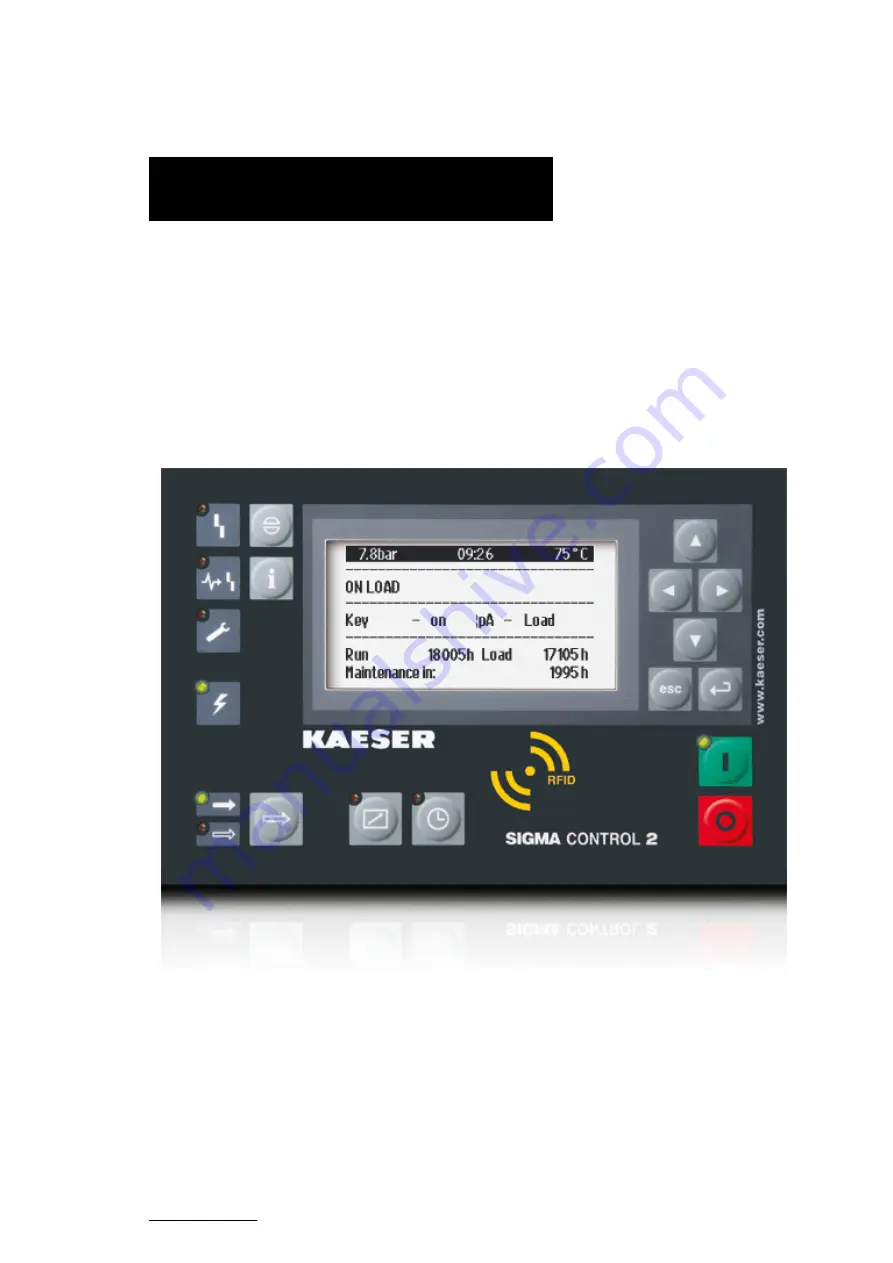
User Manual
Controller
SIGMA CONTROL 2
SCREW FLUID ≥5.0.X
No.: 9_9450 12 E
Manufacturer:
KAESER KOMPRESSOREN SE
96410 Coburg • PO Box 2143 • GERMANY • Tel. +49-(0)9561-6400 • Fax +49-(0)9561-640130
www.kaeser.com
User Manual
Controller
SIGMA CONTROL 2
SCREW FLUID ≥5.0.X
No.: 9_9450 12 E
Manufacturer:
KAESER KOMPRESSOREN SE
96410 Coburg • PO Box 2143 • GERMANY • Tel. +49-(0)9561-6400 • Fax +49-(0)9561-640130
www.kaeser.com