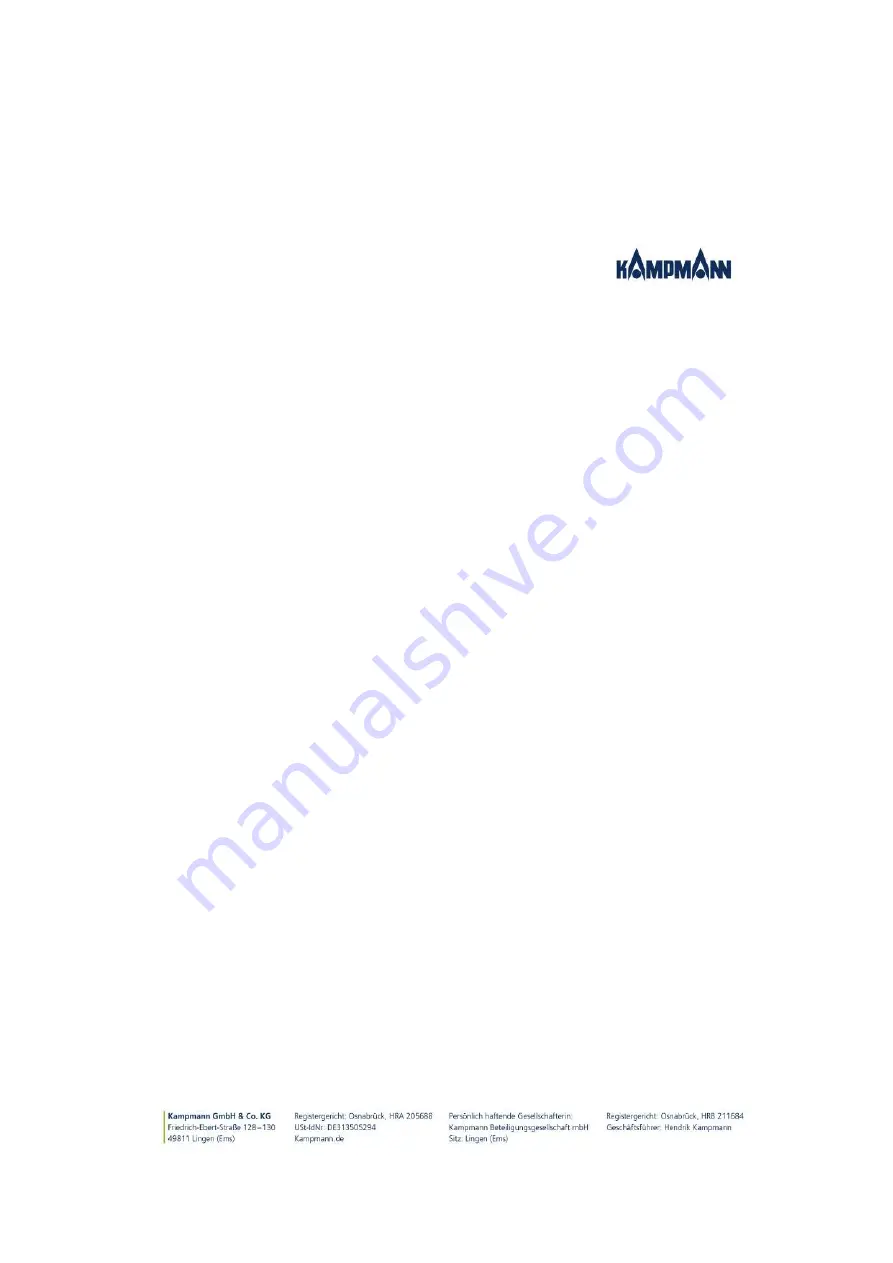
KaCool D HC
Assembly, installation and operating instructions
40
12
Certificates
EU-Konformitätserklärung
EU Declaration of Conformity
Déclaration de Conformité CE
Deklaracja zgodno
ś
ci CE
EU prohlášení o konformite
Wir (Name des Anbieters, Anschrift):
KAMPMANN
GMBH & Co. KG
We (Supplier’s Name, Address):
Friedrich-Ebert-Str. 128-130
Nous (Nom du Fournisseur, Adresse):
49811 Lingen (Ems)
My (Nazwa Dostawcy, adres):
My (Jméno dodavatele, adresa):
erklären in alleiniger Verantwortung, dass das Produkt:
declare under sole responsibility, that the product:
déclarons sous notre seule responsabilité, que le produit:
deklarujemy z pe
ł
n
ą
odpowiedzialno
ś
ci
ą
,
ż
e produkt:
deklarujeme, v
ě
domi si své odpov
ě
dnosti, že produkt:
Type, Modell, Artikel-Nr.:
KaCool D HC
525***
Type, Model, Articles No.:
Type, Modèle, N° d’article:
Typ, Model, Nr artyku
ł
u:
Typ, Model,
Č
íslo výrobku:
auf das sich diese Erklärung bezieht, mit der / den folgenden Norm(en) oder normativen
Dokumenten übereinstimmt:
to which this declaration relates is in conformity with the following standard(s) or other normative document(s):
auquel se réfère cette déclaration est conforme à la (aux) norme(s) ou autre(s) document(s) normatif(s):
do którego odnosi si
ę
niniejsza deklaracja, jest zgodny z nast
ę
puj
ą
cymi normami lub innymi dokumentami
normatywnymi:
na který se tato deklarace vztahuje, souhlasí s následující(mi) normou/normami nebo s normativními
dokumenty:
DIN 1946-4
Raumlufttechnische Anlagen in Gebäuden und Räumen
des Gesundheitswesens
VDI 6022 Blatt 1
Hygieneanforderungen an raumlufttechnische Anlagen
und Geräte
DIN EN 1397
Wasserübertrager – Wasser-Luft-Ventilatorkonvektoren –
Prüfverfahren zur Leistungsfeststellung
DIN EN 55014-1; -2
Elektromagnetische Verträglichkeit
DIN EN 61000-3-2; -3-3
Elektromagnetische Verträglichkeit