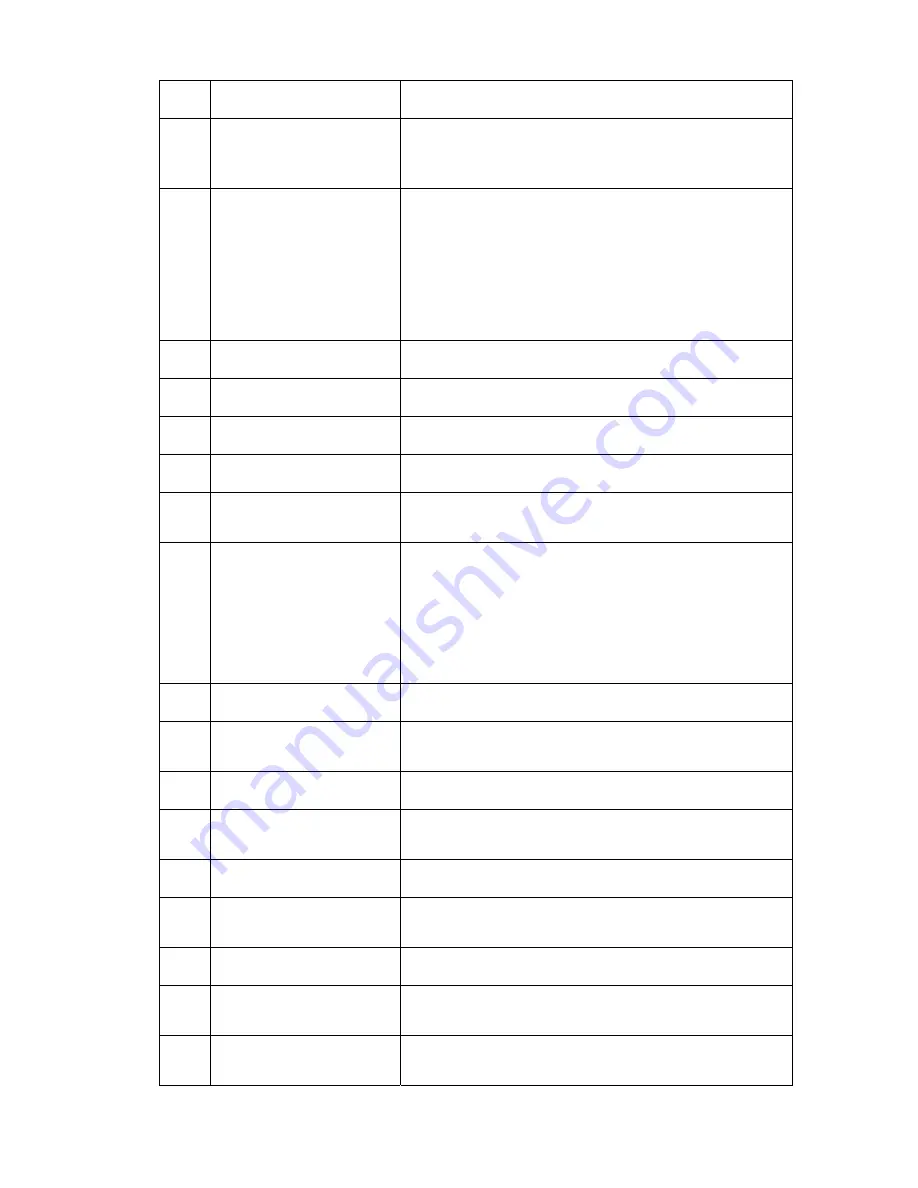
24
15 Front Cover
To support and fix the puller roller frame.
16 Roller
Bracket
To support and fix working roller, as well as to
adjust the axis of roller parallel with the horn
surface.
17 Working
Roller
The working roller is made of special hardened
steel material, and should be handled with care
so
as not to damage the surface. When this roller is
changed or replaced, the axis of roller must be
exactly paralleled with the horn surface to
perform good and uniform operation.
18 Roller Bracket
To support and fix working roller
18-1 Upper Roller Bracket
To support and fix working roller
19 AC Fan
To cooling down the horn.
20 AC Fan
To cooling down the transducer kit.
21 Safety Cover (L)
Cover the transducer kit and electrical parts for
safety concern.
22 Air
Filter
Connect it to an air source with an I.D. 5/16”
(
8
mm
)
hose, then it will filter the air and supply
clean & dry air into the system.
Caution:
The filter may accumulate water in the
cup. As much as possible, the water must be
drained everyday by pressing the push button up.
23 Foot Switch
Controls roller cylinder up-down activities.
24 Solenoid
Valve
Receive instruction from Item 23 foot switch to
drive roller cylinder up-down.
25 Treadle Switch
Switches on the operation of motor and ultrasonic
26 Safety Cover (R)
Cover the motor, transmission mechanism and
electrical parts for safety concern.
27 Foot Switch
Switches on the operation of ultrasonic only.
28 Transformer Unit
Cover
To support and fix the power transformer.
29 Control PCB ASS’Y
Controls the operation of motors.
30 AC
Motor
Rotated the horn-transducer through a timing belt
and a timing pulley.
31 Timing
Belt
A component of transmission mechanisms which
conveys the lower motor’s power to tooling horn.
Summary of Contents for KS-2010
Page 12: ...11 ...
Page 13: ...12 ...
Page 22: ...21 ...
Page 23: ...22 ...
Page 31: ...30 6 4 Wiring Diagram A MAIN WIRING DIAGRAM A 1 KS 72 ...
Page 32: ...31 A 2 KS 85 ...
Page 38: ...37 FUSE FUSE B GENERATOR CIRCUIT DIAGRAM KS 72 KS 85 KS 2010 KS 3010 ...