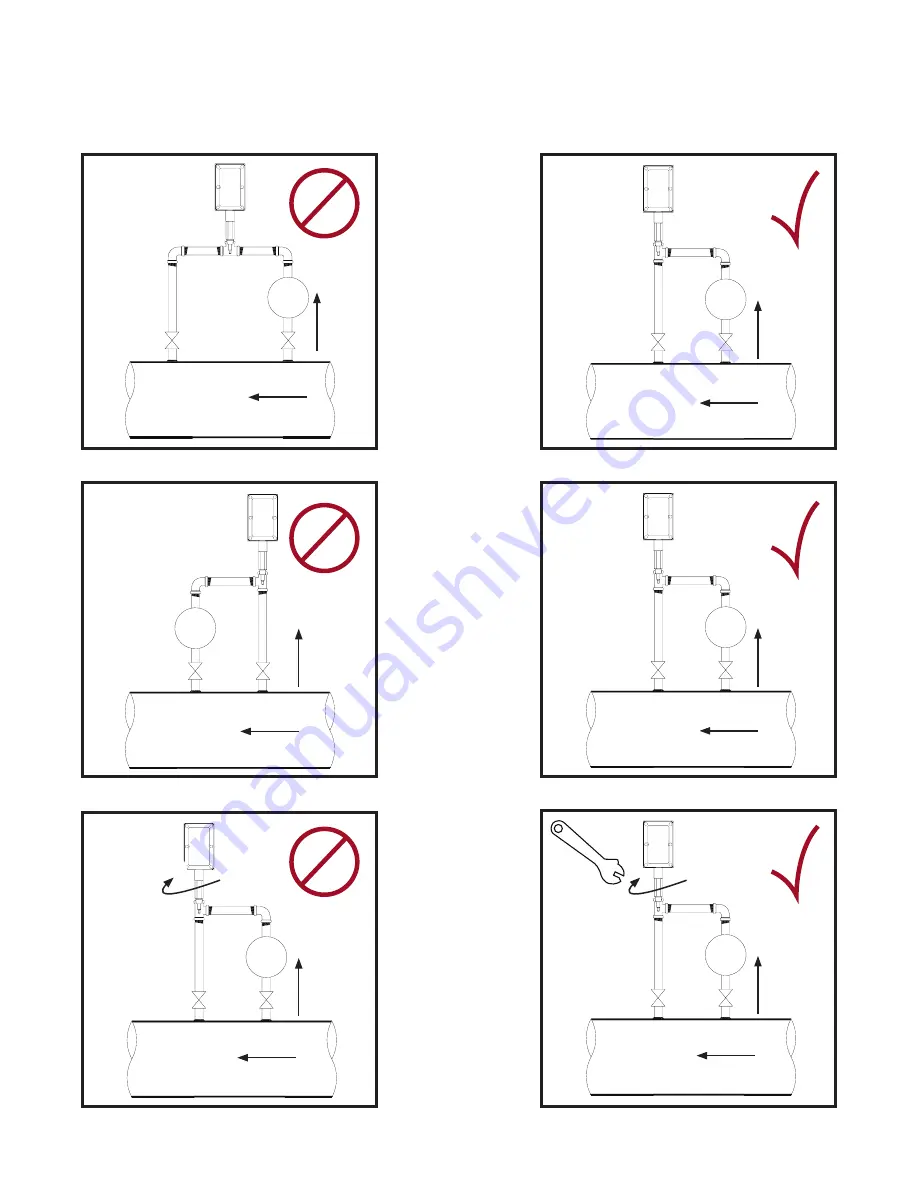
5
OODMANUAL 0720
KAM CONTROLS, INC.
I
P
I N S TA L L AT I O N C O N T I N U E D
INSTALLATION DO’S AND DON’TS
P
FLOW
FLOW
P
FLOW
FLOW
P
FLOW
FLOW
P
FLOW
FLOW
P
FLOW
FLOW
P
FLOW
FLOW
DO NOT install the
fast loop OOD™
sensor in a straight
portion of pipe.
It needs to be
mounted off the
bend opposite the
pump.
DO NOT install
the OOD™ sensor
with the lens facing
directly into the
flow. If the product
has particulate
matter in the fluid,
like sand, this will
sandblast the lens
and could cause
premature failure.
DO NOT attempt to
screw the OOD™
sensor either in
or out by hand.
Always use a
1 1/4" or 1 3/8"
wrench on the
wrench flat below
the electronics
enclosure.
I