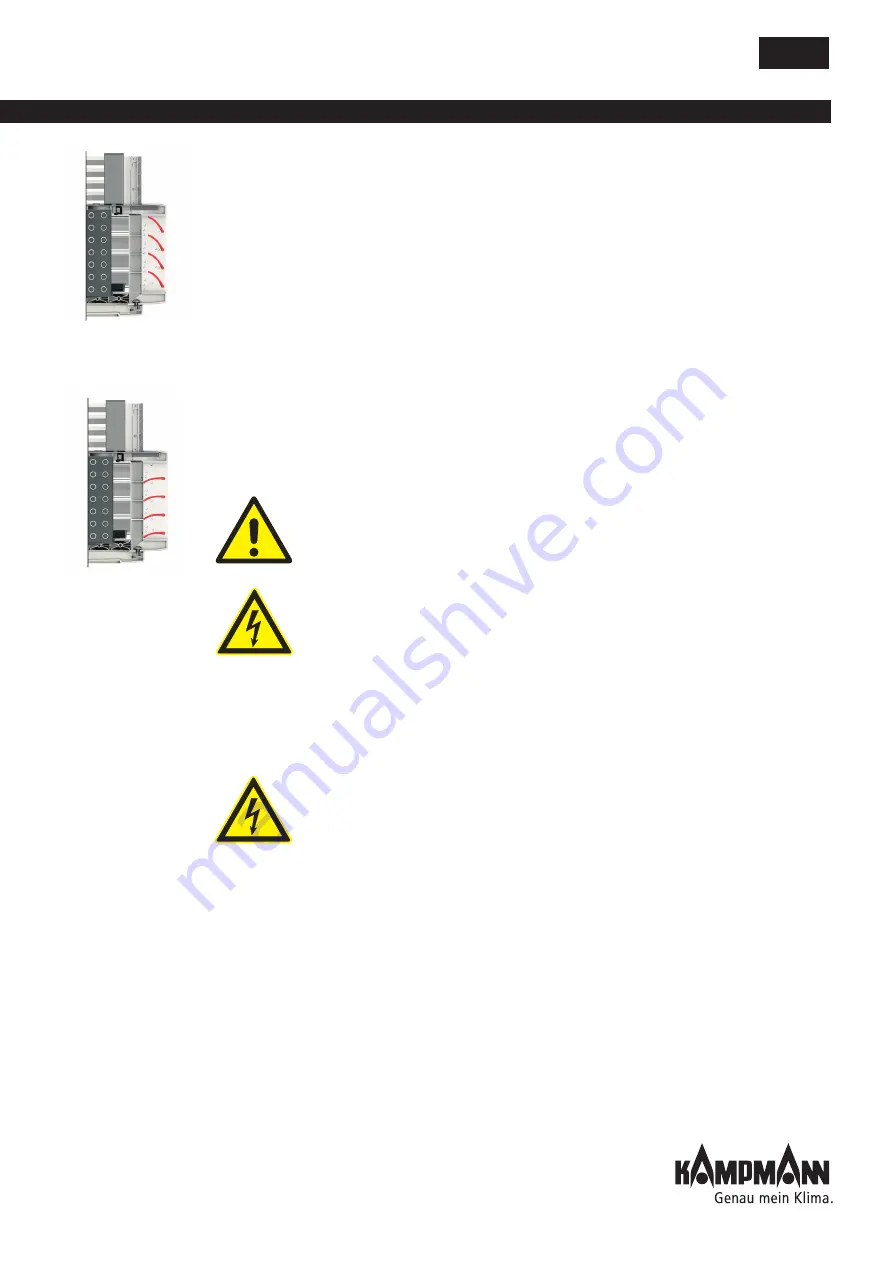
35
Ultra
1.54
Comfortable indoor climate in high-end interiors
Installation and operating instructions
11.2 Commissioning
Proceed as follows after conducting the above checks:
• Open the valves on the heating system.
• Properly fill the pipes and heat exchanger, if they have been drained after
installation.
• Ensure that the entire system is vented.
• Check that all pipes and valves are leak-tight.
• Start up the Ultra by applying voltage to all electrical components.
• Check the direction of rotation and all speed levels or the speed range
(0-100 %).
11.3 Post-commissioning checks
Perform the following checks after commissioning the unit:
Are the fans switched off permanently by the thermal contact (the
exception are the power module and stage switches 30773 and
30774)?
To do so, disconnect a wire from terminal TK of the stage switch (Danger:
230 V!). All the fans should switch off immediately. The operating readiness
indicator must go out on the stage switch. Reconnect the wire to terminal
TK. The fans should not start up again. Reset the stage switch and switch
it on again. The fans should restart. Briefly disconnect the connecting wires
of all thermal contacts individually to check that all thermal contacts are
correctly wired.
If the fan switched off by the thermal contact (applies to the
0 – 100 % variable power module)?
To do so, disconnect a wire from terminal TK of the motor of the Ultra to
be checked (Danger: 230 V!). The fan should switch off immediately. The
fault should be reported via the potential-free NCC contact and trigger that
the fan switches off, depending on the control used. Reconnect the wire
to terminal TK. Depending on the control used, the fan should start up
again or may not start up again (in the event of the fan being switched off
permanently) Perform this check for every single Ultra to monitor all units.
Are the fans in all units rotating in the correct direction at all
switching stages?
The direction of rotation is indicated by the arrow. Make sure that the fan
is drawing in air. Swap 2 phases on the stage switch if all three-phase fans
are rotating in the wrong direction at all fan stages. Swap the auxiliary
phase connections (Z1, Z2) if the ASC single-phase motors are rotating in
the wrong direction. Check the wiring of the incorrectly rotating fans if
individual fans are rotating in the wrong direction.
Heating mode:
position diagonally down
(factory setting)
Cooling mode:
horizontal position