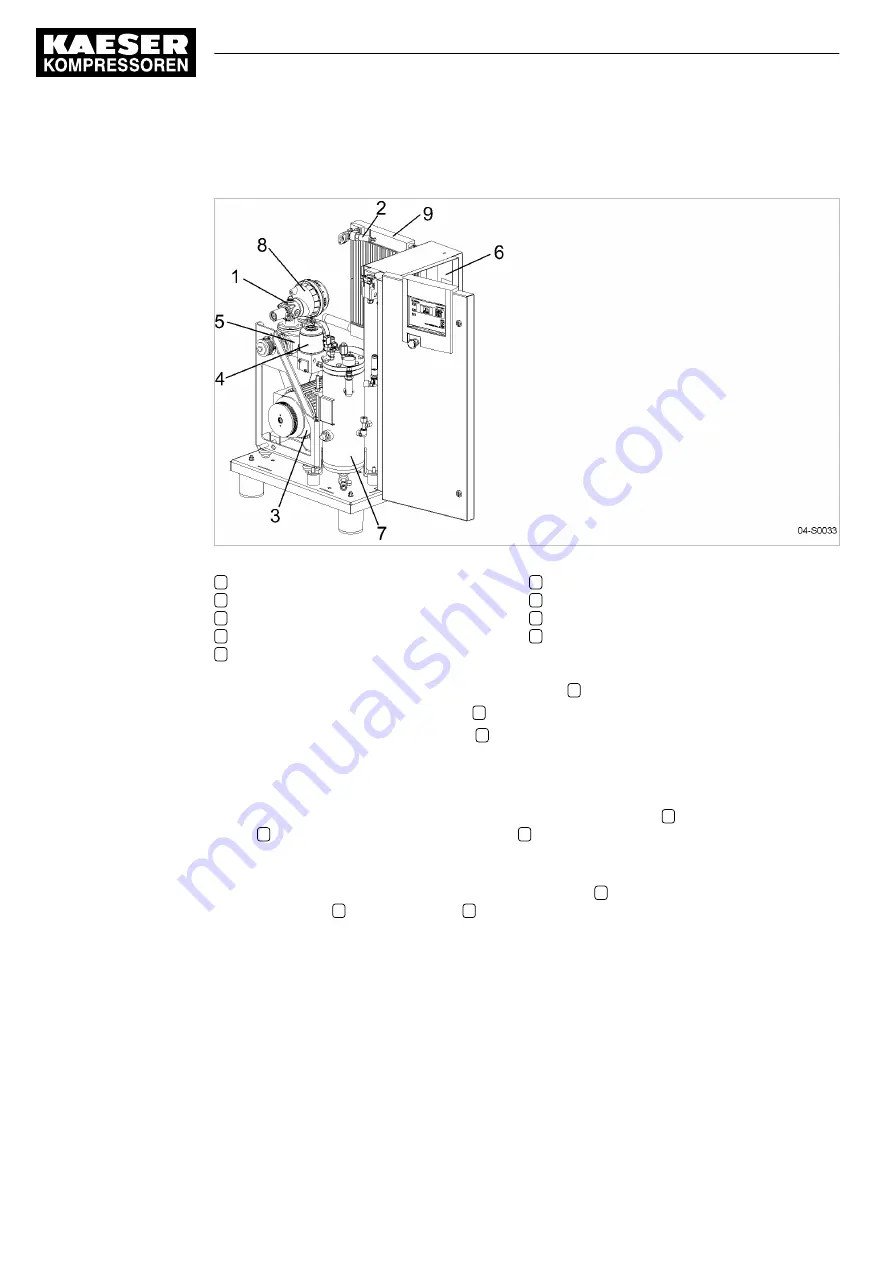
4.2 Machine function
Fig. 6 Machine layout
1
Inlet valve
2
Minimum pressure/check valve
3
Compressor motor
4
Oil filter
5
Airend
6
Control cabinet
7
Oil separator tank
8
Air filter
9
Oil/air cooler
Ambient air is cleaned as it is drawn in through the filter
8
.
The air is then compressed in the airend
5
.
The airend is driven by an electric motor
3
.
Cooling oil is injected into the airend. It lubricates moving parts and forms a seal between the ro‐
tors themselves and between them and the airend casing. This direct cooling in the compression
chamber ensures a very low airend discharge temperature.
Cooling oil recovered from the compressed air in the oil separator tank
7
gives up its heat in the oil
cooler
9
. The oil then flows through the oil filter
4
and back to the point of injection. Pressure with‐
in the machine keeps the oil circulating. A separate pump is not necessary. A thermostatic valve
maintains optimum cooling oil temperature.
Compressed air, freed of cooling oil in the oil separator tank
7
, flows through the minimum pres‐
sure / check valve
2
into the air cooler
9
. The minimum pressure / check valve ensures that there
is always a minimum internal pressure sufficient to maintain cooling oil circulation in the machine.
The aftercooler brings down the compressed air temperature to 9 °F to 18 °F above ambient. Most
of the moisture carried in the air is removed in the aftercooler.
4.3 Safety devices
The following safety devices are provided and may not be modified in any way.
■ EMERGENCY STOP control device:
The EMERGENCY STOP button shuts down the compressor immediately. The motor is stop‐
ped. The pressure system is vented.
4
Design and Function
4.2
Machine function
24
Operator Manual Screw Compressor
SM Tri-Voltage, SIGMA CONTROL 2
9_5875 33 USE