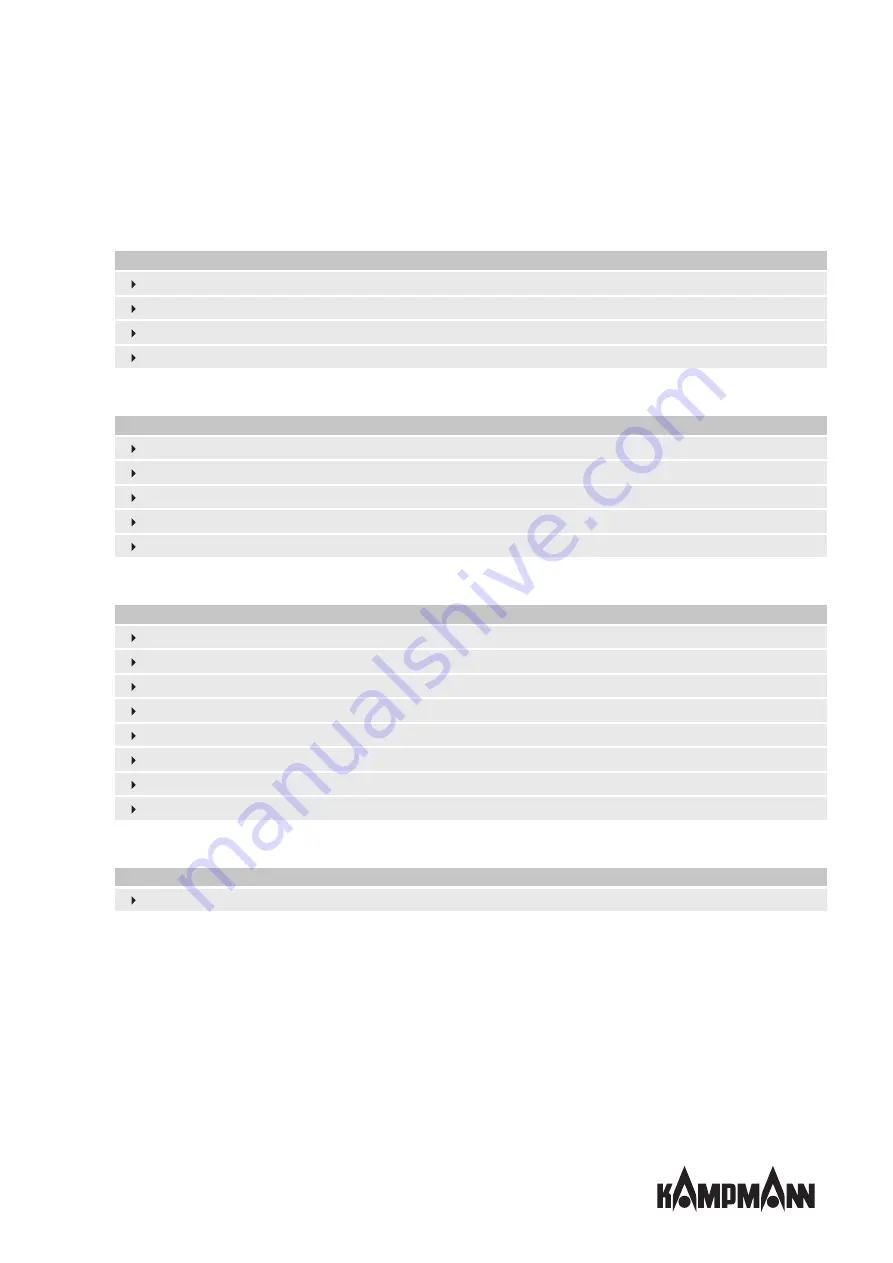
TIP
Assembly, installation and operating instructions
33
8
Pre-commissioning checks
Before initial commissioning, check whether all the necessary conditions have been met so that the unit can function safely
and properly.
Structural tests
Check that the unit is securely standing and fixed.
Check the horizontal installation/suspension of the unit.
Check whether all components are properly fitted.
Check whether all dirt, such as packaging or site dirt, has been removed.
Electrical tests
Check whether all lines have been properly laid.
Check whether all lines have the necessary cross-section.
Are all wires connected in accordance with the electric wiring diagrams?
Is the earth wire connected and wired throughout?
Check all external electrical connections and terminal connections are fixed in place and tighten if necessary.
Water-side checks
Check whether all supply and drainage lines have been properly connected.
Fill pipes and unit with water and bleed.
Check whether all bleed screws are closed.
Check leak tightness (pressure test and visual inspection).
Check whether the parts carrying water have been flushed through.
Check whether any shut-off valves fitted on site are open.
Check whether any electrically actuated shut-off valves have been properly connected.
Check whether all valves and actuators are working properly (note permitted mounting position).
Air-side checks
Check whether there is unimpeded flow at the air inlet and outlet.
Once all checks have been completed, initial commissioning can be carried out in line with
Summary of Contents for TIP
Page 2: ......
Page 40: ...TIP Assembly installation and operating instructions 40 12 Certificates...
Page 45: ......
Page 46: ......
Page 47: ......