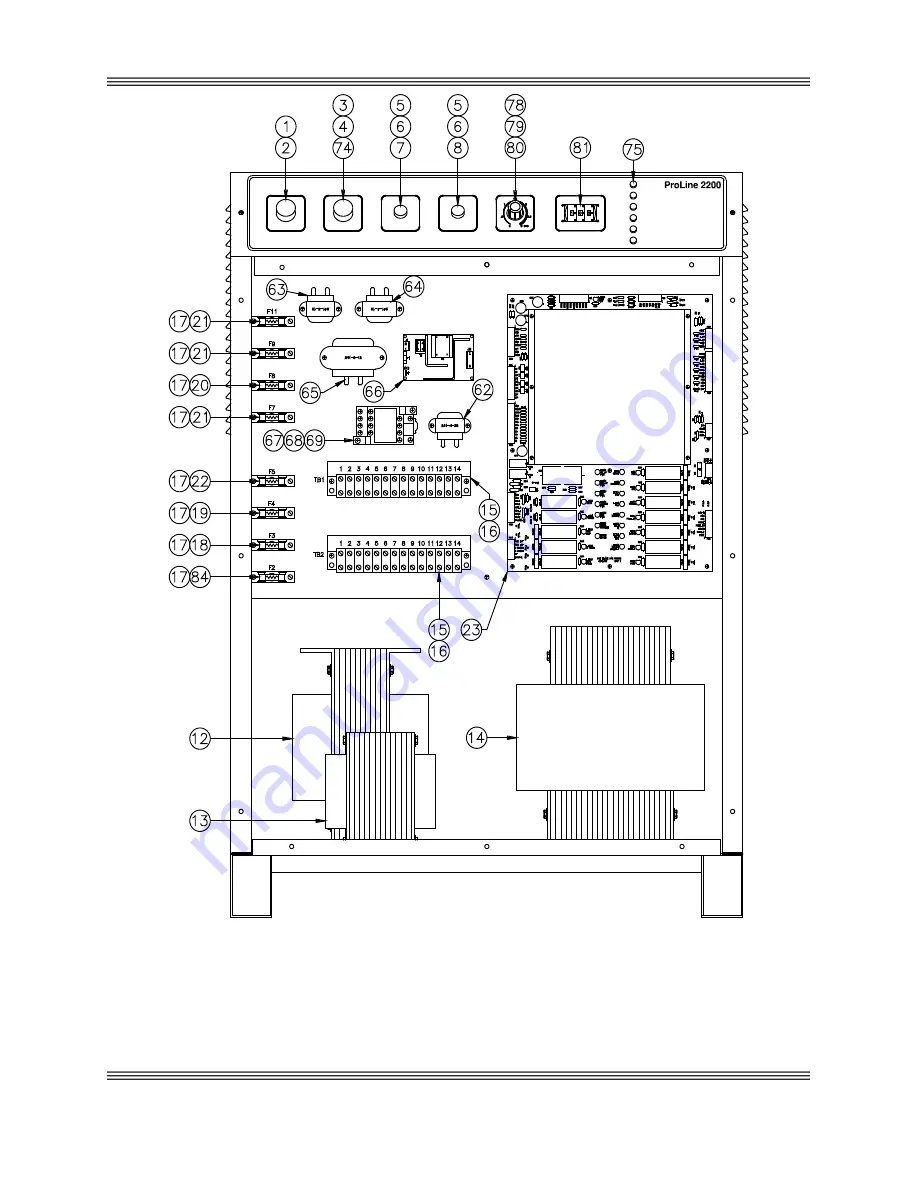
Parts List
ProLine 2200 User’s Manual REV N
This information is subject to the controls of the Export Administration Regulations [EAR]. This information shall not be provided to
non-U.S. persons or transferred by any means to any location outside the United States contrary to the requirements of the EAR.
6-3
Front panel fans not shown (item numbers 42 and 85)
Figure 6-1 Power Supply Front View