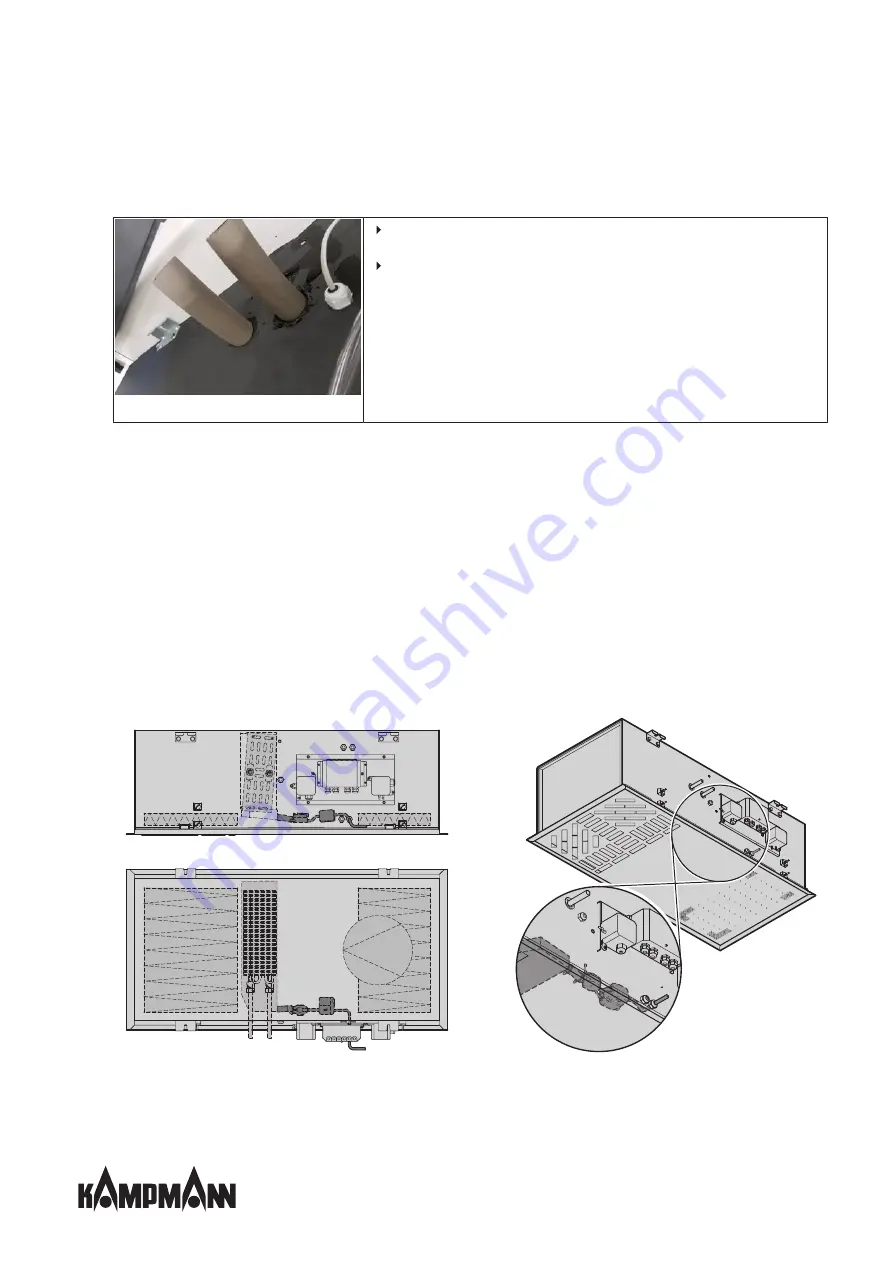
KaCool D HC
Assembly, installation and operating instructions
22
6.5.3 Insulating the pipework
Fig. 10: Insulating the pipework on site
Apply adhesive to the front cross-section of the diffusion-tight insulation (by
others).
Push the diffusion-tight insulation (by others) along the pipes as far as the
wall of the housing and press it to produce an adhesive joint.
6.5.4 Condensation connection
6.5.4.1
Condensation drain with natural gradient
A condensate drain needs to be connected and appropriately fixed to a condensate drain spigot on the unit (15 mm drain).
Ensure that the gradient is at least 1 cm/m, without restrictions and without rising sections of pipe, to ensure the drainage of
condensate from the basic unit providing no adequately sized condensate pump has been fitted (in accordance with DIN EN
12056; formerly: DIN 1986-100). However, no condensate pump is factory-fitted as standard. Take into account all applicable
regulations, such as the use of a ball trap, when connecting the condensate line to the sewer system. Protect the trap from
drying out. The suction effect of the fan on the condensate drain neck could otherwise produce troublesome odours. Consider
using water vapour-impermeable insulation depending on the pipe material used for the condensate drain. You will need a
condensate pump (permanently installed in the basic unit) if a natural gradient is impossible on site. This is used to pump the
condensate into higher collection or discharge equipment. When delivered, the condensate pump and float switch is factory-
fitted to the unit.
Fig. 11: Correct condensate drainage