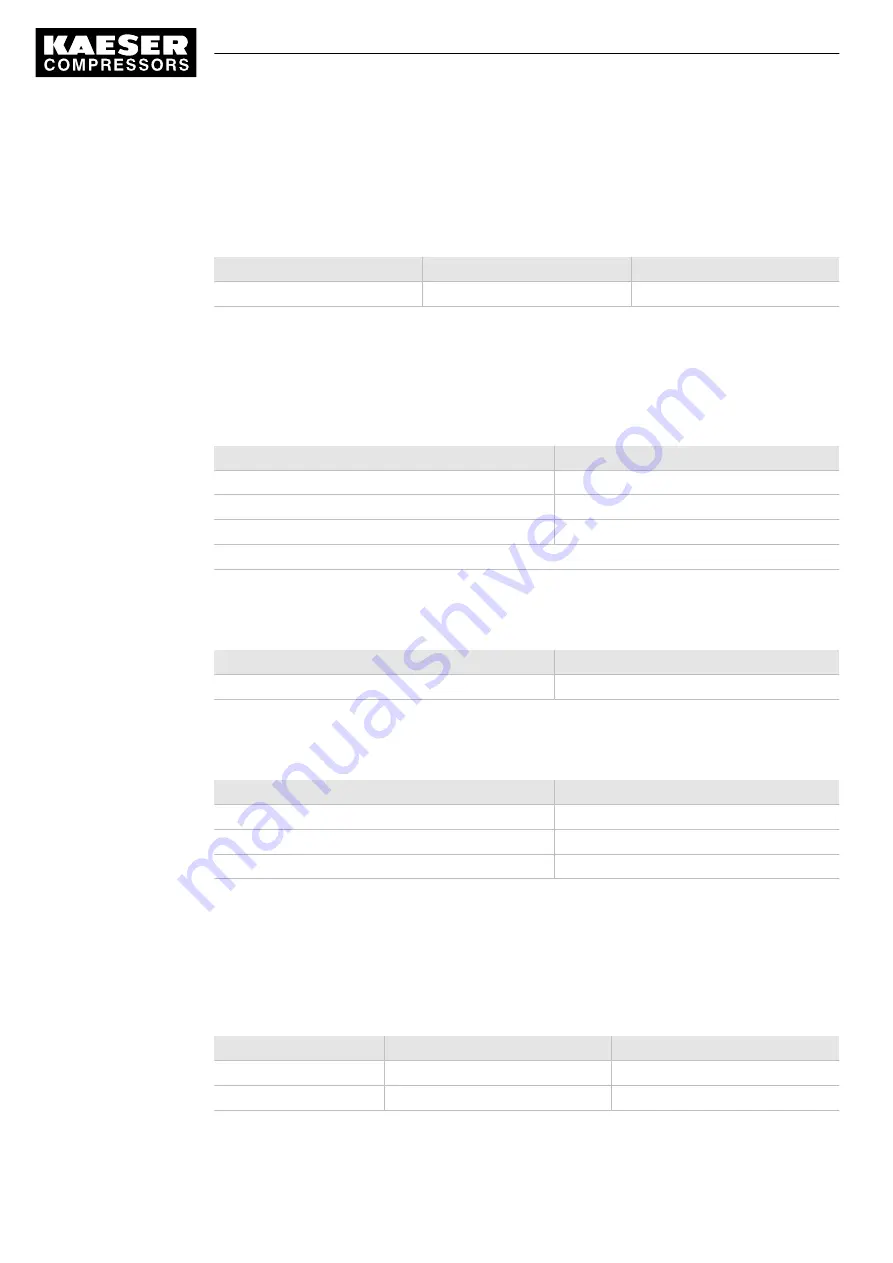
2.7 Options
2.7.1 Option ea
Tool lubricator
Name
Temperature range [°F]
Fluid volume [qt]
Special road breaker lubricant
−13 – 122
2.6
Tab. 32 Road breaker lubricant recommendation
2.7.2 Option ba
Low temperature equipment
2.7.2.1 Ambient conditions
Positioning
Limit value
Maximum altitude AMSL* [ft]
3000
Minimum ambient temperature [°F]
−13
Maximum ambient temperature [°F]
+113
* Higher altitudes are permissible only after consultation with the manufacturer.
Tab. 33 Ambient conditions
2.7.2.2 Air lines frost protection
Antifreeze
Fluid volume [qt]
Wabcothyl
0.3
Tab. 34 Antifreeze recommendation
2.7.2.3 Coolant pre-heating
Coolant pre-heater
Value
Model
DEFA A411235
Voltage [V]
230
Power [W]
550
Tab. 35 Coolant pre-heater
2.7.3 Option ua
Air hose with hose reel
The machine is equipped with an additional discharge valve for the Option "Air hose with hose
reel".
Name
Discharge valve
Compressed air hose
Size ["]
G 3/4
−
Number
1
−
2
Technical Data
2.7
Options
12
SERVICE MANUAL Screw Compressor
M26
No.: 9_9446 01 USE
Summary of Contents for M26
Page 1: ...SERVICE MANUAL Screw Compressor M26 No 9_9446 01 USE...
Page 191: ...13 Annex 13 3 Dimensional drawing No 9_9446 01 USE SERVICE MANUAL Screw Compressor M26 183...
Page 193: ...13 Annex 13 3 Dimensional drawing No 9_9446 01 USE SERVICE MANUAL Screw Compressor M26 185...
Page 194: ...13 Annex 13 4 Electrical Diagram No 9_9446 01 USE SERVICE MANUAL Screw Compressor M26 187...
Page 195: ...13 Annex 13 4 Electrical Diagram 188 SERVICE MANUAL Screw Compressor M26 No 9_9446 01 USE...
Page 196: ...13 Annex 13 4 Electrical Diagram No 9_9446 01 USE SERVICE MANUAL Screw Compressor M26 189...
Page 197: ...13 Annex 13 4 Electrical Diagram 190 SERVICE MANUAL Screw Compressor M26 No 9_9446 01 USE...
Page 198: ...13 Annex 13 4 Electrical Diagram No 9_9446 01 USE SERVICE MANUAL Screw Compressor M26 191...
Page 199: ...13 Annex 13 4 Electrical Diagram 192 SERVICE MANUAL Screw Compressor M26 No 9_9446 01 USE...
Page 200: ...13 Annex 13 4 Electrical Diagram No 9_9446 01 USE SERVICE MANUAL Screw Compressor M26 193...
Page 201: ...13 Annex 13 4 Electrical Diagram 194 SERVICE MANUAL Screw Compressor M26 No 9_9446 01 USE...