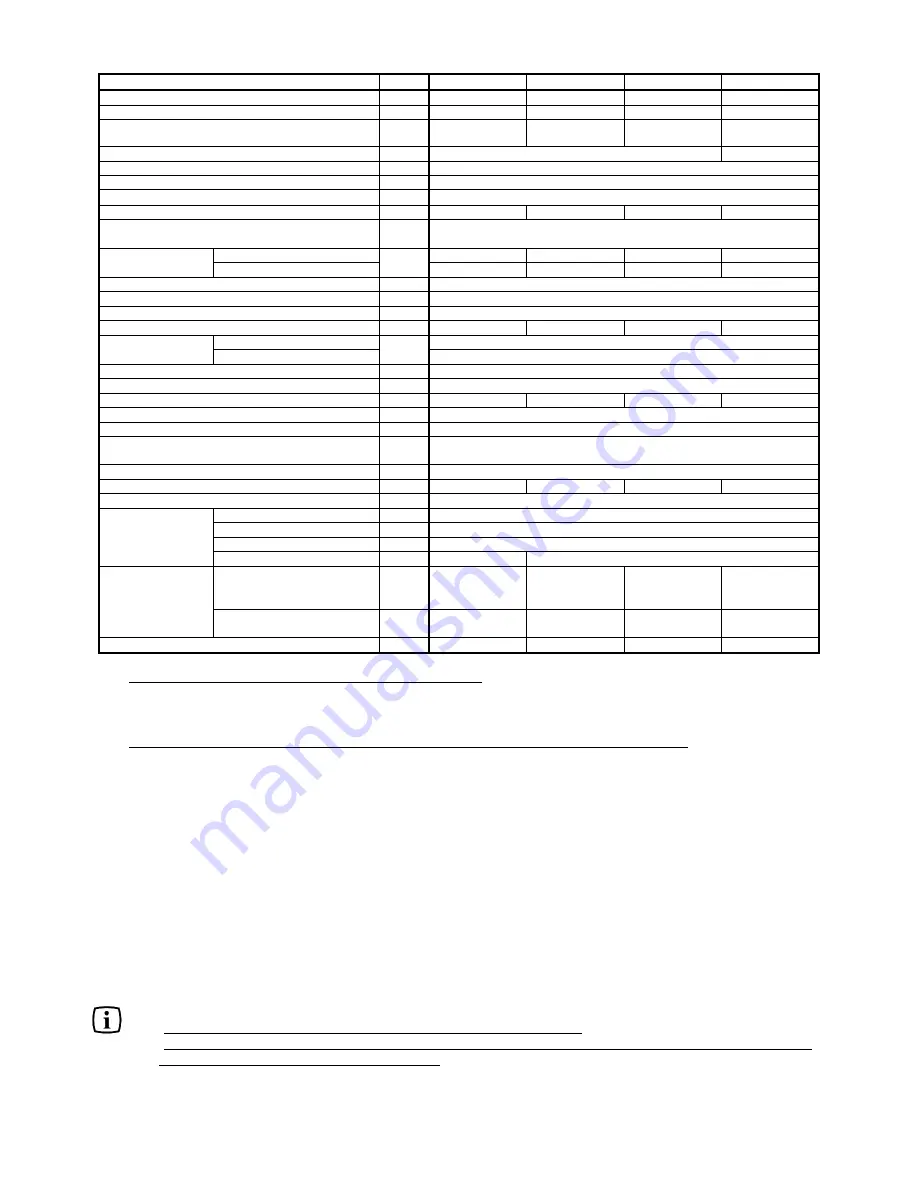
- 9 -
KALVIS-100MG ... -500MG LT 2019.03.18
Table 1 continued
Boiler model
Kalvis-250MG
Kalvis-300MG
Kalvis-400MG
Kalvis-500MG
Nominal power (Q
N
)
kW
250
300
400
500
Minimum power (Q
min
)
kW
75
90
120
150
Burner model
UNI-MAX
250 kW
UNI-MAX
300 kW
UNI-MAX
400 kW
UNI-MAX
500 kW
Control unit
PLUM ecoMAX850P2-O
KEY RK-2006LPGP2
Fuel type
wood pellets *
1
Fuel moisture, no more than
%
10
Pellet fuel size, no more than
mm
6
– 8
Fuel consumption at nominal power
kg/hrs
65
77
114
150
Efficiency factor at Q
N
,
no less than
%
90
Heated area
B class *
2
m
2
2925..8750
3510..10500
4680..14000
5850...17500
C class *
2
1400..4175
1680..5010
2240..6680
2800...8350
Burning time without fuel refill (at Q
N
) *
3
hrs
depending on fuel volume
Boiler class acc. to LST EN 303-5
5
Service life time, no less than
years
10
Water capacity in the boiler
l
1200
1400
1400
1600
Water pressure in
the boiler
no less than
bar
(MPa)
2,5 (0,25)
no more than
4,0 (0,4)
Maximum outflowing water temperature
ºC
90
Min. return water temperature during operation
ºC
50
Hydraulic resistance (Δt=20ºC/Δt=10ºC)
mbar
0,127
0,136
0,185
0,254
Working environment temperature
ºC
3 - 30
Draught from boiler *
4
Pa
180 *
4
Exhaust smoke temperature at nominal power, up
to
ºC
130
Operation voltage
V
230 AC
Electrical power
W
585
1111
1411
1466
Electrical protection class
IP 20
Connection branch
pipe dimensions:
flue pipe (relative diameter)
mm
Ø 250
flue pipe branch pipe
mm
Ø 305
water discharge
mm (col)
25 (1")
heating system
mm (col)
50 (2")
65 (2½")
Overall
dimensions, no
more than:
height (H)
breadth (B)
length (L)
mm
mm
mm
1900 *
5
1440 *
5
3320 *
5
2170
1600
4730
2220
1760
4970
2220
1760
5270
breadth without el. panel (B1)
length without burner (L1)
mm
mm
1140 *
5
2990 *
5
1260
3110
1420
3350
1420
3650
Mass, no more than (
10%)
kg
