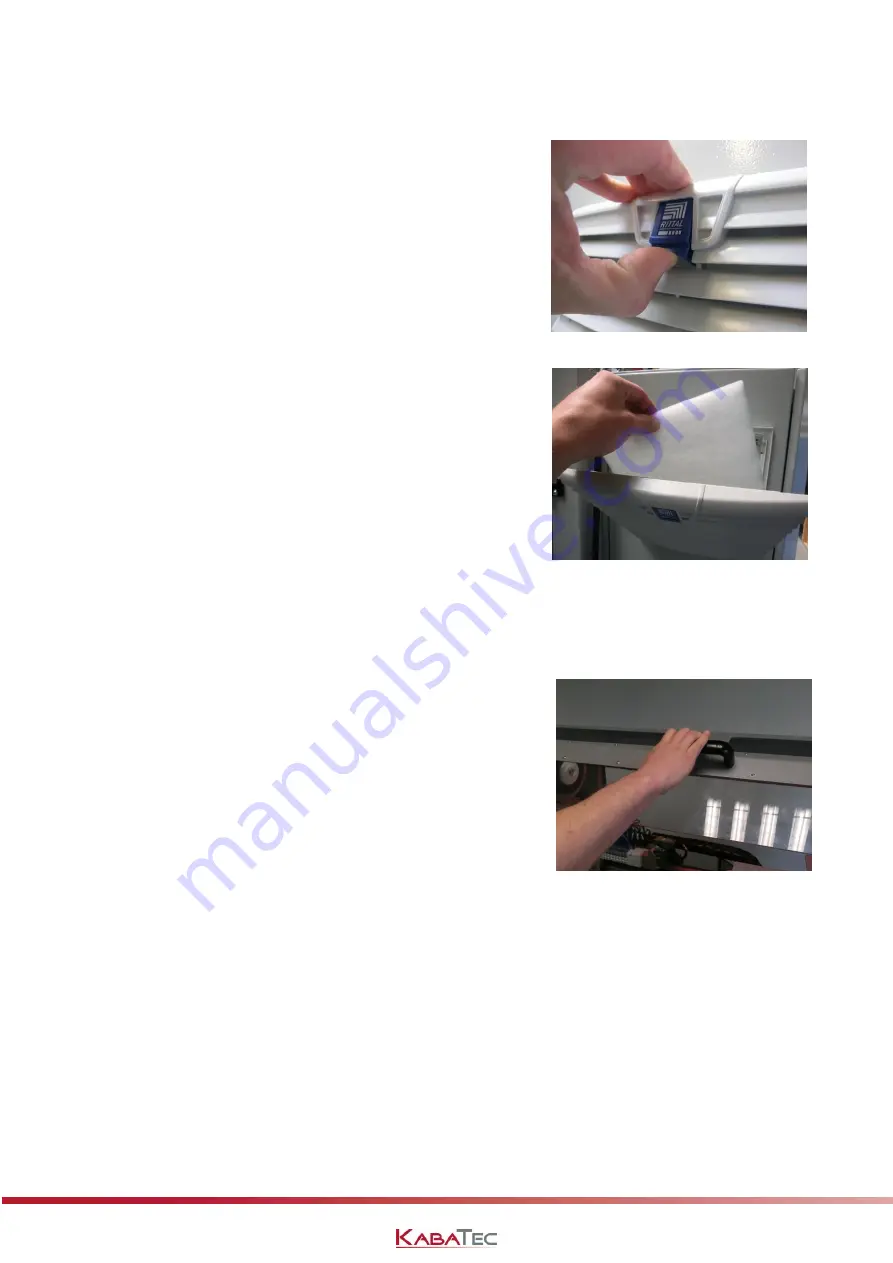
Translation of the original operating manual for the KTS SpeedTec mini
B|HM0SM|00001|V0006|EN
Page
57
6.7 Cleaning the air filter
To unlock the filter grille, pull the blue marker (with the
logo) upwards slightly. The grille can now tilt up by approx.
70°, thereby allowing easy access to the filter mat. The
appropriate cleaning frequency is strongly dependent on
the degree of contamination of the ambient air and cannot
therefore be stated precisely.
6.8 Cleaning the Makrolon discs
Clean the Makrolon safety discs using a commercially-
available disc cleaner. The cleaning interval is dependent
on the place of installation of the machine and cannot
therefore be stated precisely.