2500 *
5
2580
3000
3420
*
1
Wood pellet quality shall be in line with DIN 51731, DIN plus standards.
*
2
Energy quantity calculated according to the requirements of STR 2.01.02:2016 Projecting and Certification of Energy Performance of
Buildings, expressed for Energy Performance of Buildings Classes B and C.
*
3
Using Ø8 wood pellets (7 % moisture and 17,5 MJ fuel heating value).
Fuel load combustion duration depends on fuel type, moisture, outside temperature, heat consumption.
*
4
Permanently constant draught from the boiler has to be ensured, so it is necessary to install smoke exhauster. For control of the smoke
exhauster, frequency converter and differential pressure sensor are recommended.
*
5
Dimensions are determined for a particular order at the time of
Peephole installed in the rear of the boiler is used to observe the combustion process visually.
For draught measurement in the boiler, branch pipes are installed on the both sides of the boiler, under
trimming covers, one branch pipe is used to pull a tube on, other end of the tube is led to the differential
pressure gauge installed in the control box (
see fig. 6
).
On the top of the rear wall of the boiler, smoke collector is installed, having three holes directed towards the
rear and the both sides. Flue pipe branch pipe is attached to one of the holes, selecting the direction, the
remaining two holes are covered with sooth removal lids.
In the boilers
Kalvis-300MG ...-500MG,
burner
UNI-MAX 500 kW
...
300 kW
is installed on rails
(
see fig. 3
).
More information about the burner and controller can be found in:
-
„
ECO-BURNER UNI-MAX 100-1000 kW Pellet Burner User Manual
“.
-
„
Burner control unit PLUM ecoMAX850P2-O (or KEY RK-2006LPGP2) for Pellet Boilers, Installation,
Service, Maintenance And Operation Manual
“.
Summary of Contents for Kalvis-100MG
Page 2: ......